PolyJet Fixtures / / 3D Printing Jigs & Fixtures Application Story
On production floors worldwide, people depend on jigs and fixtures to enhance manufacturing processes—custom-made tools that enable steps such as alignment, assembly and work holding with optimal efficiency and minimal scrap. These crucial components are often made with CNC machining or other in-house fabrication equipment, commonly in one of the final steps before production can begin. Switching jig and fixture fabrication to 3D printing instead results in faster turnaround, improved efficiency and performance through greater design freedom and frees up production equipment to focus on production. In this featured blog post, Fathom takes a look at a Stratasys application story that demonstrates the use of 3D printing as a fast and cost efficient alternative for making jigs and fixtures.
FEATURED APPLICATION STORY
Rutland Plastics, located in Rutland, United Kingdom, delivers custom injection molding services and products to a variety of companies and industries. Many of the manufacturing and inspection operations Rutland performs require the use of jigs and fixtures to hold and position its injection molded parts.
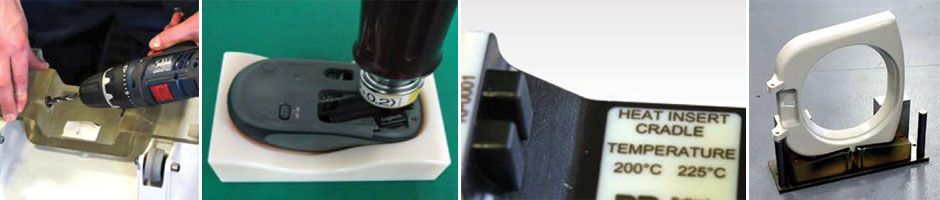
Most of the fixtures Rutland creates are designed specifically for each client’s unique parts. This meant that Rutland needed a low-cost solution for producing numerous jigs and fixtures within a day, something not possible with traditional CNC machining. A typical CNC machined aluminum fixture took at least three days to make and cost about $1,500.
Another obstacle was that Rutland was machining its fixtures on the same machines used to make injection molds and Rutland managers were reluctant to stop production of revenue-generating molds to make fixtures. In addition, identification labels and soft-touch pads had to be added to conventionally-machined fixtures, requiring secondary steps and added time.
As a solution, Rutland engineers took advantage of the multi-material capability of their Connex Technology-based 3D Printer, previously used for in-house prototyping, to make jigs and fixtures. This allowed them to quickly produce custom fixtures with a rubber-like interface to prevent marring and an embedded identification label, all in a single operation.
Carl Martin, technical manager for Rutland Plastics, noted that the cost of producing the typical fixture has been reduced to $900 and the lead time dropped to 24 hours. The process is also more efficient since engineers can simply set up the 3D printer and walk away, letting the 3D printer do its work overnight.
“We can produce jigs and fixtures in a fraction of the time and cost on the Objet 3D Printer, without tying up production machinery,” said Martin. Additive manufacturing eliminates the constraints of CNC machining, which makes it possible to improve the productivity of our operations by improving the functionality of the fixtures.”
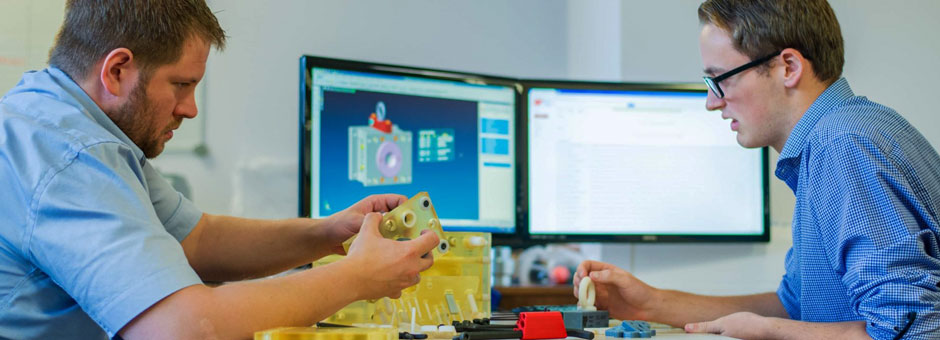
To speak with an additive technologies expert about your jig or fixture application, start a conversation using the contact form on the right.
Thanks for reading a Fathom blog post! With so many developments in a fast-changing industry like additive manufacturing, the headlines can really stack up. To cut through the clutter of 3D printing news, follow our weekly blog Change is Additive for our staff picks of the week.