Make the Unmakeable #1: Q&A
Fathom is challenging all creative professionals to think differently about how they design, prototype and manufacture products today. This year, were hosting three different 3D CAD challenges on GrabCAD, known collectively as the Make the Unmakeable Contest. Winning submissions selected by a panel of high-profile judges will demonstrate original ways 3D printing can enhance the product development process. Three winners will be awarded a $2,500 credit for 3D printing services from Fathom production centers and other great prizes (full details). Then, judges will name one of those three winners Make the Unmakeable Champion of 2015 and will be awarded a professional 3D printing system (uPrint SE) from Fathom. With only days left for the first challenge and more than 100 entries, we asked our Lead Industrial Designer Veronica De La Rosa to weigh in on what she thinks of the challenge. If you have questions about this interview, leave us a comment or reach out to us on Facebook.
The Fathom team shares a deep passion for improving the world we live in by leveraging our creativity, innovation and expertise for a purpose greater than ourselves — what was the inspiration behind this first Make the Unmakeable Challenge?
Veronica: We spent quite a bit of time trying to decide what this first challenge should be. We wanted to provide people with enough leeway to be creative while also challenging contestants to use that creativity to solve an important and relevant problem. The big question for us was what that problem should be. It wasn’t until one of our principals, Michelle Mihevc, said the words “New Year’s resolutions” that it all clicked for us. We really gravitated to this idea because everyone can relate. Whether or not one personally partakes in this tradition, I’m sure everyone has friends or family members that start their year with a promise of self-improvement. We also thought it would be a great time to introduce this challenge, seeing that a large portion of people’s resolutions start to lose momentum around the time this challenge started.
The unlimited design freedom that comes with 3D printing can sometimes be challenging for designers and engineers because anything is possible — how do you approach product design differently than when you only had access to traditional manufacturing methods like CNC machining? What should creative professionals keep in mind when designing?
Veronica: The great thing about additive manufacturing is that it supports “outside-in” thinking. With additive manufacturing, a designer can focus on what the product does as opposed to being confined to how it’s going to be made.

Traditional manufacturing processes can limit initial concept exploration while additive has the potential to actually drive innovation. Your initial designs are not at the mercy of what has been done in the past, but rather provide a vision for what is possible.
Take, for example, the Calibowl. This product is a bowl with an undercut lip that helps keep contents within the bowl. We used 3D printing to transform our CAD into physical models, allowing us to validate the design with consumer feedback. Upon discovering we had a winning idea, we then had to determine how to manufacture the bowl. By pushing the limits of our injection modeling team, we were able to develop an innovative solution for molding that many traditional facilities considered an impossible undercut to injection mold. If it weren’t for the design freedom that 3D printing offers, an innovative consumer product like Calibowl would have never been realized.
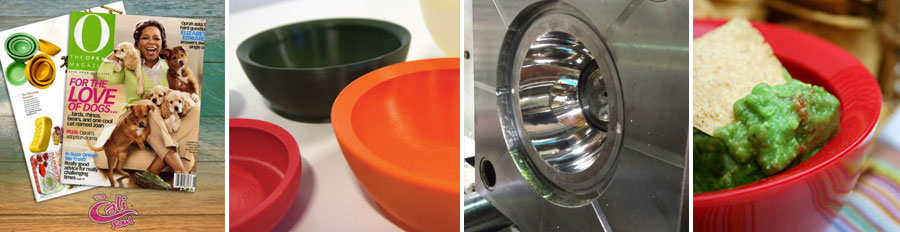
Make the Unmakeable Contest from Fathom is not very restrictive — what is your advice for engineers and designers who are submitting entries for the first challenge?
Veronica: I think this is a great opportunity for designers and engineers to truly challenge themselves. This is not an easy competition, considering the first challenge is very broad and does not define the parameters of the problem to work with. This amount of freedom can be very challenging for some and therefore requires work on part of the contestant to define the specifics of the problem they want to solve. I think the best way to start this process would be to begin by researching the problem itself. Understanding the resolution and really educating oneself on the subject matter will produce richer and more relevant submissions.
I would also try to avoid messaging; designing something that simply tells you to abide to your resolution. This challenge requires you to investigate how something physical (your design) can effect a mental experience (the habit). Along the same lines, resolutions tend to be directed at the individual. Since every individual is different, customization can be a valuable feature of design proposals, which also happen to be well-suited for additive manufacturing.
One topic of conversation that consistently pops up at Fathom is how to create a healthier work environment. Many of us agree that a standing desk could really improve our lives. Unfortunately, adjustable standing desks tend to be pretty expensive. But what if you could print a mechanical solution that could easily adjust any standard desk from a sitting to standing position? This could really be a real game-changer for the furniture industry and corporate health.
To learn more about Fathom’s fully offering, download an overview of our services.