Prototype to Production in 8 Weeks
Infinite Uptime is an Internet of Things (IoT) solution for machines to quantify productivity, quality, monitoring and maintenance. The device is controller- and machine tool-independent and uses proprietary on-board analytics, as well as unsupervised learning for pattern recognition—it is a 5-second install plug-and-play solution that can transform even a WW-II machine tool into a smart connected machine.
Origin Story
Fathom consistently works with companies that see common problems as challenges for the taking—what is the inspiration behind Infinite Uptime?

Bhinge: The manufacturing industry is a traditional one, which has taken time to embrace the digital era using new data-driven technology. The main reason is the fragmented structure of the industry, different machine tool builders and controller manufacturers using different data protocols and the inability and unscalable nature of extracting data from the existing infrastructure. Infinite Uptime aims at providing a new source of data extraction to machines independent of machine tool or controller, which is completely scalable and leapfrogs the industry into the digital era.
Describe the product itself—who is the target user of your product and how does the product change their experience?
Bhinge: Infinite Uptime is an IoT solution for machines to characterize productivity, quality, monitoring and maintenance. It is controller and machine tool independent and uses proprietary on-board analytics as well as unsupervised learning for pattern recognition. It is a 5-second install plug-and-play solution that can transform even a WW-II machine tool into a smart connected machine.
A connected machine is one which is completely characterized in terms of production, quality, monitoring and maintenance. We create tremendous value in terms of productivity improvement, downtime reduction, quality improvement and automated predictive maintenance.
Who are your most prominent collaborators? How did the business get its start?
Bhinge: Our most prominent collaborators are Autodesk, Siemens and Foxconn and these are the customers who saw immediate value in our solution and our technology. However, the initial jump was provided by Carl Bass, CEO of Autodesk who shared our vision in creating a machine-agnostic solution for the manufacturing industry.
Creating & Iterating Designs
In the course of product development, design changes happen often and frequently for a variety of reasons such as look, feel, and functionality—what are key lessons learned from the product development process to bring Infinite Uptime to life?
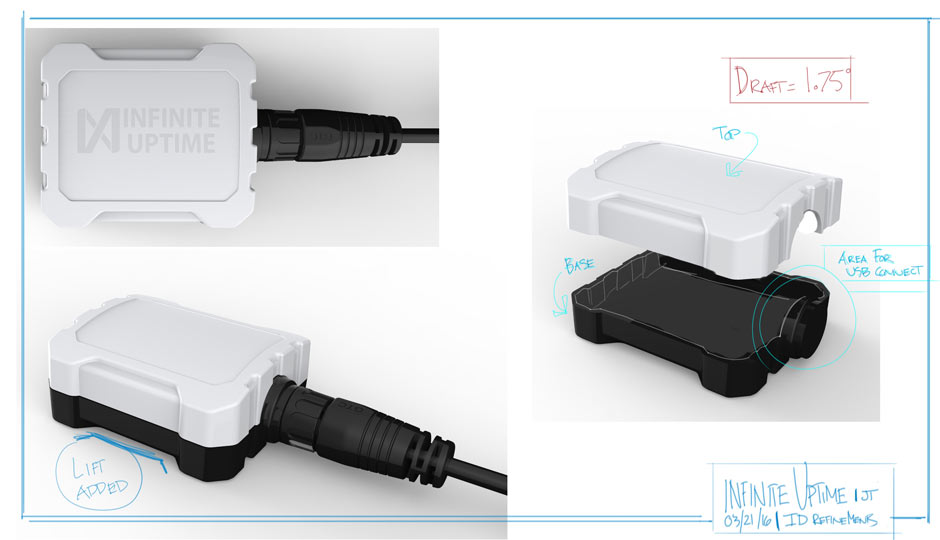
Bhinge: Material selection is much more important than we initially imagined. Everything in the design process and manufacturing process revolves around the selection of the right material. The further we go down the design and manufacturing path, the less leverage we have on this important design choice. We went through a few different iterations to actually nail the right material.
We went through 3D printing in FDM, to PolyJet, to urethane casting and finally to injection molding. Fathom’s approach and means of production fit in with our product development at each step so it worked very smoothly. All our newer products are going through the same phases of prototyping and production.
Did 3D printing allow you to test more prototypes or to speed your product development?
Bhinge: Absolutely. Making minor adjustments on 3D printed prototypes and using 3D printed sectioned prototypes for Design for Assembly was absolutely critical and time-saving.
3D printing is the cheapest and fastest way to get samples in your hand which you can assemble and troubleshoot early on saves months of work. There is no mold or fixture design involved and it is also extremely useful during DFMA. Going through the assembly steps on a 3D printed prototype is of tremendous value.
Our initial design was with a complicated gasket and Fathom’s design for manufacturing (DFM) cut the bill of materials (BOM) down, reduced assembly steps and balanced the use of off-the-shelf parts in the assembly and specially designed features. It made sourcing a lot easier as well with Fathom’s network of sources for all kinds of prototyping needs.
Were there any challenges that only proved solvable through working with Fathom?
Bhinge: Waterproofing is a key feature in our application. Machines in production environment are covered in coolant, grease, oil and other liquids. Designing for IP66 waterproof standard was critical.
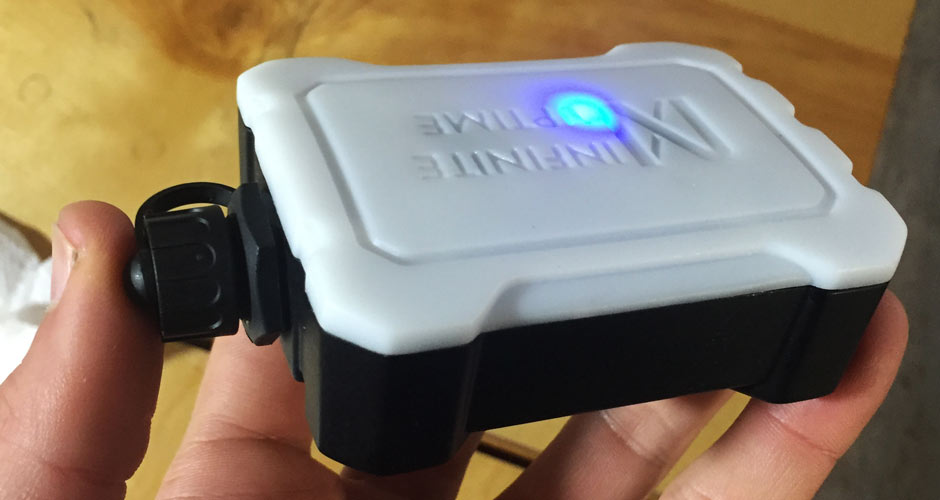
Ultimately, Fathom was amazing in providing a solution which works in the harshest of manufacturing environments.
To learn more about Infinite Uptime, visit the website: infinite-uptime.com. To read more about accelerated product development with Fathom, check out other blog posts documenting our work with women’s health startup NextGen Jane, NFL fitness product startup Recoup Fitness, professional sports footwear with Brooks, mobile charging company Doblet and direct digital manufacturing versus injection molding with Intel.
Have a project that could use a boost? Start a conversation with us today!