Make the Unmakeable #3: Winner Q&A
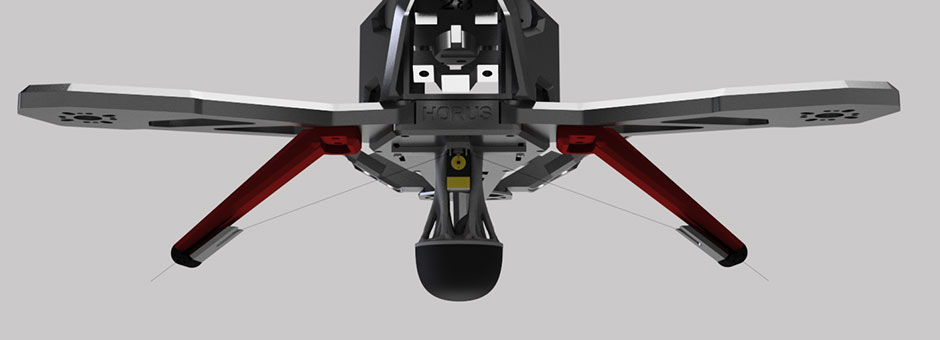
Fathom partnered with GrabCAD and SolidProfessor in hosting the third round of the 2015 Make The Unmakeable Challenge. Each round of the competition dared designers and engineers to innovatively utilize the unique design freedom of additive manufacturing in creating inventive products related to a specific theme. Round three focused the designers on developing attachments and additions to the Horus Kestrel 3D, an open-source 3D printable drone.The panel of judges recently announced Casey Rogers, a recent graduate of UC Berkeley and Co-President of the Berkeley 3D Modelling Club, as the winner of challenge #3 for his Quadcopter Universal Gripper Accessory design.
With the conclusion of the third round, Casey now moves into competition with round one winner Devin Sidell and his Grow Pod concept and round two winner Winston Jennings and his Sphere Wall Mount design. The three finalists will now vie for the title of 2015 Make The Unmakeable Challenge Champion and the grand prize, a uPrint SE professional-grade FDM 3D printer.
The Quadcopter Universal Gripper Accessory will allow the Horus drone to be remarkably dexterous in gripping objects. In your design submission, you mentioned construction as an industry that could benefit from the gripper— what are some of the other applications you envisioned for this design?
One of the more novel applications which I left out of my entry’s description—I was worried it’d complicate the vision of the project—was using the gripper as an incredibly versatile landing gear system. For example, imagine a quadcopter with arms at the front for manipulating and soldering wires in addition to the gripper at the base. The quadcopter could fly up to the top of a cell tower and apply the gripper to any adjacent bar or pole and hold itself in position using the gripper while the arms on front perform repairs to the cell tower’s equipment. For a more mundane application, a quadcopter could use the gripper to attach to a high-up tree branch and then saw the branch off using a sawing mechanism attached to its front.
The power of the universal gripper is in, well, its universally applicable function.

Are there any particular features or strengths of the universal grabber that are only possible to achieve through 3D printing? What precludes them from production through traditional manufacturing?
For this project I really tried to focus on creating something that leveraged the strengths of 3D printing, as opposed to just being printable. The organic branching structure and complex geometry of the arm reduces weight while maintaining strength but cannot be manufactured using traditional methods because of its intricate shape. I also used living hinges in the landing gear by leveraging 3D printing’s ability to print in multiple materials. In each component of the design there is one or more ways 3D printing was used to improve the component over a comparable traditionally manufacturable part.
How does the design utilize materials uniquely available to additive manufacturing? Are there any specific chemical properties you singled out that allow the gripper to function?
Rather than specifically using unique materials or chemical properties, I leveraged 3D printing’s ability to change the physical properties of a material by 3D printing the material with minute structures. The universal gripper project by Cornell University and University of Chicago was my inspiration for the quadcopter gripper. In the original project, the end of the gripper was filled with coffee grounds. The coffee grounds stiffen in place when suction is applied, giving the mechanism its unique gripping power. For my gripper I’ve proposed using small 3D printed particles whose structure can be designed to improve their stiffness when compressed and thus improve the gripping strength of the device.
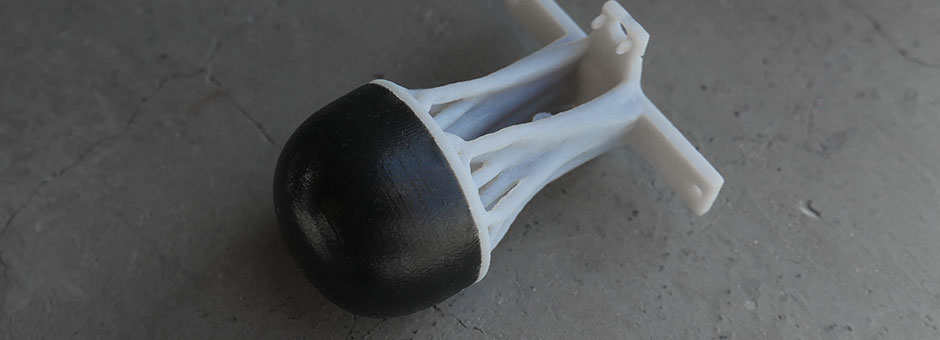
How did you first become interested in additive manufacturing and design? Have you created any 3D printed projects in the past?
I first started working with additive technologies my freshman year at UC Berkeley via a 3D printing club on campus called 3DMC. Since then I’ve worked on countless projects. This past summer I had an internship with a 3D printing startup working with direct metal printers. I’m currently interning for Autodesk as a Fusion 360 advocate. I’ve done a lot of work designing 3D printing projects in Fusion, including designing the quadcopter universal gripper arm. Fusion’s robust support for imported meshes, relative to other CAD packages, was key in incorporating the gripper arm’s organic structure into my design.
Now that your design has been selected, you and the two other finalists will compete for the grand prize of a uPrint SE — if you become the Make The Unmakeable Champion, what will be your first project on the professional 3D printer?
That’s hard to say—it’s a really incredible 3D printer and I’d have to make sure to make the best possible use out of it! If I win the 3D printer, I will likely donate it to 3DMC’s makerspace on the UC Berkeley campus and see what kind of cool stuff my fellow club members can come up with!