Injection Molding Cost
What factors go into the price of injection mold tooling and part production costs? How can you ensure that your parts are as affordable as possible? Here’s what you need to know, from the custom injection molding experts at Fathom.
Common Factors That Affect Injection Molding Cost
Injection molding is highly repeatable and allows for identical parts to be produced quickly and in large volumes, but there are many factors that can affect the final cost of the project.
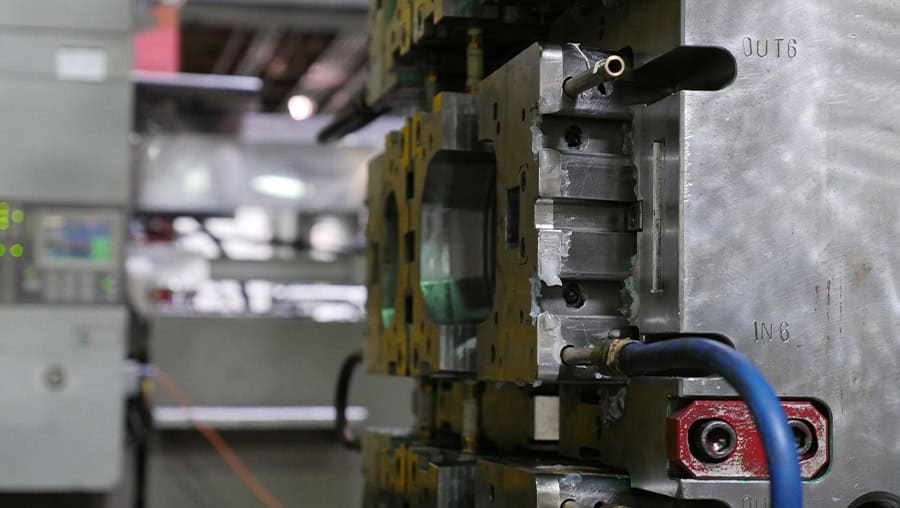
Mold Costs
The more complex the part design, the more costly the tooling. Simple designs with fewer features don’t require as much labor and fabrication time, reducing their cost. Complex part designs that require undercuts, surface finishes or intricate cooling channels, for example, contribute to higher injection molding costs. Multi-cavity tools and family molds are also more complex and cost more to produce than single-cavity tools.
Mold material can also influence the cost. Molds can be made using hardened steel, aluminum or 3D printing. For production parts, Fathom prefers steel tools because they last longer and don’t require as much maintenance as the other two types of tooling. We also offer aluminum molds, hand molds, MUD molds, and unit molds for prototype and low-volume parts.
Our U.S. tooling is produced using automated CNC machining and EDM cutting, which keeps our tool quality consistently high, shortens our lead times and keeps our tooling cost-competitive.
Setup Costs
The labor required to set up a mold to run on an injection molding press can also contribute to higher costs. This includes configuring and optimizing the locations of runners, plus pre-production runs and quality checks. For large production runs, these injection molding costs can be amortized over a larger number of parts. For short production runs, they will have a bigger impact on the per-part cost.
Material Costs
The cost of materials for custom injection molding largely depends on the polymers chosen and the size of your production run. Common materials used for injection molding include polypropylene, polyethylene and acrylonitrile butadiene styrene (ABS). All three of these materials are popular due to their durability and affordability.
How Part Designs Impact Injection Molding Costs
In addition to tooling, materials and setup, injection molding costs can be affected by a part’s size, design and quantity ordered.
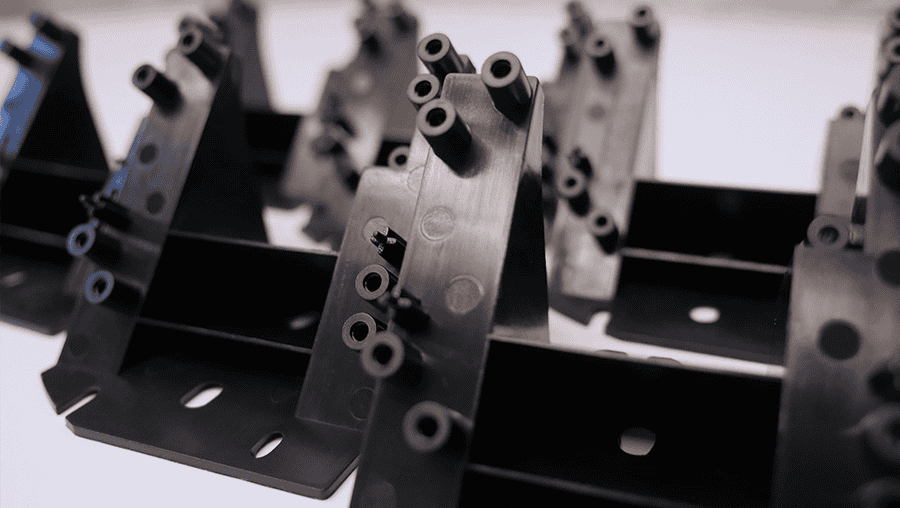
Part Size
As the size and complexity of a part increases, injection molding costs usually increase, too. Complex parts may require more sophisticated gating, runner and cooling systems to ensure consistent fills and to prevent warping during cooling. Larger parts may also require a larger press, which also results in higher injection molding costs. And of course, larger parts require more material, which also has an incremental effect on the overall cost per part.
Part Design
The complexity of a part also impacts its cost. Parts with intricate details are often harder to mold than simple parts. Here are several examples:
- Bosses, which are structures within a part that will contain inserts, must be designed so that they don’t cause sink marks or unsightly seams as the parts cool.
- Parts with thick walls may also cause sink marks or warping due to uneven cooling.
- Parts with surface textures may require additional draft so they can be ejected from the mold without damage.
- Undercuts may require tooling with slide actions so the parts can be ejected from the mold.
Injection molding costs can be reduced by simplifying part geometry and avoiding these potential problem areas. Fathom’s injection molding experts can perform a DFM analysis of your part designs to identify any issues before tooling is made.
Production Volume
Injection molding is a popular manufacturing method for medium- to high-volume production runs. Longer production runs usually have a lower cost per part, because tooling, setup and material costs can be amortized over a larger number of parts.
Injection Molding Specifications & Tolerances
Knowing injection molding specifications and tolerances will ensure that parts fit correctly during assembly. Tolerances also influence how a part should be designed for optimum functionality.
TOOL OPTIONS | LEAD TIME | PART QUANTITY | MAXIMUM PARTING LINE MISMATCH | MAXIMUM FLASH | TOOL TOLERANCES LINEAR DIMENSIONS | PART COLOR | PART FINISH (COLOR) | PART FINISH (TEXTURE) |
---|---|---|---|---|---|---|---|---|
Rapid Tool (Master Unit Die Base) | 1.5-3 Weeks | 5,000 Shots | 0.010in | 0.010in | ±0.003 + 0.002in/in | Pantone Colors | A2 | Yes |
Prototype Tool (Stand Alone) | 2-4 Weeks | 5,000-50,000 Shots | 0.010in | 0.007in | ±0.005 + 0.002in/in | A2 | ||
Production Tool | 5-10 Weeks (Depends on Size and Complexity) | 250,000 - 1,000,000 Shots (Depending on Class of Tool Selected) | 0.005in | 0.005in | SPI (Commercial) | A1 |
Injection Molding Material List
Selecting the right material for your parts is critical because it can affect their performance and cost. When selecting a material, consider the environment in which the part will function and how it will be used. Will it be exposed to harsh chemicals or temperature extremes? Will it experience wear or abrasive conditions? Does it need flexibility to bend or move without breaking?
Fathom’s injection molding experts can help you select the right material that will meet your performance and cost needs.
Some of the materials offered by Fathom for custom injection molding include:
- Crystalline plastics (tough materials with excellent chemical resistance)
- Amorphous plastics (which can be molded into complex shapes with good dimensional stability)
- Imidized plastics (which can withstand high temperatures and loads)
- Polyethylene (PE)
- Polypropylene (PP)
- Acrylonitrile Butadiene Styrene (ABS)
- Polyoxymethylene (POM)
- Polystyrene (PS)
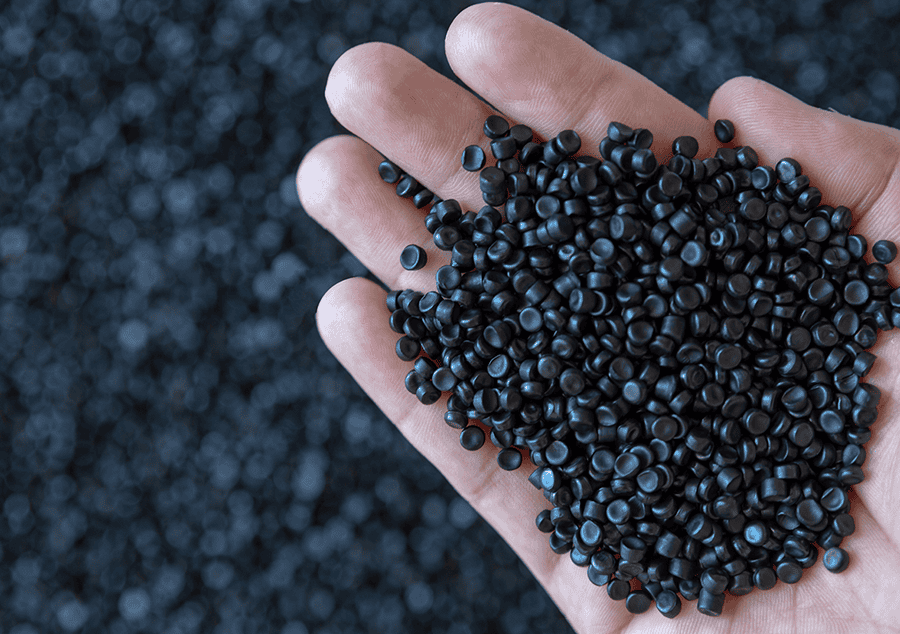
For a list of the material types offered by Fathom’s U.S.-based injection molding operations, download our Fathom McHenry Material Guide:
Injection Molding Finishing Processes
After the injection molding process, some parts may require a surface finish. This step can add a rough or smooth texture to a part. Industrial, mechanical, or construction parts may require a rough finish. Items such as toys or medical supplies may need a smooth or glossy finish. Below is a list of surface finishes offered by Fathom.
SURFACE FINISH | GUIDE | TYPICAL APPLICATIONS |
---|---|---|
Standard No Machine Mark | Tool Marks Removed | Low Cosmetic |
SPI-C1 | 600 Stone | Low Polish Parts |
SPI-B1 | 600 Grit Paper | Medium Polish Parts |
SPI-A2 | Grade #6 Diamond | High Polish Parts |
SPI-A1 | Grade #3 | Lens or Mirror |
IM-1 Light Bead Blast | Need 1 Degree Draft Angle | |
IM-2 Medium Bead Blast | Need 1.5 Degree Draft Angle | |
IM-3 Heavy Bead Blast | Need 3 Degree Draft Angle |
Examples of Injection Molded Parts
- Flat screen enclosures
- Remote controls
- Printers
- Electrical circuit boards
- Cell phones
- Toothbrushes
- Cosmetic packaging
- Helmets
- Jewel boxes
- Padding
- Syringes
- Knobs
- Intake manifolds
- Beakers
- Test tubes
- Medical implants
- Fixtures
- Vents
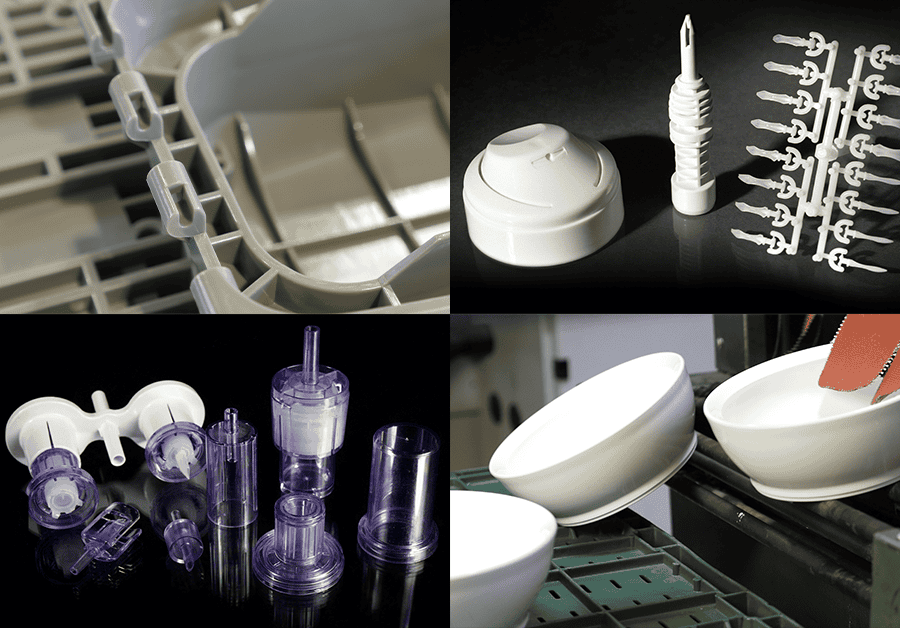
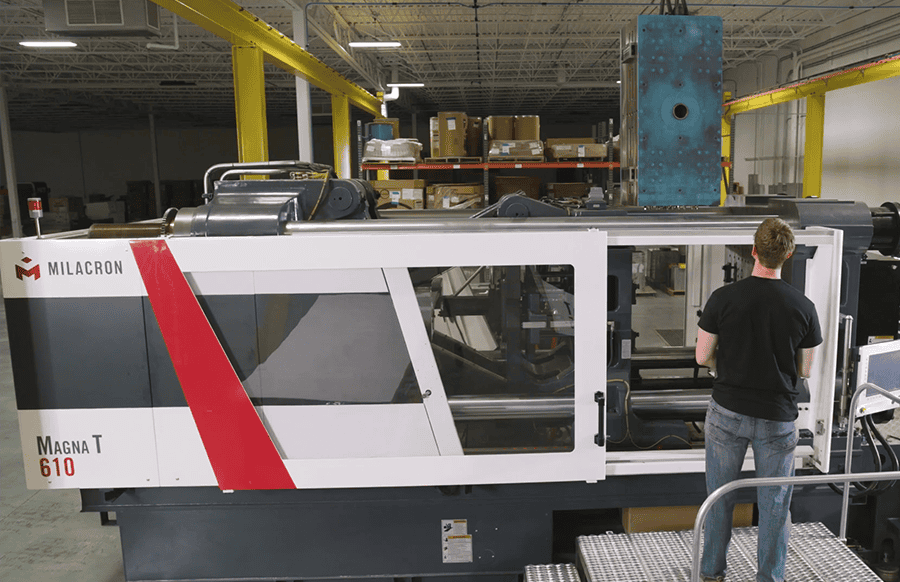
Fathom’s Locations
for Injection Molding
Fathom has 2 U.S.-based locations that offer injection molding. In addition, we offer a lower-cost overseas option via ICOMold by Fathom.
Hartland //
1050 Walnut Ridge Drive
Hartland, WI 53029
Illinois //
1207 Adams Drive
McHenry, IL 60051
Why Choose Fathom’s Custom Injection Molding Services?
Production Parts Faster with Injection Molding by Fathom
Fathom will review your quote and alert you of any potential issues that need to be acknowledged and discussed, and/or problem areas that need to be redesigned – before tooling is made.
Our U.S.-based injection molding team has decades of experience building high-quality tooling. Our automated CNC and EDM machining centers enable us to reduce our lead times, so you can start receiving production parts faster.
Our diverse group of engineers, designers and builders help you navigate the right process, materials and more for each stage of your product development – from design and prototype, to validation for mass production.
Additional Resources