Featured Part / / Innovative Robotics With MJF
Print-in-Place Mechanical Assemblies for Accelerated Innovation
Redesign of Robotic Assembly / / Reduced Component Count and Assembly Steps with Multi Jet Fusion
In this featured post, Mechanical Engineer Anne Pauley, examines and redesigns a previously injection molded robotic assembly using additive manufacturing. From reverse engineering, to manufacturing technology selection, to the identification of the potential for robotic innovation using Multi Jet Fusion (MJF) technology.
The Project // Redesigned Assistive Robot Finger
Additive Technologies Featured / / HP Multi Jet Fusion (MJF) / / Using Nylon 12
Original Materials / / 12 Off-The-Shelf Hardware & 5 Injection Molded System Components
Redesign Materials / / One Print-In-Place Assembly, One Small Hardware Access Cover & One Steel Spring
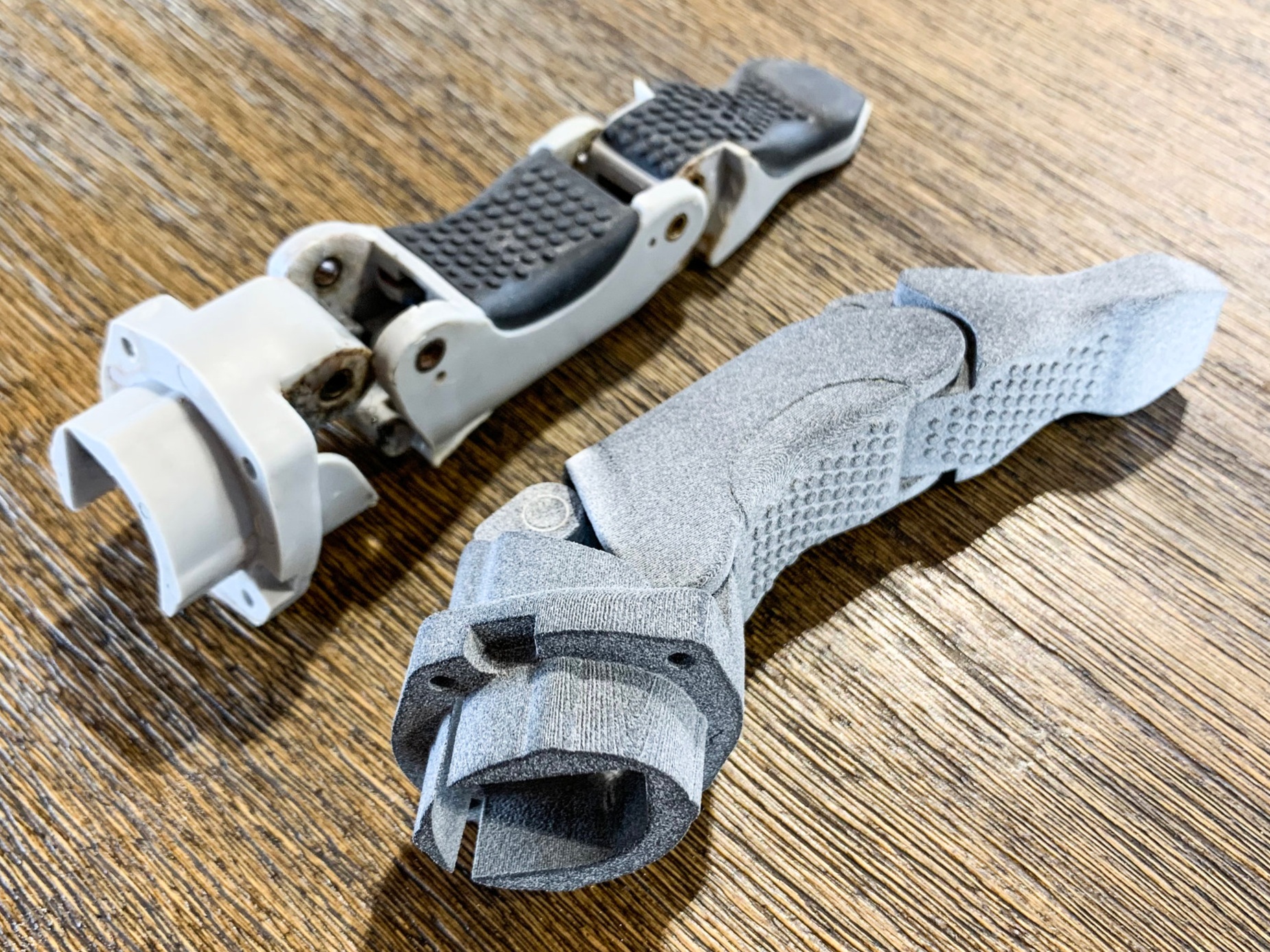
Left – Original / / Injection Molded
Right – MJF / / Print-In-Place Assemblies
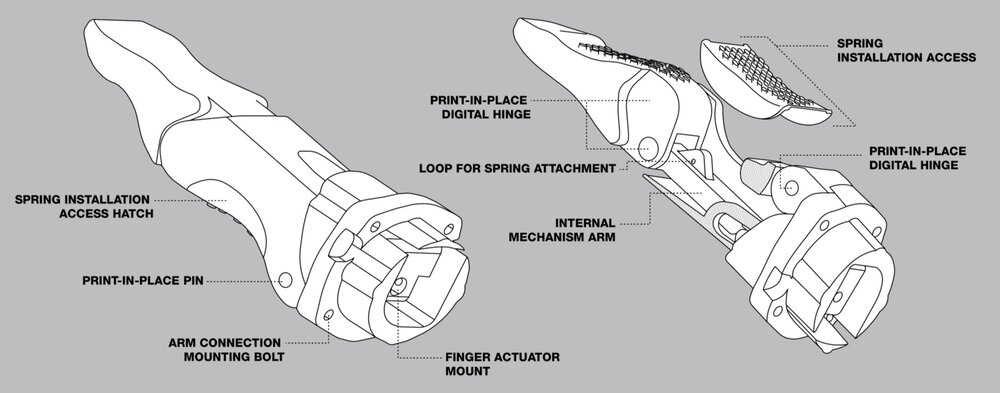
Key Design Features of the New Additively Manufactured Assembly
3D Printing vs. Injection Molding / / Read More
The Part / / Mechanical Assembly of a Robotic Finger
Mechanical Engineer Anne Pauley on Fathom’s Design & Engineering team redesigned a mechanical assembly of an assistive robot for the MJF process. She worked directly with the end-user, an individual with Muscular Dystrophy (MD) to test the prototypes.
The original design is an assembly of five injection molded plastic components and 12 off-the-shelf hardware components. The goal was to simplify the design while providing an easy route to customization and cost effective low volume manufacturing. By employing additive, the need for a costly injection mold tool was removed. Further design optimization consolidated the assembly. This new design improved reliability and reduced manual labor assembly costs.
She utilized the capability of the MJF process to print with no support material to manufacture a pre-assembled mechanical finger. To design the assembly, parametric modeling in Fusion 360 was used to model the mechanical components of the finger, maintaining the necessary mounting points for installation onto the 5-axis arm. The exterior geometry of the shells was left unchanged.
While reverse-engineering the assembly, it was determined that machining tolerances were not critical to the functionality of the finger. The original mechanism hinges were snap-fit injection molded plastic. The end-use application of the finger as a user-controlled assistive robot also did not require the same level of positional accuracy and mechanical load in the joints as industrial robotics.
Technology Selection for Redesign // 3D Printing to Rapidly Iterate and Refine Design Details with MJF
Multi Jet Fusion was chosen as the ideal application for the part due to the ability to use Nylon 12. Nylon 12 is a durable material with excellent mechanical properties frequently used by the Fathom team for short to medium production runs while maintaining shorter cycle times. The MJF printed prototypes were used to iterate quickly, testing the fit and function of the assembly with focused design changes. Utilizing this process also solves the problem of tedious removal of printed hinges. As powder-bed technologies allow material to be evacuated quickly from interior geometry after printing.
One of the primary goals of this iterative process was to consolidate components and reduce the need for hardware and assembly. The original design had 12 pieces of off-the-shelf hardware and five injection molded custom components. Assembly was difficult and time consuming. In the redesigned MJF assembly, there is one print-in-place assembly, one small hardware access cover and one steel spring. The assembly process of this design was reduced to only two steps: inserting the steel spring and attach the cover to hide the hardware.
The Value / / Rapid Prototyping and Part Consolidation
The ability to print pre-assembled mechanical components with MJF offered the opportunity to drastically reduce the need for manual assembly with print-in-place mechanisms. The fast 2-day turnaround of MJF parts at Fathom’s additive production facility made it possible for the engineer to achieve an accelerated development timeline with five iterative prototypes in two weeks. The additive manufacturing expertise of Fathom’s Design and Engineering team made it possible to take full advantage of the capabilities of the Multi Jet Fusion technology. The total cost of the assembly including 3D printing and hardware was under $90 for quantity one and under $70 each for a quantity of three or more.
Parts As Soon As 2 Days / / Instant MJF Quotes
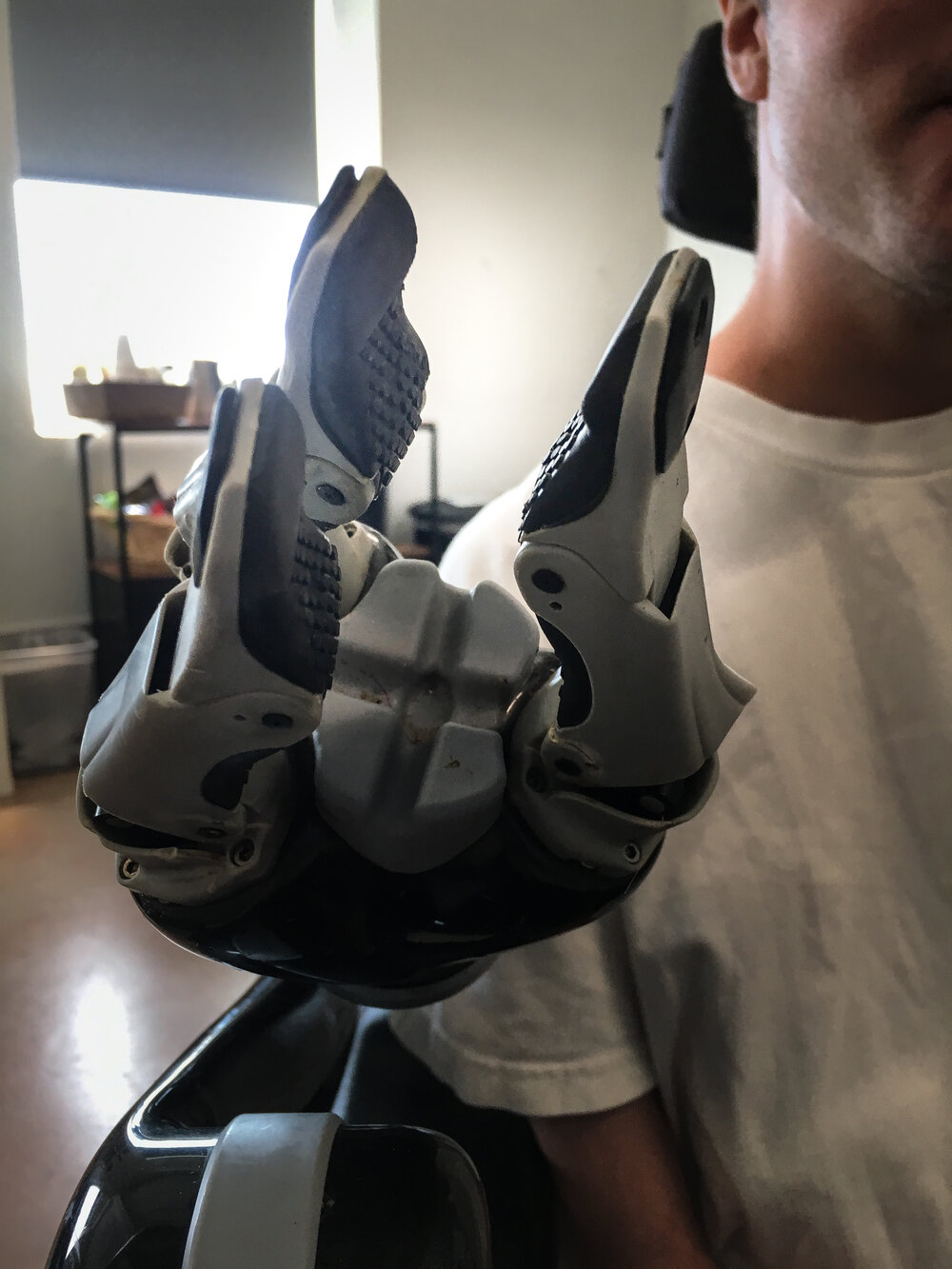
Assistive Robot with Original Parts / / Stay Tuned For Final MJF Parts
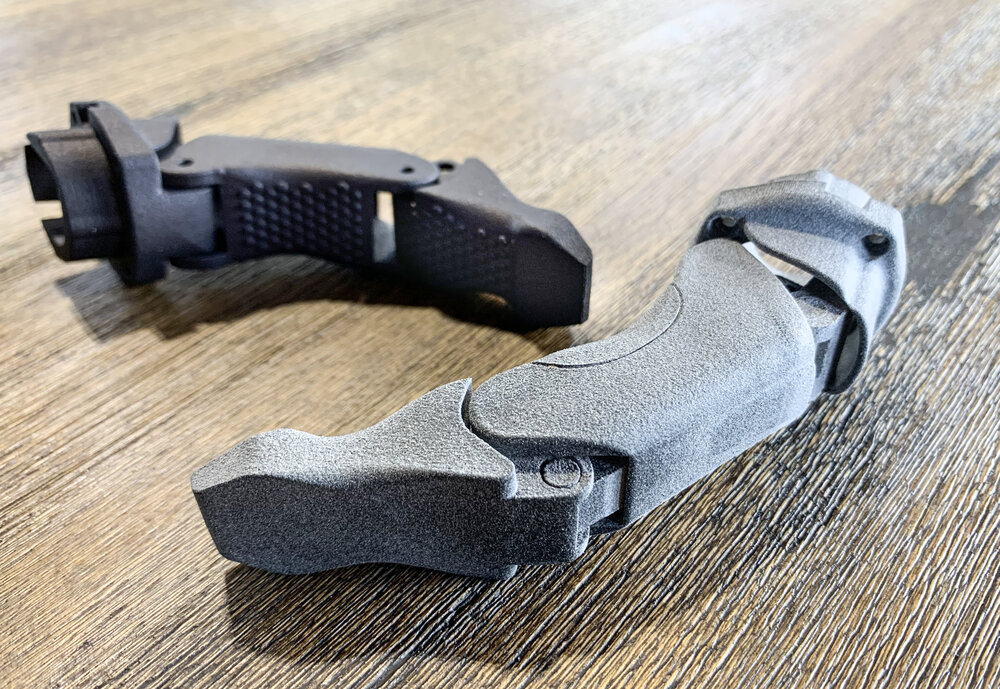
Comparison of Original CAD Design & Refined Design Using MJF
Design Guidelines // Fathom’s application and engineering team created this easy-to-use guideline for 3D printing and additive manufacturing technologies. Get answers for commonly asked questions specific to designing for SLS, PolyJet, FDM, SLA, and MJF. Information includes wall thickness, hole diameter, clearance for assemblies, escape holes, minimum detail, pin diameter, accuracy and standard layer thickness.
Break-Even Point // As additive technologies, materials and processes mature, so does the argument for using additive manufacturing (AM) to make production parts. Let go of traditional manufacturing constraints and embrace a new mindset that explores additive manufacturing as a serious means of production. The break-even point of AM compared to injection molding (IM) was once a few hundred parts but is now pushing into the thousands with trends showing the cut-off point even higher in the coming years. Learn more about Additive Manufacturing vs. Injection Molding today.
For more information about Fathom’s Engineering & Design team who can be contracted to support your in-house design teams product development, click thru to read about their expertise and view available services.
Learn more about Fathom’s engineering & design help—start a conversation today!