Material Spotlight / / Agilus30 FAQ
Agilus30 is a PolyJet material released earlier this year from Stratasys and it is a rubber-like material with improved functional performance—two times the tear resistance when compared to Tango and more than two times the tensile strength. With better elongation and less stickiness, this new material is an excellent option for 3D printing seals directly onto a lid, testing wrist band prototypes or making valves for medical devices that can withstand high water pressure. In this featured blog post, Fathom Applications Engineer Tony Slavik discusses the new material and which customer bases use it most, highlighting specific material characteristics that make the durable material stand out / / View Data Sheet for Agilus30
What separates Agilus30 from other PolyJet Technology materials?
Agilus30 is a great next step following what Stratasys already offered in terms of 3D printing rubber-like parts. The increased tear resistance really elevates the viability of testing designs thoroughly.
What do you see as the most likely applications of this material? What industries could benefit the most from using it?
Many industries stand to benefit because this material can meet many application needs. Agilus30 is another step closer to being a direct replacement for injection molded rubber parts. Its not quite there, but it serves myriad purposes. Examples of applications include over-molding, soft-touch and hinges, hoses, seals and gaskets, as well as knobs, grips, pulls and handles. Agilus30 can also be combined with additional materials to create a wide range of Digital Materials with varying Shore A values, shades and colors.
What industries will use Agilus30 the most?
I see a lot of current medical applications making great use of the material and the consumer electronics will definitely integrate it—especially those in the wearable technology space.
Aerospace and automotive manufacturers have used FDM for many end-use applications. With the improved mechanical properties of Agilus30, do you see it being used further downstream in product development?
Yes and no. I would say it really just gets wider in the development and testing stage. Agilus30, like other PolyJet materials, is still limited in its viability to make end-use products and replace other large scale rubber manufacturing methods. At the moment, these materials only mimic engineering-grade thermoplastics.
What are the colors and textures available using Agilus30?
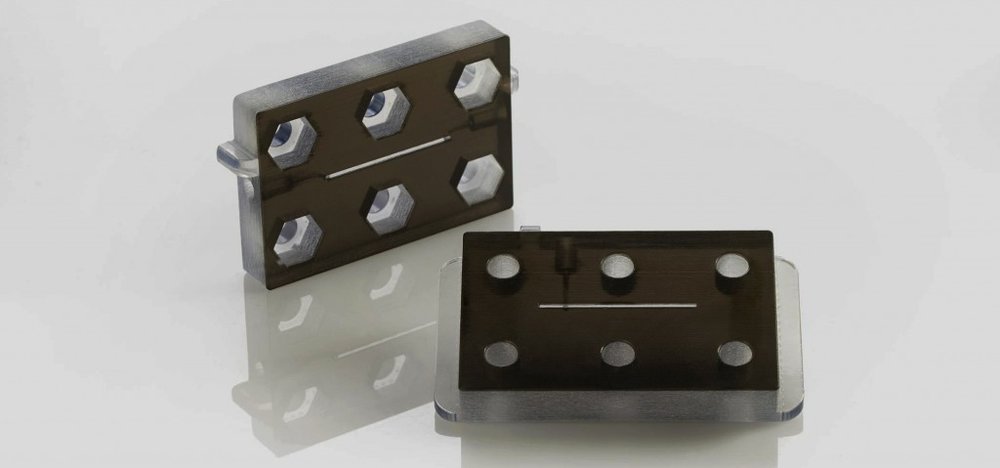
Currently, Agilus30 at Fathom comes in translucent—its effectively a direct improvement of the Tango family of materials. Agilus30 may be digitally blended with other PolyJet materials to get a variety of durometers, colors and translucency.
Is there a distinction between the surface finish available to Agilus30 and that of other PolyJet materials?
This mostly depends on the 3D printer thats used except for one key aspect—Stratasys has minimized the sticky surface feel with Agilus30 that can sometimes develop using the Tango materials, especially when glossy. Expect a less tacky surface with Agilus30.
What can Fathom customers expect in terms of cost and lead-time for Agilus30?
The new material is slightly more expensive than Tango+ and lead time is generally two to three days. Fathom currently offers the translucent Agilus30 material as a standard option, as well as digital combinations with other materials. Due to popularity, our production center will continue to offer Tango family of materials ranging from black to translucent. If you arent sure if this material is right for your application, speak with a Fathom expert about all of our 3D printing and additive manufacturing material options that span seven technology types.
For Stratasys machine owners, what systems are compatible with Agilus30?
Fathom is currently running the material in-house using our Connex3 systems, but Agilus30 is compatible with Objet260/350/500 and Connex1/2/3 systems. For more information specific to machine owners, read more in this machine-focused blog post / / Read Q&A for Machine Owners
Image Credits Include Stratasys