Overmolding
Command Attention
with Overmolding
Are you looking to improve the user experience of your product? Do you need to enhance grip, add vibration dampening or create waterproof seals? Are you seeking ways to reduce assembly costs and improve product reliability? If so, overmolding may be the perfect solution for your project.
What is Overmolding?
Overmolding is a specialized injection molding process that combines multiple materials into a single part. This technique creates components with properties that cannot be achieved using a single material, such as soft-touch grips on rigid handles or waterproof seals integrated directly into housings.
By strategically combining materials, overmolding delivers exceptional functionality while streamlining your manufacturing process.
There are two common types of overmolding injection molding:
Over Plastic // This approach begins with a rigid plastic part. A softer, more flexible plastic material is then molded over it.
Over Metal // In this approach, a metal part is overmolded with plastic. It’s frequently used to add plastic handles to metal tools. It can also be used to encapsulate a metal part within plastic.
Plastic overmolding can also be used to create integrated gaskets, vibration-damping components, multi-color aesthetic features and protective coatings.
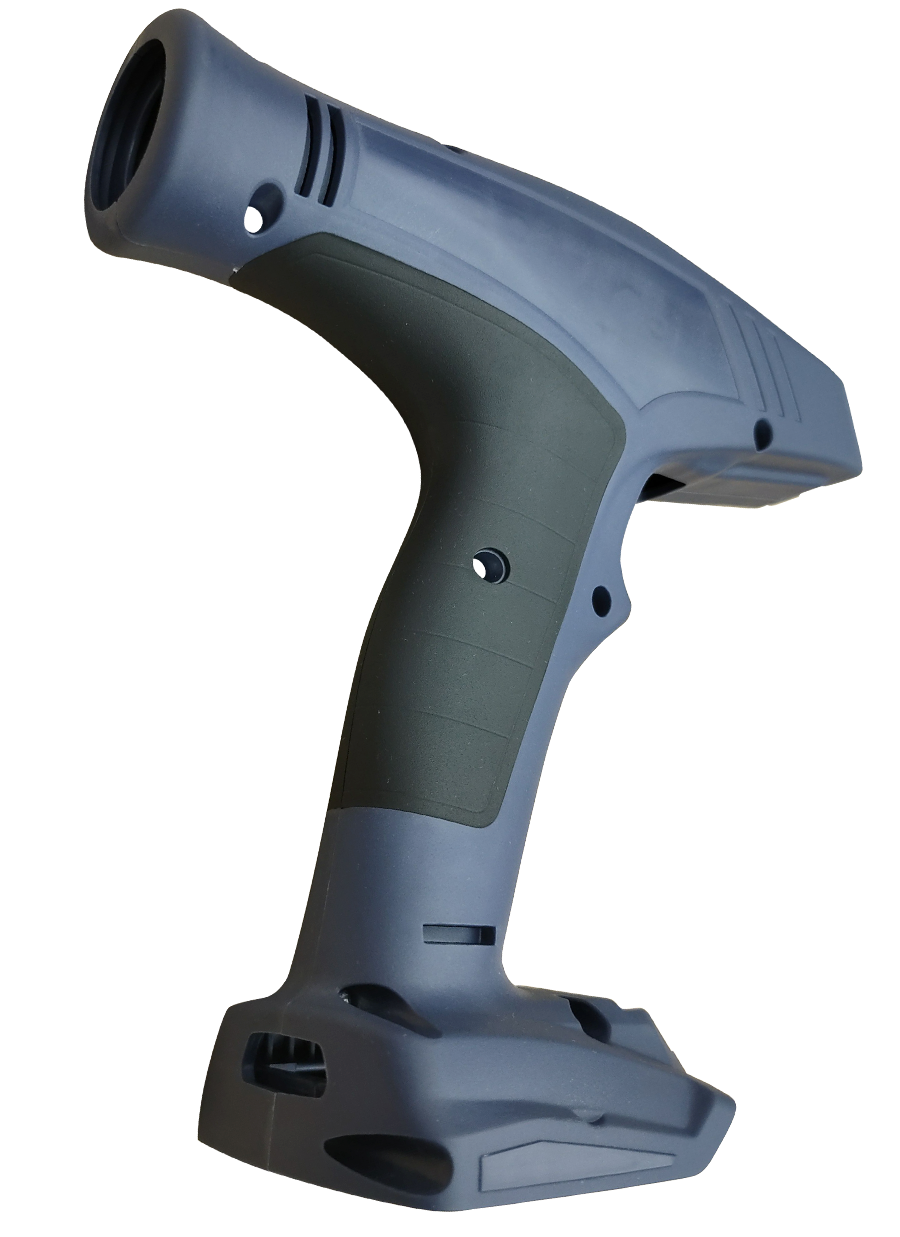
How Can Overmolding Improve Your Products?
Enhance Ergonomics & User Experience // Add soft-touch grips to rigid components to improve user comfort, reduce fatigue and enhance your product’s visual appeal. These tactile improvements can help differentiate your product in the marketplace.
Simplify Assembly // The overmolding process can eliminate secondary operations by combining what would traditionally be separate components into a single overmolded part. Often, it replaces a secondary operation like painting or coating. The efficiency of this injection-molding process reduces assembly time, lowers costs and can also improve the reliability of your product.
Protect Your Parts Against Moisture or Corrosive Liquids // Design and manufacture liquid-tight seals and gaskets into your components, eliminating the need for separate sealing elements. These overmolded features can improve your product’s long-term performance and reliability.
Improve Aesthetics // Incorporate multiple colors, textures and materials into a single part for enhanced visual appeal and brand differentiation. The overmolding process enables you to do so without using time-consuming finishing operations to achieve the same aesthetics.
Enhanced Design Flexibility // Designers can consider and bring to life a variety of eye-catching designs.
Protect Sensitive Components // Encapsulate electronic components or other sensitive elements within protective overmolded layers. This design approach can improve the durability of your product and extend its service life.
Applications of Overmolding
Because of its versatility, the overmolding process is utilized across numerous applications, including:
- Power and hand tools
- Medical instruments and devices
- Consumer electronics
- Automotive interior components
- Sporting equipment
- Household products
- Industrial control systems
Industries where overmolding is commonly used:
- Medical and healthcare
- Automotive and transportation
- Consumer products
- Electronics
- Industrial equipment
- Sporting goods
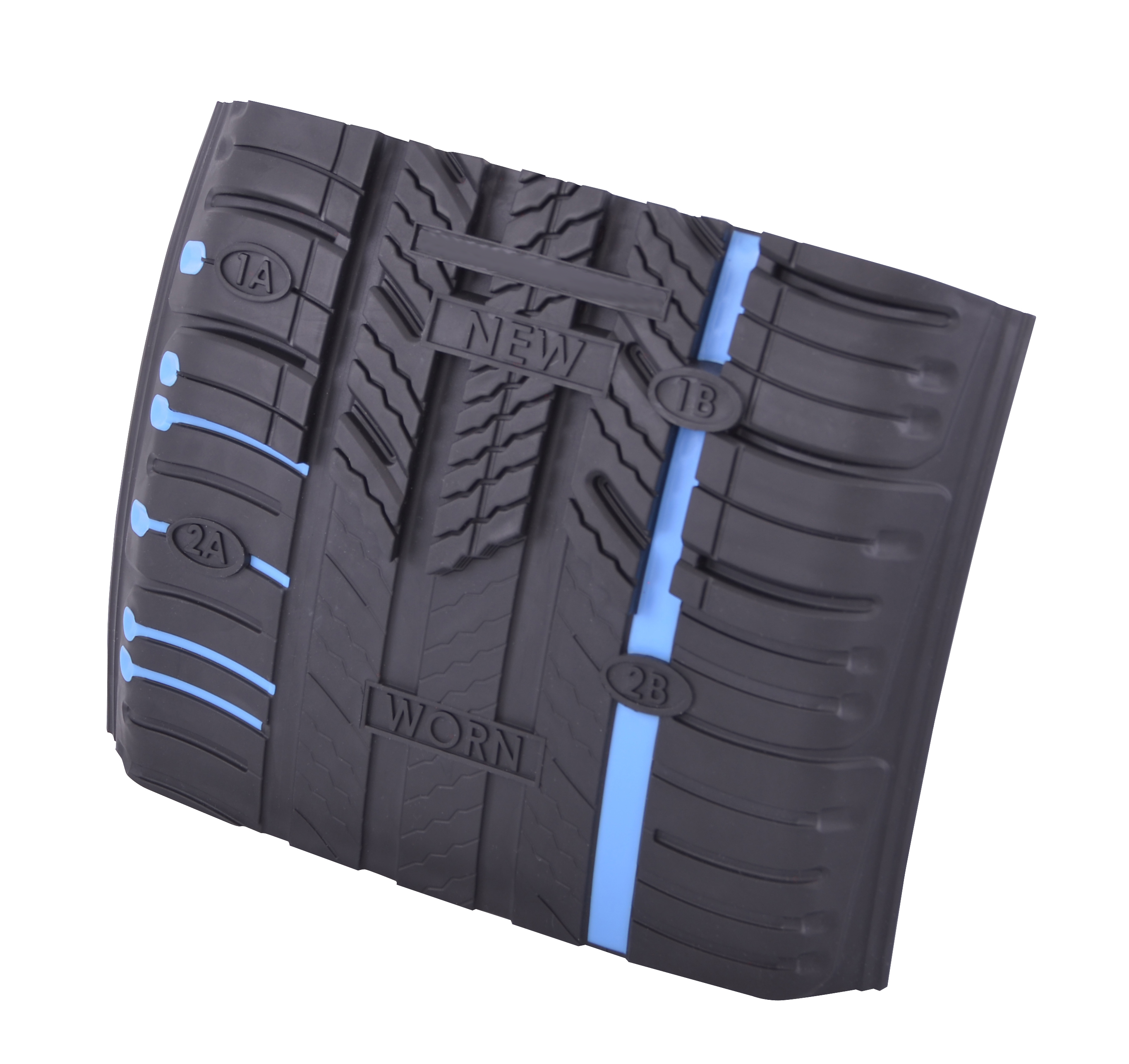
Design Considerations for Overmolding
Material Compatibility // When designing an overmolded part, material compatibility is crucial. The substrate and overmold materials must create a strong chemical or mechanical bond. Without it, the two materials will quickly separate from each other. A Fathom expert can help you select compatible material combinations for optimal results.
Part Design // It successfully requires careful consideration of several design factors:
- Appropriate substrate thickness and structure
- Strategic placement of mechanical interlocks to contain the flow of resin to the places where you want it to go during the overmolding process
- Consistent wall thickness for the overmolded material
- Proper gate location and venting
Overlooking these can lead to adhesion failures, cosmetic defects or other manufacturing challenges. A Fathom engineering expert can help you optimize your design for a successful project.
Two Methods // This manufacturing method can be accomplished using two primary methods:
- Insert Overmolding: The substrate is molded first, then placed into a second mold where the overmold material is applied.
- Two-Shot Overmolding: Both materials are molded in sequence using a single machine with multiple injection units or through mold rotation.
Each approach has specific advantages depending on your production volume, timeline and part complexity. A Fathom expert can help you determine the most cost-effective approach for your application.
Material Selection // Overmolding injection molding offers many material combination possibilities:
- TPE (thermoplastic elastomer) over rigid plastics for soft-touch applications
- Rigid-to-rigid combinations for structural or aesthetic purposes
- Specialized materials for chemical resistance, UV stability or to meet medical-grade requirements
A Fathom expert can guide you through material selection to ensure your overmolded parts meet your performance requirements.
Why Choose Fathom for Overmolding?
Overmolding is a complex process that requires a significant amount of engineering, material and tooling expertise to do well.
Fathom brings decades of experience in overmolding applications through both our U.S. and overseas manufacturing operations. Our engineering team will work closely with you to understand your product requirements and recommend design optimizations, material combinations and manufacturing processes that will deliver the best results while also controlling costs.