Q&A Interview with Scott Cullum
New location, more space and expanded services — oh my! The Seattle-based location has been under construction since late this summer and were getting ready for the grand opening next month. Featured 3D printers at the production center include a Connex500, Eden500V, Eden260V, Fortus400MC, uPrintSEPlus and Mojo. Additional additive manufacturing equipment arrives at the end of this month. For insight on the recent expansion and the 3D printing industry at large, we recently interviewed Fathom’s General Manager Dylan Oliver who joined the team in 2010 and has been a major contributor to the companys growth in the Washington and Oregon area [ click here to read the Q&A ]. Joining him in Seattle is Scott Cullum, Senior Support & Prototype Engineer and we had a few questions for him too! Get to know Scott in this weeks featured interview:
Fathom has been supporting the Northwestern region with 3D printer sales, support and services since 2008 — tell us about the upcoming expansion and what residents of the Washington area have to look forward to after its grand opening in fall this year.
Answer: The development of this brand new prototyping facility will be a major asset to companies located throughout the Northwest. Whether a company wants to develop a concept model to communicate an enhanced design or build a fully functional prototype for validation/testing purposes, we can make it happen. We will provide state-of-the-art technologies combined with the highest quality materials and stellar customer service. As a result, our clients will improve their product development processes and introduce better products to the marketplace.
The workshop is located at the corner of Stone Way N and 43rd Street — why did the Fathom team choose this location?
Answer: We chose this location for several key reasons: it is a central location that makes it easy for clients to pick up orders and attend events and seminars. Wallingford is a neighborhood with an eclectic personality, much like Fathom. We have created a central hub for the face of product development and prototyping. Providing free and convenient customer parking was very important to us, along with easy access to major freeways. These simple features are sometimes difficult to find in Seattle, but they make a world of difference to our customer. We strive to continually improve our customer service while maintaining cutting edge industry standards.
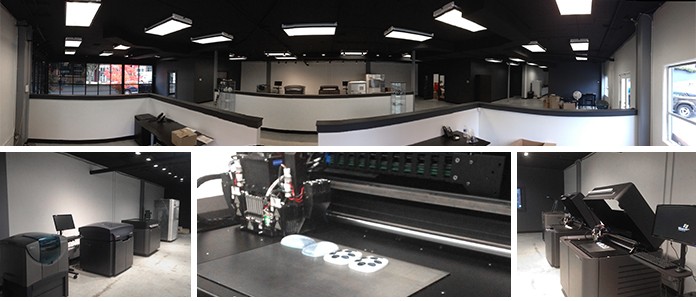
The economy in Seattle is split between older industrial companies and emerging technology-based startups and is listed as one of the fastest growing cities in the United States according to Census data released earlier this year — what do you see happening in the product development and manufacturing space and how are these companies utilizing 3D printing technologies?
Answer: It’s becoming evident that 3D printing has completely disrupted design and manufacturing… in an amazing way. The evolution of this technology has inherently improved the product development process, making it more efficient and affordable to transform 3D CAD drawings into tangible models and doing so in a fraction of the time. 3D printing is becoming essential if a company of any size wants to compete in the design/manufacturing arena. Using traditional manufacturing and prototyping tools in the past could take weeks and even months to produce a prototype, whereas now you can build better, fully-functional prototypes from end-material simulations in literally just hours. It drastically improves the product development phase, which in the long run allows companies to develop better products. By providing these incredibly powerful tools to our clients, we give them unlimited possibilities. Companies who choose not to use these technologies will soon fall behind the ones that do.
Fathom is a preferred reseller of Stratasys 3D printers and 3D production systems for office-based rapid prototyping and direct digital manufacturing solutions — what are some considerations for engineers and designers who are looking into various 3D printing technologies including Fused Deposition Modeling (FDM) and Polyjet Technologies from Stratasys?
Answer: The largest considerations for these differing technologies are material requirements, surface resolution, build size and application or intention. FDM materials are thermoplastics which by nature are much stronger and heat resistant. They are great for functional parts that endure any type of stress. However, the surface resolution is much finer on a Polyjet machine, when compared to FDM. Polyjet technology provides over 120+ different materials, including elastomeric, rigid opaque, clear, ABS & PP simulations and the amazing digital materials 3D printer that builds multiple-material parts. The type of application often determines which technology to use. The application/intention of the part will dictate the material properties required, surface finish, size, strength, etc. As of now, there isn’t a single technology out there that excels in every single application. Customers get to pick and choose which technology benefits their particular project best, which can make or break their prototype.
Regarding the merger of Objet and Stratasys, blog author Sam Green interviewed Phil Reeves of Econolyst asking what he thought are the complementary strengths of the two companies that make them a good fit — what do you think about these two technologies coming together?
Answer: I was very excited to hear about the merger. Ultimately, the additive manufacturing industry will flourish as a result of this merger. Stratasys and Objet were industry leaders in the 3D printing arena, but they were contrasting technologies. Objet prototypes were famous for their fine surface finish, diversity in material types, high machine output and sleek designs. FDM prototypes were notorious for being extremely strong and durable, fully-functional, highly heat-resistant and production-grade. Both companies had strengths and weaknesses. Now that they’ve come together, I’m sure we will see the best of both worlds combined to lead the additive manufacturing industry into the next stages. Now that 3D printing is becoming more essential to the design and manufacturing industries, these machines are heavily relied upon, which creates more demand for better materials, higher quality models, faster output and more affordable machinery. I look forward to the beneficial impacts on design, engineering and manufacturing from Stratasys as the technology continues to evolve and re-shape our world.
Forbes published “Manufacturing the Future: 10 Trends to Come In 3D Printing” by Eric Savitz at the end of 2012 — with more than half the year over, would you say Savitz’s predictions have come true so far?
Answer: I believe these predictions are completely legitimate. The benefits of additive manufacturing and newly discovered applications every day are rapidly changing the world around us. From bio-printing organs, to mall kiosks, to 3D printed automotive and aerospace parts, we can all see the dramatic impact this technology is having on any industry that produces a physical product. Many of the trends outlined in this article have already materialized and the rest are not too far off. I have personally installed machines in many schools and universities around the country and trained educators to teach the new generation about this emerging technology. Students will soon be exposed to 3D printing at a very early age, which I believe will spark creative interests allowing them to solve complex problems by creating tangible solutions. That’s what product design is all about at the root… problem solving using creative methodology.
3D printing has long been used for creating rapid prototypes but users are rethinking how to use these technologies, creating all sorts of 3D printed parts for end-use — tell us about some of the ways you’ve seen Fathom customers utilize these advanced technologies?
Answer: We are incredibly fortunate at Fathom to see industry leaders utilizing 3D printing technology for various unconventional applications on a daily basis. We are exposed to this so often that it’s beginning to seem almost normal. The intensive rate of creation is becoming standardized to us, whereas others are instantly amazed at the very site of a 3D printer materializing a part from thin air. I have worked on many projects with our clients using this technology to create cutting-edge medical devices, custom surgical guides, end-use electronics housing, custom prosthetics, consumer gadgets and the list is literally endless. Every project is incredible it its own way and the utilization of additive manufacturing has benefited them immensely. One application I am very excited about is rapid tooling: Using a 3D printer, you can build mold cavities used for RTV or injection purposes for low-run production. This also allows a company to simulate mass production and work out any problems they may encounter. In the past, a company would spend tens of thousands of dollars on a project like this and it would take months to complete (typically done overseas). The same process now is a fraction of the cost and consumes a fraction of the time as traditional tooling methods.
Fathom has some exciting news to share in the upcoming months leading to the Seattle office opening — what do you enjoy most about being part of the 3D printing industry and the Fathom team?
Answer: The most rewarding aspect about working with Fathom on the front end of the 3D printing industry is the direct exposure to the newly developed products that shape our society. We have the most innovative clients in the world and many of them have created the products surrounding our lives. These products make our lives easier and more efficient and it’s invigorating to see concepts come to life, then see them on a shelf at a local store. It’s exciting to see 3D printing used in so many different ways to benefit each industry and application differently. It really is a universal technology that can be catered to any process or industry. This new wave is being referred to as a paradigm shift and second industrial revolution because it truly is disrupting the way we design, develop, engineer, create, prototype and build all of the tangible products in our world. I am incredibly fortunate to work with so many different companies in a variety of industries. There’s never a dull day because each day I learn something new. The creative energy in our studio is electric and almost surreal. We have an amazing team at Fathom and the best customers you can imagine. I get to see first-hand how people are pushing the limits using this technology and the effect it has on the world of design and manufacturing. The Seattle studio opening is another exciting Fathom milestone that re-instates our passion for creative development and manufacturing technology and our commitment to make it readily available to all of our customers.