Incodema by Fathom //
Quick-Turn Sheet Metal Prototyping
- Innovative Forming Solutions for Small Parts
- Comprehensive Cutting, Forming & Finishing Services
- Highly Responsive Team of Experts
Get a Quote
Start a Quote or Connect with Our Experts
Need Complex Sheet Metal Parts Fast?
5-7 Day Turnaround on Small Metal Parts Manufacturing
Rapid Prototyping is Our Specialty
Incodema by Fathom is a rapid prototyping precision sheet metal fabricating company specializing in small, complex, precise parts. We can support your project from prototyping, production and post-processing under one roof. Because we are a vertically integrated company, you get a single point of accountability throughout the lifespan of your project.
25 years ago, we were one of the pioneers to offer rapid prototyping sheet metal services – parts in only 5-7 business days, not 6-8 weeks. Today, our can-do, customer-focused team continues to help our customers value-engineer their parts and deliver cost-effective solutions to their most challenging small metal parts manufacturing needs. They love the sense of urgency we bring to their projects!
Precision Sheet Metal Services & Capabilities
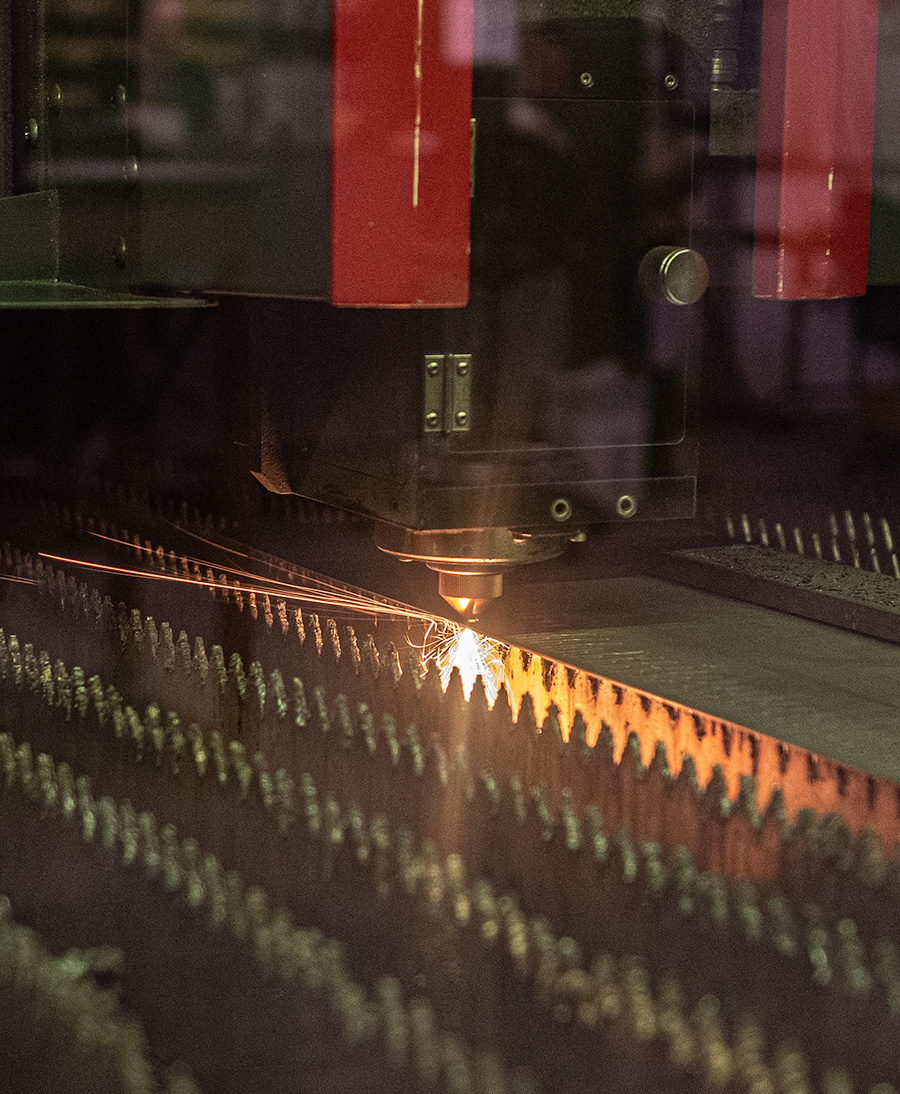
Sheet Metal Cutting
Laser Cutting // Laser cutting is highly accurate and yields excellent cut quality with minimal heat-affected zones. This process is ideal for fast, high-quality sheet metal prototype fabrication projects as well as low-volume production quantities.
Water Jet Cutting // This is a computer numerical control (CNC) machine tool process capable of cutting titanium, Inconel, brass, tool steel, glass, stone, ceramics and composites with superior edge quality and minimal burr. It is ideal for heavy gauge and tough applications and can cut materials with a thickness of up to 6 inches in both low and high quantities.
MicroCut™ // This is a revolutionary, abrasive waterjet technology that provides higher cutting accuracies and tighter tolerances than standard cutting processes. In many cases it can rival the tolerancing achieved with wire EDM. This versatile machine can be used on a wide variety of materials (ferrous and non-ferrous) without leaving heat-affected zones.
Photo Chemical Machining/Etching // This is a process of selectively removing material by using a chemical action, and it is the ideal manufacturing solution for parts with complex geometries such as encoders, screens and filters. PCM is highly precise and produces burr-free parts quickly and at a low cost. With PCM, the hardness, grain structure and ductility of the metal remain unchanged by the process.
Sheet Metal Forming
Manual Progressive Dies // We have developed a technique in which we turn an ordinary press brake into a manual progressive die by adding multiple die sets to a single brake. By combining this dynamic technique with our custom modular tooling, we can easily set up several projects per brake per day while achieving precision tolerancing on the most intricate, small components. This process is so precise that we refer to it as “sheet metal origami” on the shop floor.
Manual Forming: Large Format // While small, complex parts are our specialty, we also offer large format services in-house. We maintain a 300-ton press with a 36″ x 72″ bed in our facility to form parts that are too large for a traditional press brake. This equipment is ideal for small-volume projects that require deep-drawn custom parts or large die sets with embosses and gussets.
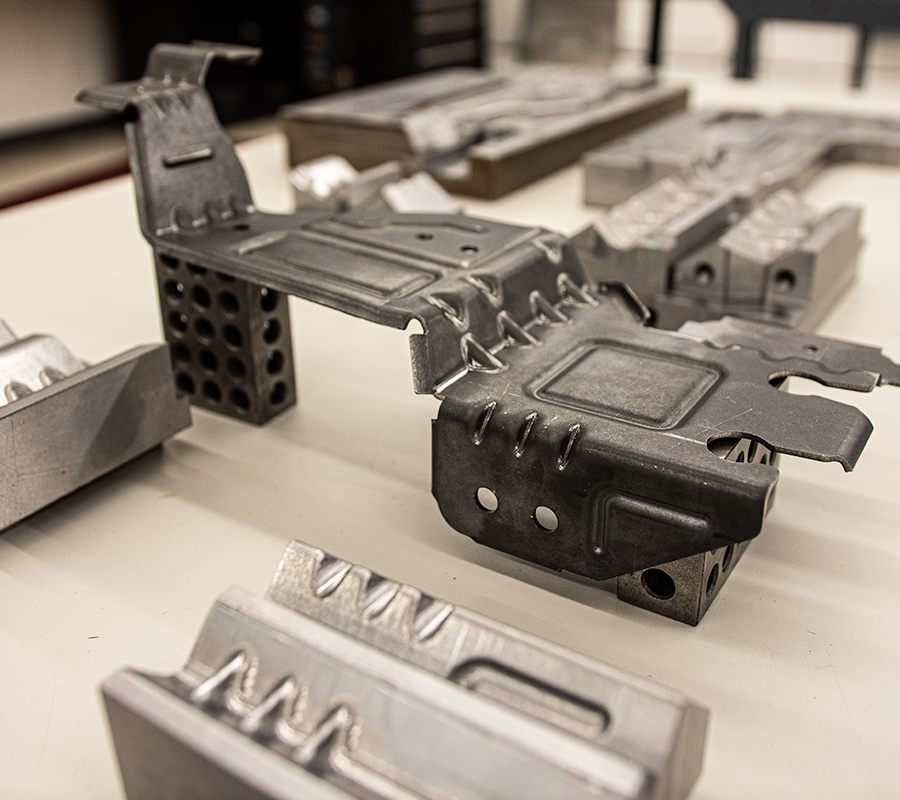
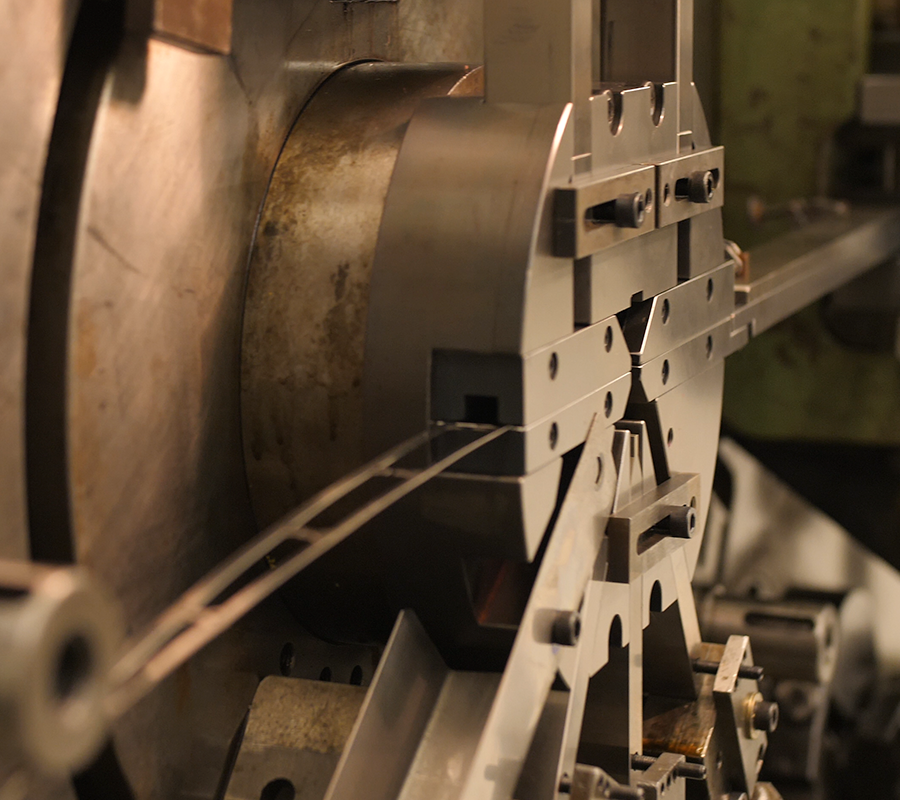
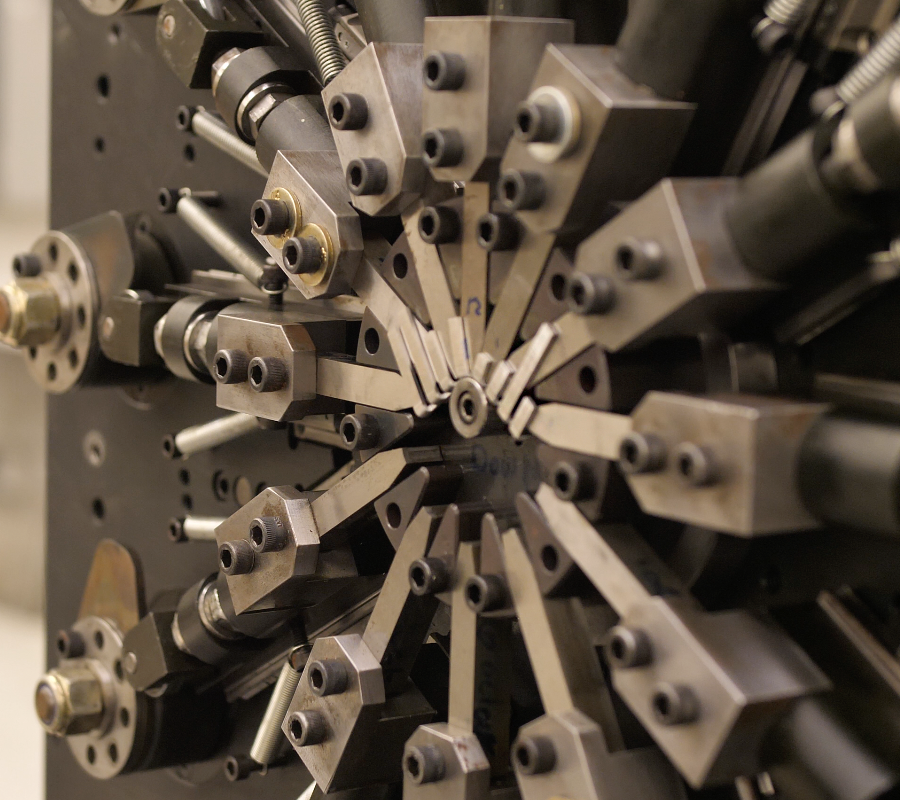
Mid-to-High Volume Sheet Metal
Semi-Automated Manufacturing // We offer a variety of cost-effective, semi-automated tooling solutions that cost 15-30% of the cost of fully automated production tooling.
- Photo Chemical Machined Flat Blanks // Small, thin parts with complex flat geometry are manufactured burr-free and ready for forming by our partners at Newcut by Fathom.
- Put-and-Take Tooling // Semi-complex dies, actuated manually or by machine, form complex features and/or multiple bending operations in one step.
- Die Blanking // Flat parts and some parts with formed features may be manufactured completely in full automation or made ready for secondary, semi-automated bending and forming processes.
Four-Slide and Multi-Slide Stamping // Four-slide and multi-slide manufacturing are ideal for small and intricate springs, brackets, electrical terminals, clips and battery contacts in high volumes. These machines use custom tooling to quickly make multiple precise bends in a flat blank in seconds.
- Imagine a machine that looks like the face of a clock. The circular perimeter contains a set of forming slides. They contain custom tools for bending, cutting and punching small pieces of sheet metal with incredible precision. Continuous slit-to-width material is fed into this multi-slide machine. Moments later, multiple tools move toward the center, perform their tasks in quick succession and return to their original positions. The machine ejects the finished part. In full automation mode, a multi-slide machine can produce thousands of parts a day without human intervention.
Specialty Stamping // Our skilled and creative toolmakers can design and create complex tooling solutions necessary to manufacture even the most challenging stamped parts. Many of Incodema by Fathom’s operators have engineering skills, and they are empowered to develop manufacturing solutions on the fly to keep the manufacturing process moving quickly and smoothly.
Post Processing
Welding // Our in-house welding experts can complete your part by fusing two or more parts through heat, pressure or both.
- Arc welding
- Metal inert gas (MIG)
- Tungsten inert gas (TIG)
- Laser welding
- Resistance spot welding
- Oxyfuel welding and cutting
Outside Processing // We maintain strategic partnerships with key suppliers of heat treating, plating and powder coating who understand our need for quality and speed. All our processes are NADCAP certified and RoHS compliant.
Post-Machining // While we make every effort to meet all your design specifications during the fabrication process, occasionally post-CNC machining is required to complete your parts. Our in-house CNC machining centers allow us to post-mill features into your sheet metal components to meet your requirements while maintaining our fast turnaround times.
In-House Custom Tooling // Whether your formed parts need intricate EDM tooling, waterjet cutting or more robust CNC-machined tooling, our team of engineers and master tool makers can develop creative tooling solutions for your formed parts. Complex bending and precision forming are our specialties. We look forward to solving your most challenging design features.
Deburring and Finishing // Attention to detail is critical to our manufacturing process. We can uniformly remove laser dross, mechanical burrs or sharps and other surface imperfections with our in-house deburring and finishing operations. Our processes range from hand sanding to automated deburring, tumbling and finishing.
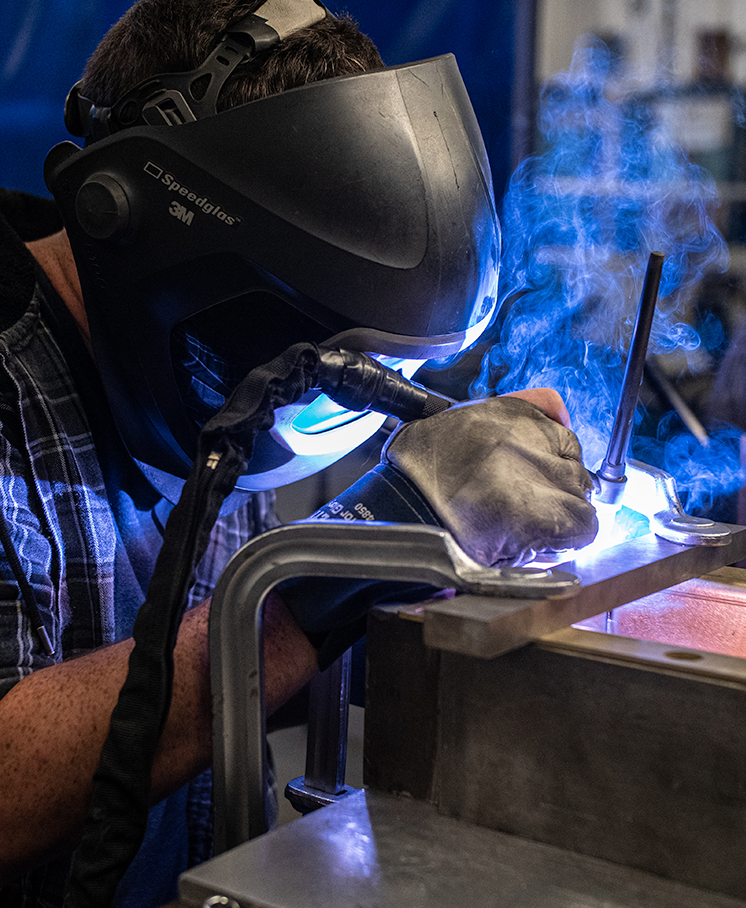
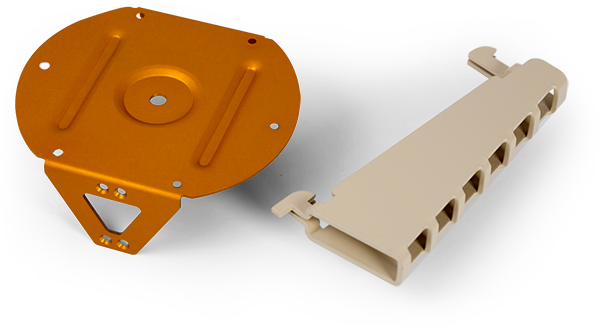
For Every Step In Your
Product Lifecycle
Your parts matter to us. From the moment you begin talking to the Incodema by Fathom team, you’ll know something is different. There’s a sense of urgency and a refreshing can-do attitude. You’ll get a quote within 24 hours. You’ll be talking to the people doing the work, not a middleman or an algorithm. We take a white glove approach to small metal parts manufacturing.
Other sheet metal fabrication shops prefer to focus on big production jobs. They won’t touch sheet metal prototype fabrication projects because there’s no guarantee they’ll evolve into production projects. But these types of projects are our bread and butter. We love to build relationships that grow over time, from part designs to successful production projects.
Our unique in-house blend of metal-cutting and forming technologies, combined with our deeply experienced team, enables us to help you quickly optimize your parts for manufacturability and bring your new products to market faster.
Small, complex formed metal parts are our specialty
Talk to our experts today to kick off your next sheet metal prototype fabrication project!

Designing for Sheet Metal Parts
Engineers need to consider several rules of thumb when designing parts for sheet metal. This helpful guide summarizes the best practices you need to keep in mind.
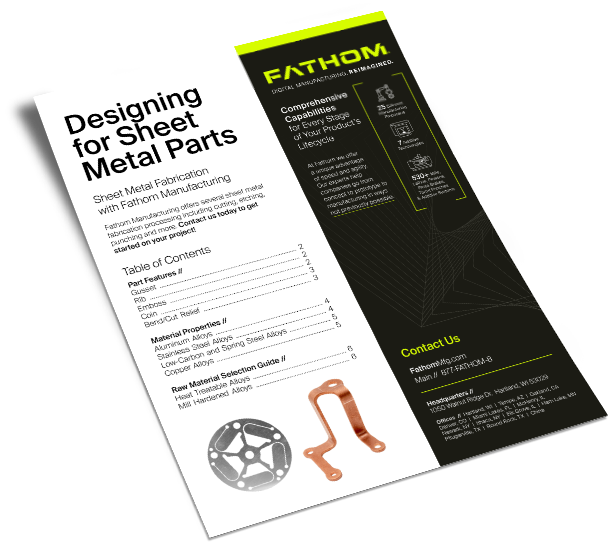
Prototype to Production //
Why Our Customers Choose Incodema by Fathom
We have the expertise, equipment and capacity to meet your needs for small, formed precision sheet metal parts – from prototyping to production of up to 50,000 pieces.
Large progressive die and multi-slide shops are focused on big production runs – typically millions of parts per year. They can’t afford to help customers iterate a prototype part until it’s qualified for production. At Incodema by Fathom, it’s our core expertise. We welcome these types of projects. We can help you accelerate your new product development process.
We Love Prototyping // When you need sheet metal prototyping services, we’re the experts. When you bring your part design to us, our engineering team will review and offer recommendations to improve its manufacturability. Next, we typically produce several rounds of prototype parts for your review to validate their fit, form and function. Formed prototypes are manufactured by hand using precision press brakes and custom tooling (if required).
Solution Focused // We love helping our customers solve their design problems. We value-engineer their components, helping them save money through better design. Our highly experienced team has been doing it for decades. They’ve seen and solved a wide variety of small metal part manufacturing challenges. They look forward to an opportunity to bring their expertise to your complex cutting and forming projects.
Vertical Integration // Engineering, tool building and production are all done under one roof by our experienced team. The knowledge of your project stays with us throughout the life cycle of your parts. That means fewer hassles, faster problem solving and better parts.
Certification & Compliance // We’re ISO 9001:2015 and ITAR Registered.
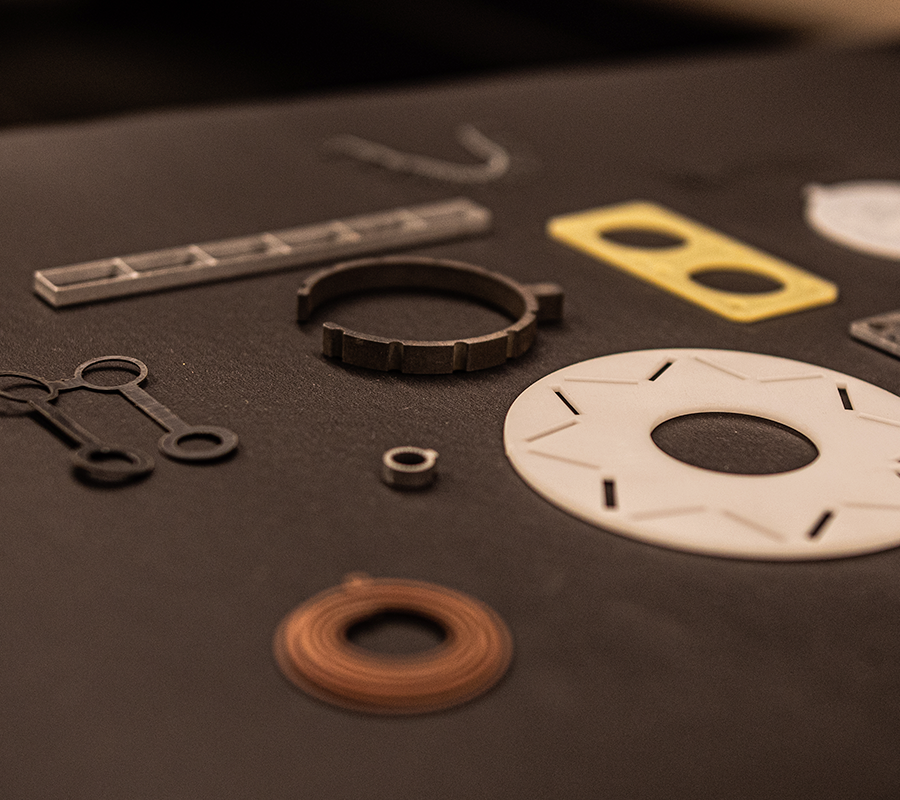
Precision Sheet Metal Applications
A wide variety of industries use precision sheet metal manufacturing to produce their prototypes and final products. It can be used for:
- Medical products
- Office equipment
- Communications products
- Housing
- Chassis
- Enclosures
- Brackets
- Appliances
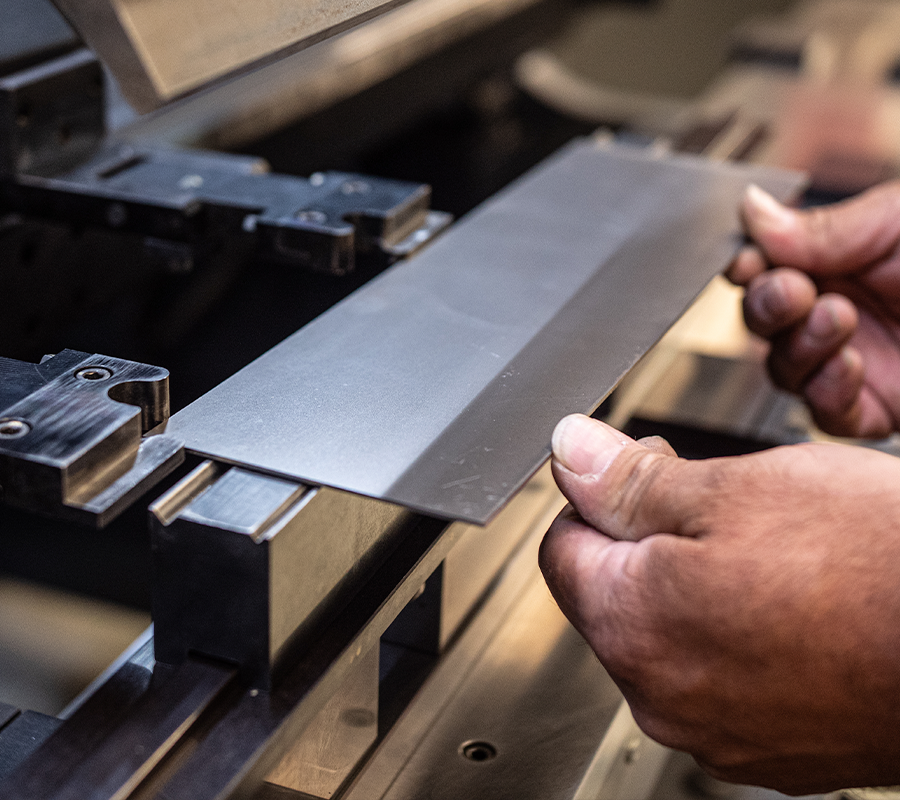
Industries Served
Our precision sheet metal engineering, manufacturing and finishing operations have made us a preferred supplier to manufacturers in these industries:
- Electronics
- Defense
- Aerospace
- Life sciences
- Industrial
Service Area
Incodema is located in Ithaca, New York but services all the following local areas and more:
New York // Buffalo | Rochester | Utica | Mount Vernon | Syracuse | Binghamton | Elmira | Niagara Falls | Albany | Schenectady | Cornwall | Poughkeepsie | Yonkers
Pennsylvania // Erie | Scranton | Wilkes-Barre | Philadelphia
New Jersey // Newark | Jersey City | Camden
Why Choose Incodema by Fathom?
At Incodema by Fathom, we can help you solve your biggest precision sheet metal design challenges. Our team of engineers and master tool makers can develop creative tooling solutions to form your parts.
Why should you invest in sheet metal prototype fabrication? It enables you to test it for form, fit and functionality. It can also help eliminate the guesswork in manufacturing and reduce your overall costs.
Our unique in-house blend of metal-cutting and forming technologies, combined with experienced engineering and production teams and can-do culture, enable us to help you quickly finalize your part designs and bring your new products to market faster.