3D Printing Wearable Electronics
“Fathom provided a true partner experience for us. Don’t just look for a vendor, look for a partner with a team you can trust. When both parties can contribute their expertise, you get a better product and greater results.”
— Paul LaPorte, Founder & CEO Shockatoo
CHALLENGE
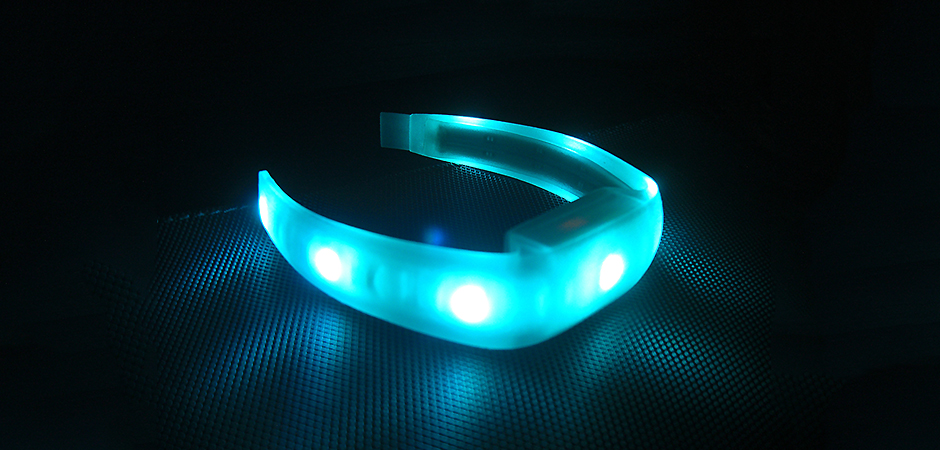
Shockatoo, Inc. is an innovative producer of wearable technology targeted at the consumer market. The company wanted to develop a flexible, translucent plastic prototype for their Kickstarter project — Fusion, a music-connected smartband designed to sense and respond to music and motion with bright, colorful, animated light patterns. The prototype would house the wearable consumer electronic device and needed to be fully functional for a video shoot in Las Vegas to promote the product launch. The product development team needed to find a cost effective iteration process that would allow for multiple design changes and material customization with quick-turnaround.
PRODUCT OVERVIEW
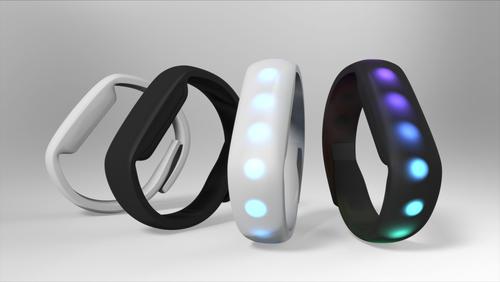
Re-imagining the way people interact with music, Fusion by Shockatoo is a music-centric computer for the wrist, combining a built-in accelerometer, microphone, microprocessor and Bluetooth 4.0 that allows the device to operate intelligently on its own. Fusion integrates the audio of music, the visuals of a concert lightshow and the kinetic energy of dance. The Smartband creates animated light displays by sensing both the beat of the music and the user’s motion. When paired with a smartphone using Bluetooth, users can select and download hundreds of interactive light patterns, play one to fit their mood or create their own and connect with friends by letting users sync to each other.
SOLUTION
The Shockatoo team leveraged Fathom’s in-house additive manufacturing services, 3D printing material expertise and creative technical professionals to meet their aggressive product design schedule and unique product specifications. Fathom manufactured 3D printed parts for two design cycles in less than two weeks. The first cycle helped dial in the product design and also determine which custom blended materials created the required feel and translucency. Finished parts were achieved in the second cycle and were expedited to Las Vegas for Shockatoo’s promotional video. The final prototype captured the flex, finish and light transmission that Shockatoo had envisioned for their new product line. “Our team was pleased to have been able to make design adjustments so quickly,” said Paul LaPorte, Founder and CEO of Shockatoo. “The team was able to test out various material combinations to get the desired result and we hit a home run.”