Fathom’s design team is always searching for and thinking up ways to optimize additive manufacturing methods and solve real world problems. In this featured post, learn more about how Industrial Designer Aaron Porterfield set out to demonstrate the strengths of generative design in creating fixtures of any angle. This method allows designers and architects to utilize more structural complexity and customization rather than what is possible using traditionally manufactured fixtures with standardized angles. To manifest the diverse angles and complex geometry of 3D printed fixtures in a physical form, Porterfield created a space-frame coffee table for the Fathom Oakland office.
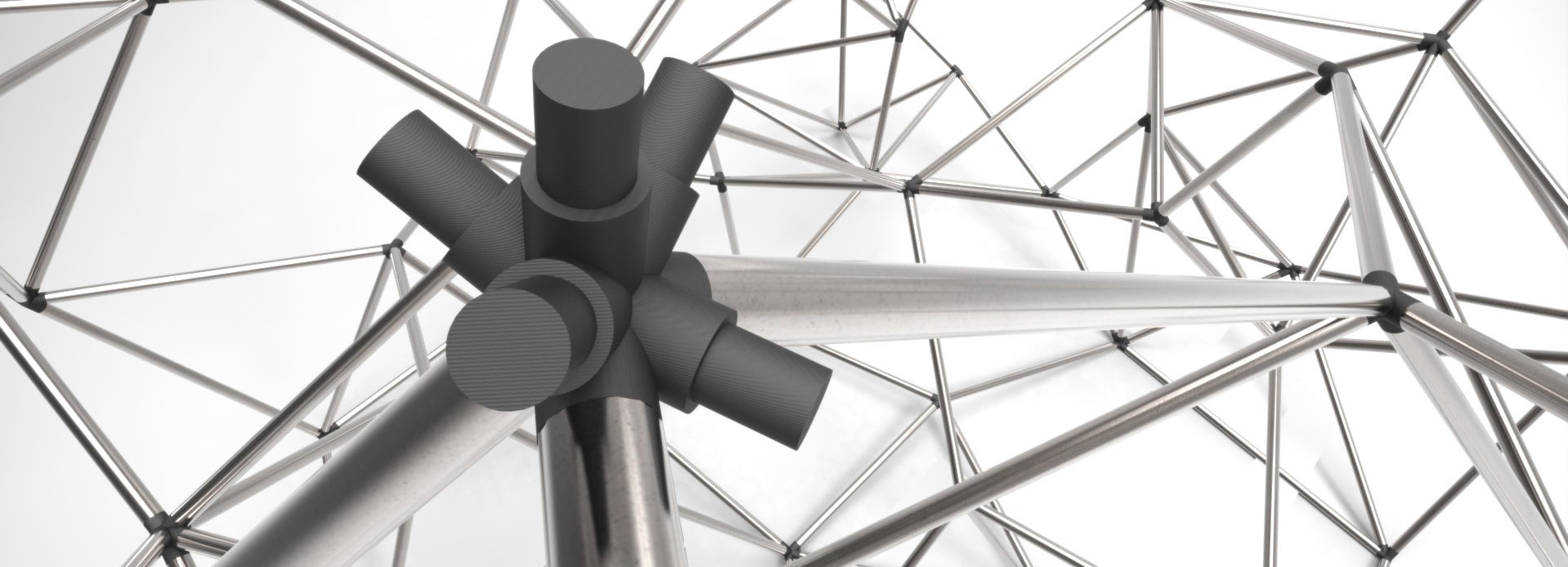
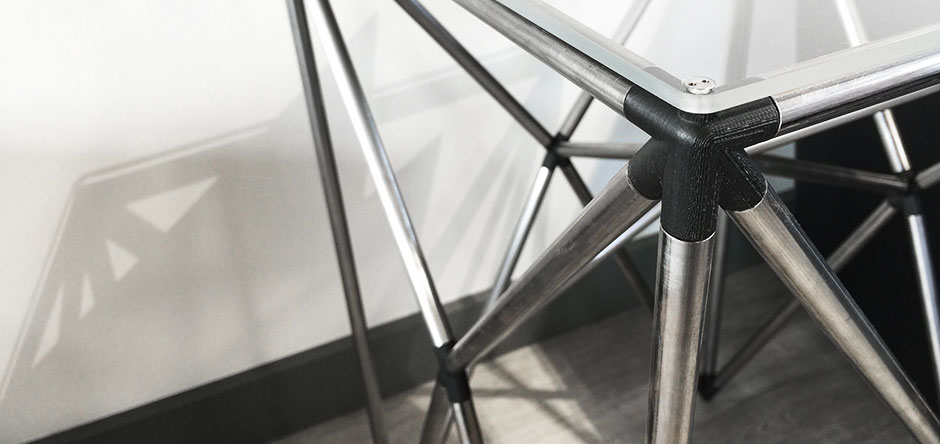
Unlimited Number of Angles Available for Design Through Parametric Modeling and 3D Printed Parts
When building with tube materials, connections are typically made by cutting material to fit in the desired position for welding (such as with bicycle frames or furniture) or a standardized fitting is used. Mass produced fittings are made with a limited number of angles (typically 90, 60, 45 or 30 degrees), between a limited number of connections. This constraint to standardized angles and uniform tube lengths hinders design variety and creativity. More complex designs, such as those used in architectural projects, require many unique pieces and therefore unique connections.
Fathom’s Industrial Designer Aaron Porterfield created a parametric model using Rhino3D and Grasshopper (a plugin for Rhino3D mainly used in architecture to create generative structures) to generate a “node” at the connection points of any group of lines. The nodes were designed to fit into hollow tubing using a user-defined diameter and wall thickness. The length of each branch of the node is a function of the angle between itself and neighboring branches, ensuring that the struts do not overlap.
The Grasshopper script produces a list with numbered tags for each 3D printed node and each strut. This list can be sorted by length to make sourcing material and planning cuts easier.
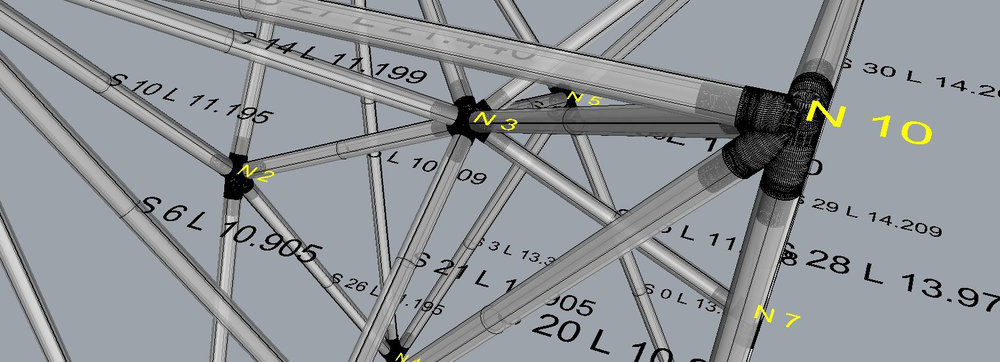
To demonstrate the capabilities of his model, Porterfield designed and built a small coffee table with a “space-frame” structure. This concept was inspired by Matt Hutchisons Asterism Series. The table consists of 13 3D printed nodes and 32 struts. The struts were cut from ½” OD tube steel and the nodes were printed in FDM ABS on Fathom’s uPrint SE Plus FDM 3D printer by Stratasys.
All the nodes for the table fit on a single uPrint SE Plus build tray for an overnight build. The table top was cut from a sheet of acrylic using Fathom’s laser-cutter. Due to the high accuracy of the customized nodes, the assembly didn’t require any glue or fasteners except for four bolts that attach the acrylic table top.
The next step for this concept would be the combination of this process with simulation to create structurally optimized design. A structural analysis could generate the most efficient frame design using a minimal number of struts, then a finite element analysis on each node could be used for topology optimization in order to reduce material.