CNC Turning Services
CNC turning services enable the production of tight tolerance cylindrical or spherical parts from a variety of metal and plastic materials. It’s ideal for rapid prototyping and low- to medium-volume production. Using this traditional manufacturing technique, a workpiece is secured in a lathe on one or both ends. It is then rotated at high speed. A cutting tool removes material until the desired part geometry is achieved.
CNC Turning Services
for Metal & Plastic Parts
CNC turning services encompass multiple machining operations where parts are rotated and cut. Fathom offers CNC turning at several of its facilities.
Learn more about Fathom’s CNC services, which include drilling, turning and milling.
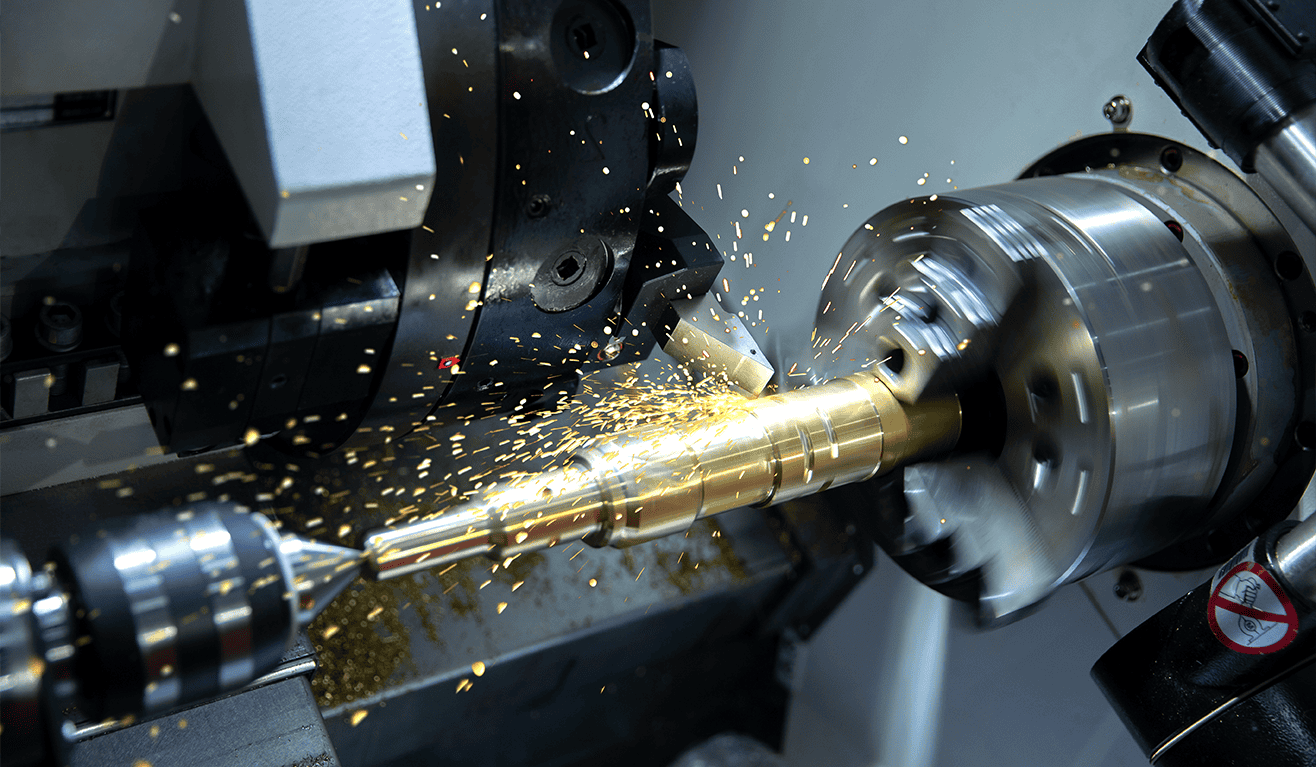
Facing
During facing, material is removed from the end of the workpiece to produce a flat surface. It’s often the first step of the CNC turning process.
Drilling
During this step, a rotating cutting tool or drilling bit makes holes in the workpiece. Drilling is most often done in pieces that will require assembly and is used to accommodate inserts or fasteners.
Turning
During CNC turning, the machine uses a cutting tool to shape the workpiece to precise dimensions, following the data fed into it from its CAD drawing.
Boring
During boring, a cutting tool such as a drill is used to remove internal material from a workpiece to create or enlarge holes.
Threading
A specially designed cutting tool is used to create external and internal threads on the workpiece. This rotating tool is precisely calibrated to produce threads with the desired depth and density.
Swiss Turning
With Swiss turning, bar stock is fed through a guide bushing. It firmly supports the material as it feeds into the tooling area of the machine. The material is held tightly in place to maximize stability and precision. The workpiece can be moved along its Z-axis, enabling more complex shapes to be cut. Swiss turning is especially valuable for the production of small, high-precision metal parts.
Benefits of CNC Turning Services
Fast & Efficient Production // These machines can run 24 hours a day, seven days a week without human supervision, while maintaining a high degree of accuracy.
Quick Production Changes // Changing over from the production of one part to another only requires the loading of a new CNC program. Many CNC machines are equipped with a rotating carousel that can carry multiple tools. This enables it to automatically switch tools during milling and machining processes.
Cost-Effective Production of Prototype Parts // Because CNC turning machines can process parts quickly, they can be used to cost-effectively produce small numbers of metal and plastic prototype parts.
Reduced Production Costs // Compared to manual turning, CNC turning provides efficient, scalable production while minimizing material waste. These factors result in the cost-effective production of parts.
Learn more about Fathom’s CNC services and expertise.
Benefits of Swiss Turning
Complex Parts // Swiss turning can be used to produce small, intricate parts quickly, with tight tolerances. Because of their guide bushing system, Swiss lathes can process long, slender parts and cut intricate details more effectively than conventional CNC lathes.
Extremely Tight Tolerances // Swiss CNC machines firmly support the workpiece adjacent to the point of operation throughout the machining process. Because the piece is supported so close to the tooling operation, the part remains steady, virtually unaffected by the force of the tools. This ensures precision within extremely tight tolerances—even when machining very small parts.
Improved Surface Finishes // Swiss lathes usually operate at higher RPMs with no vibration. This enables faster machining times and improved surface finishes.
Eliminate Secondary Operations // Swiss turning lathes can mill, drill, ream, saw and do many other operations, eliminating the need to do them separately as secondary operations.
Industries Benefiting from CNC Turning Services
- Automotive
- Aerospace
- Electrical
- Medical
- Energy
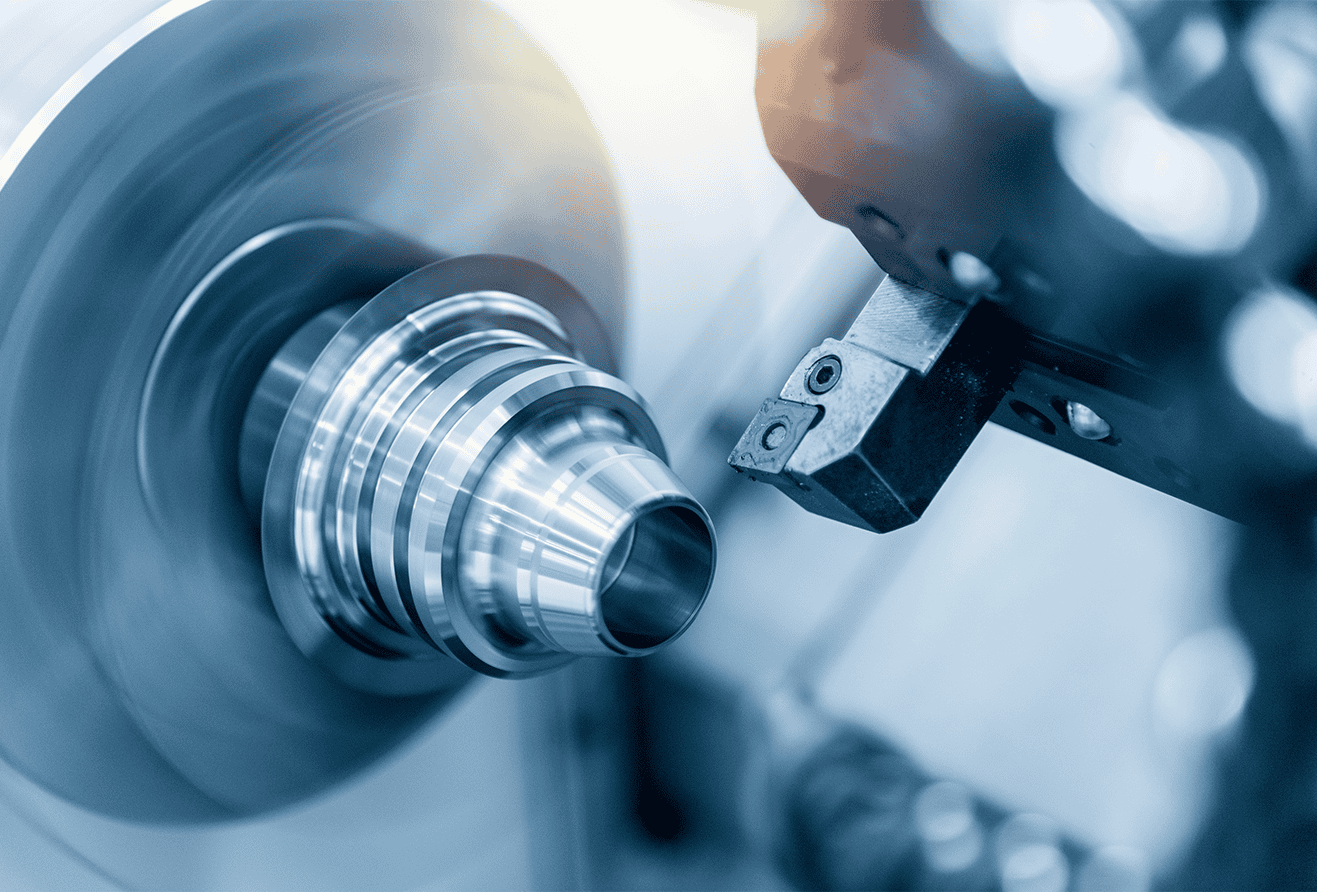
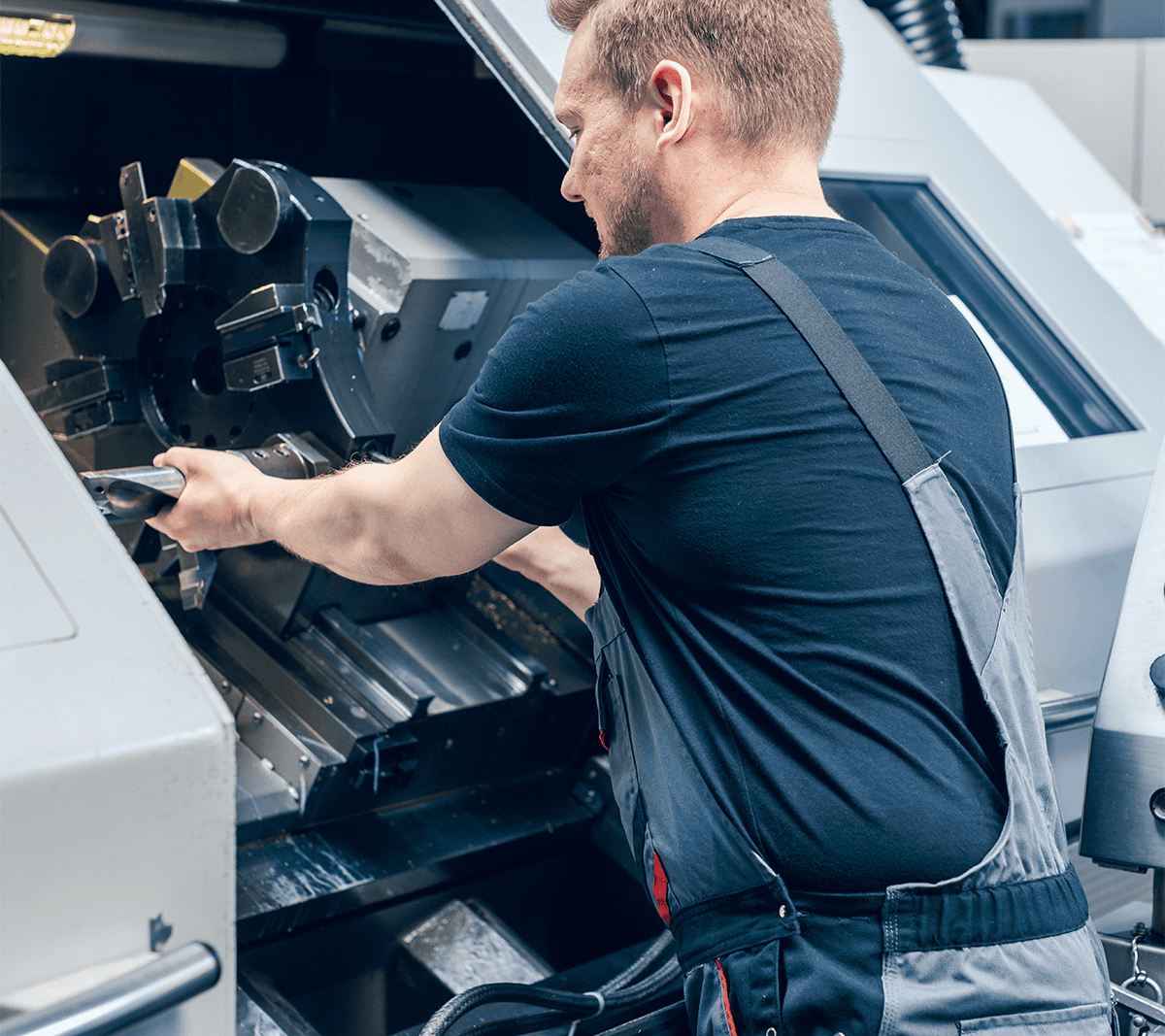
Fathom’s Locations for CNC Services
Fathom’s nationwide network has four locations across the U.S. that offer CNC turning services:
Wisconsin //
Fathom Headquarters
1050 Walnut Ridge Drive
Hartland, WI 53029
Arizona //
444 W. 21st St. Ste. 101
Tempe, AZ 85282
Minnesota //
13758 Johnson Street NE
Ham Lake, MN 55304
Texas //
1513 Sam Bass Rd.
Round Rock, TX 78660
CNC Turning Material Specifications & Tolerances
METALS |
OPTIMAL QUANTITY |
TOLERANCES (+/-) |
ADVANTAGES & CONSIDERATIONS |
FINISH & |
Stainless Steel |
1-1,000 |
+/- 0.005″ |
|
|
Low Carbon Steel |
1-1,000 |
+/- 0.005″ |
|
|
Aluminum |
1-1,000 |
+/- 0.005″ |
|
|
Brass |
1-1,000 |
+/- 0.005″ |
|
|
PLASTICS |
OPTIMAL QUANTITY |
TOLERANCES (+/-) |
ADVANTAGES & CONSIDERATIONS |
FINISH & |
HDPE |
1-100 |
+/- 0.008″ |
|
|
PC |
1-100 |
+/- 0.008″ |
|
|
ABS |
1-100 |
+/- 0.008″ |
|
|
Acrylic |
1-100 |
+/- 0.008″ |
|
|
Nylon 6/6 |
1-100 |
+/- 0.008″ |
|
|
Acetal (Delrin®) |
1-100 |
+/- 0.008″ |
|
|
ULTEM® |
1-100 |
+/- 0.008″ |
|
CNC Turning Available Machinery
BRAND |
MODEL |
BUILD VOLUME (in) |
PAR System |
5-Axis |
284 x 112 x 53 |
Haas |
UMC750 SS 5-Axis |
19.7 x 15.7 x 7.9 |
Haas |
VF-9/40 |
84 x 40 x 30 |
Mighty Viper |
Pro 3150-AG |
120 x 61.4 x 32 |
Mighty Viper |
B100 |
50 x 100 x 24 |
Mighty Viper |
Pro 1000-AG |
43 x 24 x 25 |
Mighty Viper |
LG 1000 |
40 x 20 x 25 |
Mazak VC |
Universal 500A 5-Axis |
20 x 20 x 20 |
Mazak |
VTC-30C |
65 x 30 x 26 |
Mazak |
VTC-20B |
44 x 20 x 20 |
Mazak |
Quick Turn Universal Smart 350 |
Lathe 4″ bar diameter, 10″ x 25.5″ |
KUKA |
KRC22 6-Axis Robotic Cell |
w/ Turntable |
Mori-Seiki |
NLX 2500SY 2015 & 2017 |
CNC Lathe |
CNC Turning Finishing
Bead Blasting // Bead blasting adds a satin or matte finish to a CNC part. The matte finish is accomplished by using a pressurized air gun to shoot glass beads at a part.
Powder Coating // Following powder coating, the part has a thin protective layer that adds strength and wear-resistance. During the powder coating process, the part is first primed using a chromating or phosphating coat. Next, the part receives a dry powder coating from an electrostatic spray gun. Lastly, the part is cured in an oven.
Anodizing // Once a CNC part has been anodized, it has an oxide layer that increases its density, thickness, and durability. Anodization also makes a part electrically non-conductive. During the anodizing process, the part is placed into an acid electrolyte bath which serves as an anode. A cathode is added to the part, and an electrical current is passed through the acid. Oxygen ions from the electrolyte and atoms from the alloy are combined along the surface of the part.
As-Milled // As-milled or as-machined products do not require a secondary process. They will still have visible blemishes and may have a rough surface.
Surface Grinding // Surface grinding produces a smooth finish. Surface grinding removes material by using a high-speed abrasive wheel as a cutting tool. The surface grinding process is used when a specific size or precision finish is required.
Polishing // Polishing improves the dimensions and accuracy of a part while producing a mirror gloss finish. Polishing tools and abrasive materials are used to achieve a smooth surface.
Passivate // After a CNC machined part has completed the passivation process, its corrosion resistance is improved. Passivation may include spray application, circulation in a chemical solution, gel application, or tank immersion.
Chemfilm // Chemfilm finishing is a chemical conversion coat that adds corrosion resistance to aluminum substrates, acting as a base for organic coatings. The part is dipped, brushed, or sprayed with the chemfilm layer.
Vacuum Metallization // The vacuum metallization process adds a mirror-like or decorative uniform finish while also improving thermal, air, light, or water barrier properties. In the vacuum metallization process, the part is placed inside a closed chamber where a metal vapor adheres and coats the part.
Silkscreen // Screen printing is used to transfer a design or logo to a part. When a part is silk-screened, a mesh is used to apply ink onto the surface, but only to permeable areas that are not covered by a blocking stencil.
Plating // Plating results in corrosion and abrasion resistance, conductivity, and reflectivity to parts. While electroplating, the part is submerged into an electrolyte bath with the material that will be used for the metal coating. An electrical charge causes the material to transfer to the part, resulting in a uniform metal coating.
Tumbled // Tumbling or ultrasonic polishing removes any sharp points or edges from a machined part. During the tumbling process, the part is placed inside a barrel along with media, water, and detergent. The barrel tumbles at different speeds depending on the desired finish.
Painting // Painting a part adds color, varnish, or ink. The painting process may include powder coating, liquid coating, or e-coating. Powder coating uses an electrostatically charged powder which produces a scratch-resistant and uniform coat on the metal part. When a part is liquid coated, wet paint is applied. The e-coating process involves dipping the part into a bath of paint where both the part and paint are electrified, causing the paint to adhere to the part.
Choose Fathom for CNC Turning Services
Fathom has the expertise to help you with your precision turning needs.
Whether you need prototype or production parts, Fathom can help you with all your CNC turning requirements. Our CNC facilities have decades of expertise in precision turning of metal and plastic parts. We also offer extensive finishing capabilities.