Top 5 Reasons to Leverage Urethane Casting
Leveraging Urethane Casting for Shorter Product Development Timelines
How do you get a finished product out without investing in injection molding tools for your plastic components?
Designs are hard to finish without comprehensive testing. One of the best tools in the tool chest for getting a product from prototype to a finished product is by creating beta builds using urethane casting. Urethane casting (also called RTV molding, silicone tooling, cast urethane) is a low cost, short-run tooling alternative that gives the ability to test a finished product before investing in production tooling.
Top 5 Reasons To Use Urethane Casting
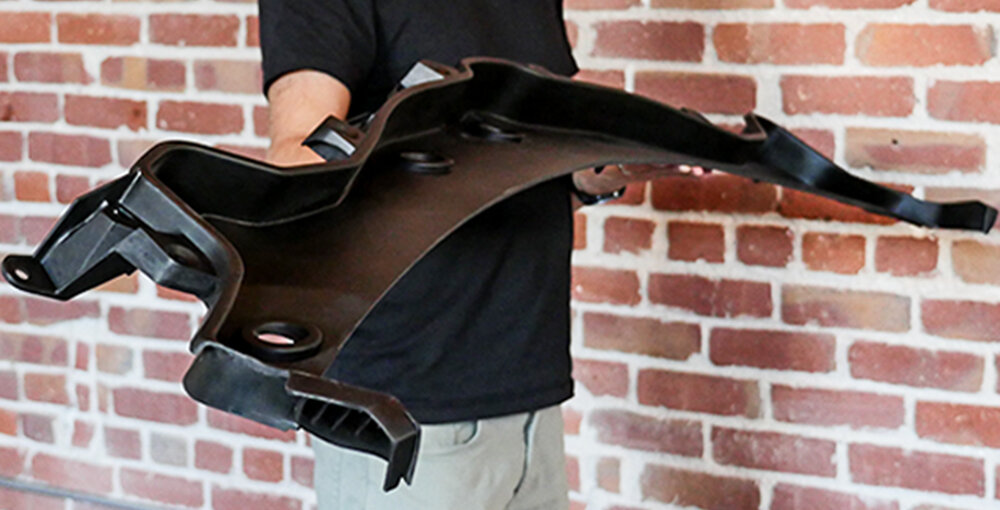
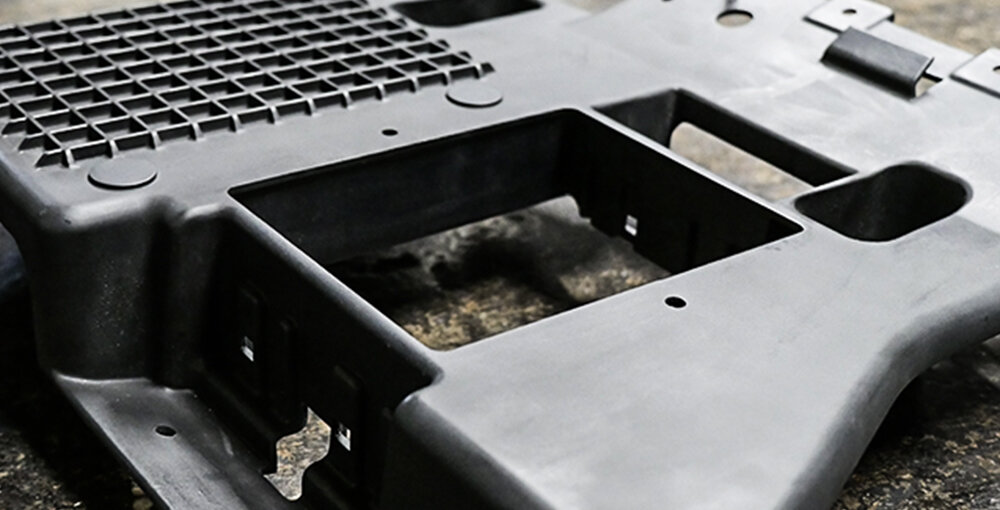
-
Speed / / Urethane casting is a fast and flexible tooling method. Fathom can produce production urethane casting parts in as little as one week. The injection molding equivalent could have taken up to six weeks. Urethane casting uses silicone rubber to make them, resulting in a faster turnaround. Since the material is silicone and not steel or aluminum, making the tool takes only a few days. The flexibility of the tool can break the rules of injection molding, especially concerning undercuts. The tooling method for urethane casting cuts down on time spent in design for manufacturing (DFM).
-
Cost / / Creating a silicone tool for urethane casting is much less expensive than cutting a metal tool. Fathom recently was able to reduce total cost of production by 68% for a low volume production request (20 parts). This fits in a typical range of cost reduction when compared to cutting a metal tool using CNC Machining. It does have a limited run life, but for creating batches of anywhere from 10 to 1,000, it can be an ideal production method. Because the process is more manual than injection molding, the price is higher, so as volumes increase, injection molding becomes more cost effective. Complexity and size are key drivers in part cost.
-
Cosmetics / / Urethane casting can meet high cosmetic standards. In a recent automotive project, Fathom was able to create production ready parts for an internal show where an interior was assembled without having to create injection molds for the large paneling. These parts included medium texturing to approximate the final cosmetics. Additive manufacturing can be expensive to create a cosmetic finish on multiple copies of the same part. But urethane can be a cheaper and faster method for creating cosmetic finishes on parts that are not ready to be sent to production tooling.
-
Functional parts / / Available urethanes offer a dynamic range of material properties. For a project that had ruled out 3D printing because no material could meet the HDT and elongation needed to function, Fathom was able to exceed both requirements using a high heat urethane. There are materials that meet the needs of nearly every application. Whether the need is for high heat deflection, chemical resistance, V0 flammability or complex overmolds, urethane casting can accommodate.
-
Clarity / / Making beautiful clear parts with a 3D printer is a challenge. Typically, this is done using a Stereolithography (SLA) machine with a lot of post-processing and can only achieve so much clarity because of the layering process of all 3D printing. In a replacement for parts that were typically machined from acrylic in multiple parts with complex and expensive setups, Fathom was able to cast urethane parts with similar clarity for a fraction of the price.
Urethane Casting Parts In As Soon As 7 Days // Get A Quote
The Urethane casting process relies on the use of silicone rubber to make the tools that are then injected with thermoset urethanes to create end-use parts. Urethane casting materials options are wide-ranging in mechanical properties, colors and transparencies and can be suitable replacements for many common production engineering plastics.
In an industry like automotive where there are layers of testing requiring builds and subsequent changes, the flexibility afforded from urethane casting can mean saving hundreds of thousands of dollars by avoiding expensive tool changes or even tool scrapping. With millions of dollars of tooling on the line, urethane casting is used in nearly every beta build in automotive.
-
Larger plastic parts such as interior paneling or ducting are ideal because of the very large and expensive production tools needed.
-
Fathom’s urethane casting capabilities are some of the best in the industry, using a wide range of proven resins with the ability to create some of the largest parts needed.
-
With equipment able to handle parts in excess of 1,000 mm, Fathom can support any beta build requirements for urethane cast parts.
Color matching, material certification, and finishing techniques like texturing, polishing, plating are all options that can be used to make anything from basic functional parts to fully cosmetic production-ready parts.
Urethane casting is an essential tool for creating production ready parts at lower volumes while minimizing large tooling investments. Whether it is a low volume manufacturing run for a beta build, initial samples for a marketing activity or even a bridge to production while steel tools are being cut, urethane casting is an extremely valuable manufacturing process for quantities typically anywhere from 10 to 1,000 parts.
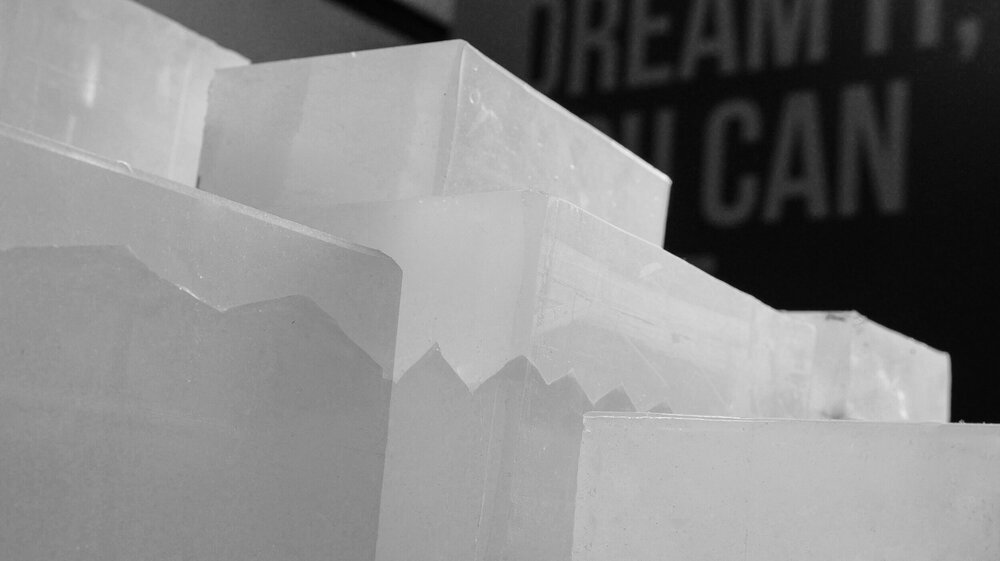
Ready to Request a Quote // Upload Your Files Today