CNC Milling Services
Bring us your challenging custom CNC milling jobs – the ones that other shops back away from. Fathom can easily handle complex geometries, tight tolerances, and short run/high mix projects with exotic, hard-to-cut materials and unique finishing and assembly needs. Bring it on. Our CNC milling services are trusted by blue-chip customers in the defense, aerospace, medical and other high-performance industries.
How Does CNC Milling Work?
A cutting tool mounted on a rotating spindle selectively removes material from a block of metal, following instructions from a CAD drawing. The workpiece, the material to be cut, is firmly mounted to a table. The tool then moves around it to mill or cut material to achieve the required shape. Using different tools, it can also cut cavities and holes in the workpiece as needed.
Three-axis milling machines can cut three surfaces of a part along its X, Y and Z axes. This type of mill can produce simple parts with uncomplicated geometries. A 5-axis mill adds two rotational axes to give milling tools access to five out of the sides of the part, enabling it to create more complex shapes. This type of milling machine eliminates the need for multiple setups and enables multiple operations to be completed in a single step. That saves time.
Most modern milling machines also include carousels of tools, enabling quick cutting tool changes to perform different cutting functions.
Because milling machines can produce parts quickly, with tight tolerances and consistent repeatability, they’re ideal for producing prototype or short-run production parts.
Contact our experts today to learn what Fathom’s custom CNC milling services can do for you!
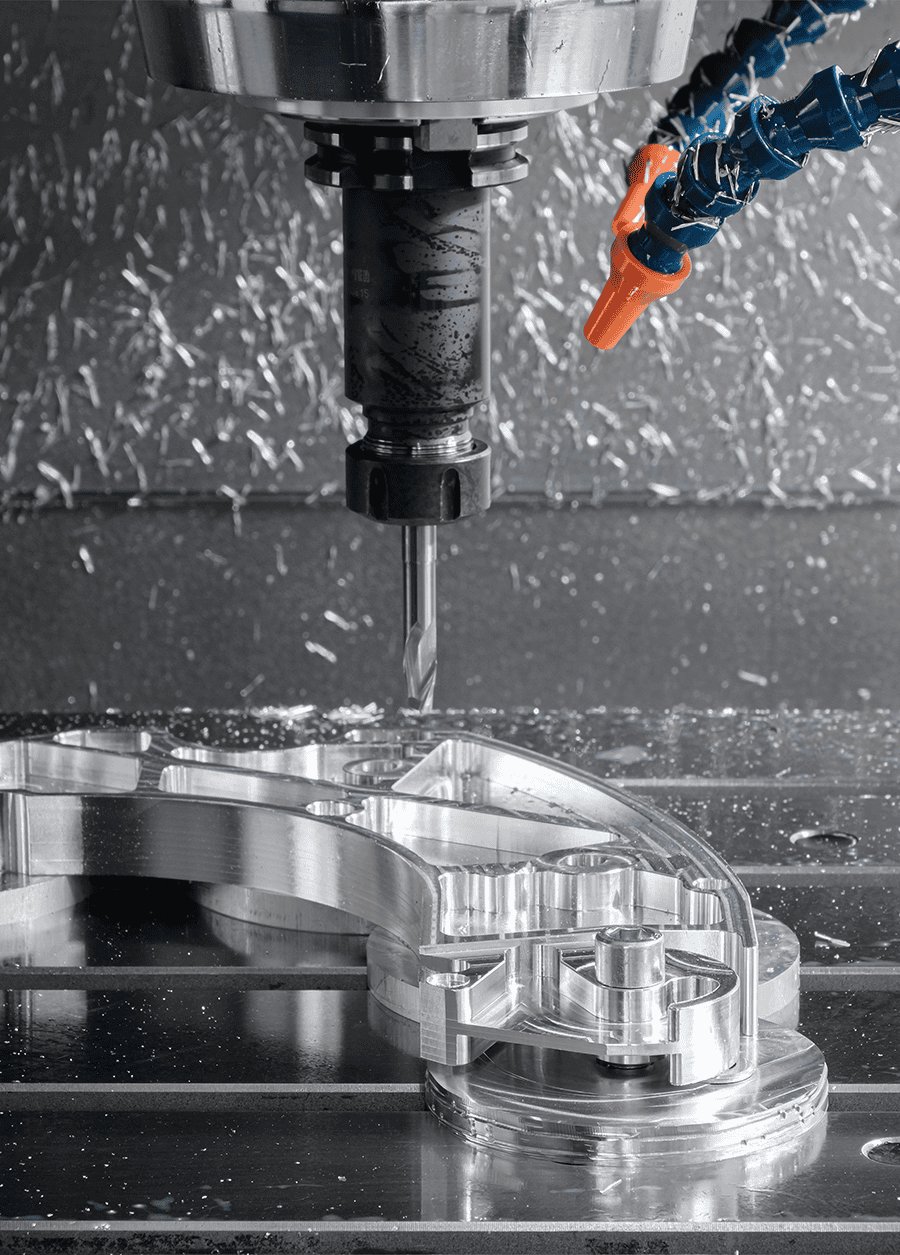
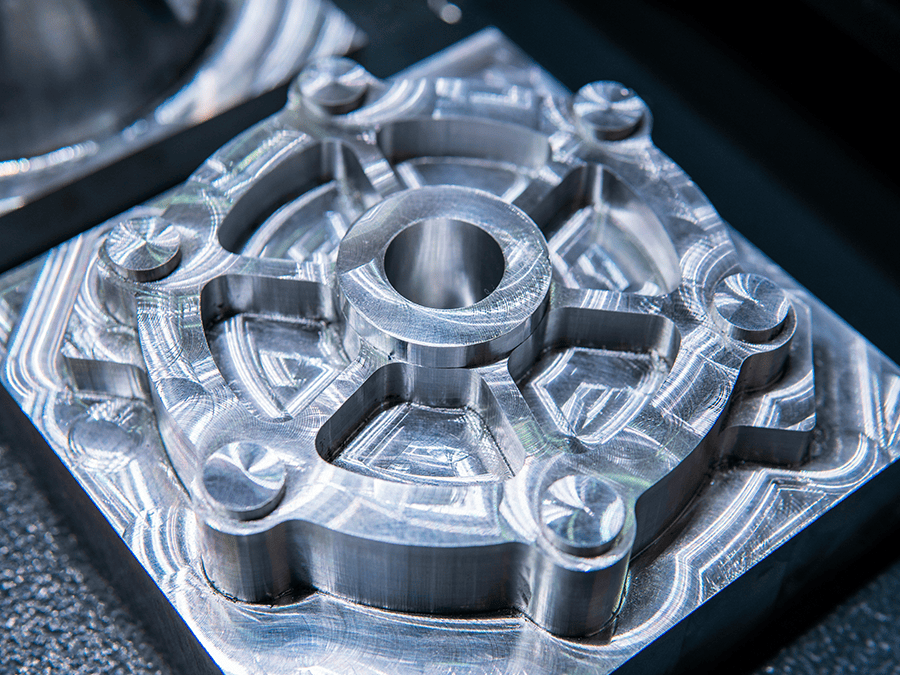
Differences Between CNC Milling and CNC Turning
There are distinct differences between CNC milling and CNC turning. CNC milling uses a moving tool along a stationary workpiece to remove raw material. During CNC turning, the workpiece rotates while a cutting tool moves along the material to create a shape. CNC turning is good for projects that require cylindrical parts. CNC milling should be used for parts that do not require a cylindrical shape and may be used as a secondary finish to add definition. Complex parts that require prismatic and cylindrical features may use a combination of milling and turning.
CNC Milling Material Specifications & Tolerances
METALS |
OPTIMAL QUANTITY |
TOLERANCES (+/-) |
ADVANTAGES & CONSIDERATIONS |
FINISH & |
Stainless Steel |
1-1,000 |
+/- 0.005″ |
|
|
Low Carbon Steel |
1-1,000 |
+/- 0.005″ |
|
|
Aluminum |
1-1,000 |
+/- 0.005″ |
|
|
Brass |
1-1,000 |
+/- 0.005″ |
|
|
PLASTICS |
OPTIMAL QUANTITY |
TOLERANCES (+/-) |
ADVANTAGES & CONSIDERATIONS |
FINISH & |
HDPE |
1-100 |
+/- 0.008″ |
|
|
PC |
1-100 |
+/- 0.008″ |
|
|
ABS |
1-100 |
+/- 0.008″ |
|
|
Acrylic |
1-100 |
+/- 0.008″ |
|
|
Nylon 6/6 |
1-100 |
+/- 0.008″ |
|
|
Acetal (Delrin®) |
1-100 |
+/- 0.008″ |
|
|
ULTEM® |
1-100 |
+/- 0.008″ |
|
CNC Milling Considerations
During the design phase of a CNC milling project, there are several critical factors to consider. The desired geometry of a part affects both how it will be positioned in the CNC machine and the time required for set up. If a part must be manually repositioned in the CNC machine, the cost will increase, and accuracy may be affected. During operation, the part may vibrate and result in loose tolerances. Deformation may occur because of the workpiece vibrating during machining. The geometry of the tools used can also influence how a part is shaped. Lastly, if the cutting tool is unable to reach the surface of the raw material, it cannot be machined, limiting the ability of creating hidden internal geometries.
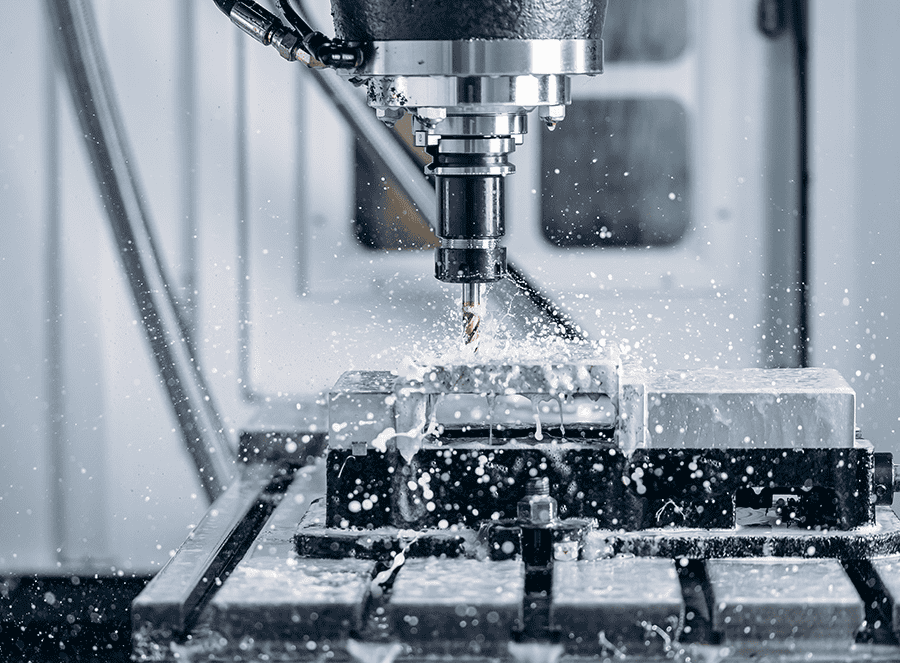
CNC Milling Available Machinery
BRAND |
MODEL |
BUILD VOLUME (in) |
PAR System |
5-Axis |
284 x 112 x 53 |
Haas |
UMC750 SS 5-Axis |
19.7 x 15.7 x 7.9 |
Haas |
VF-9/40 |
84 x 40 x 30 |
Haas |
VF-2 CNC Mill |
30 x 16 x 20 |
Mighty Viper |
Pro 3150-AG |
120 x 61.4 x 32 |
Mighty Viper |
B100 |
50 x 100 x 24 |
Mighty Viper |
Pro 1000-AG |
43 x 24 x 25 |
Mighty Viper |
LG 1000 |
40 x 20 x 25 |
Mazak VC |
Universal 500A 5-Axis |
20 x 20 x 20 |
Mazak |
VTC-30C |
65 x 30 x 26 |
Mazak |
VTC-20B |
44 x 20 x 20 |
Mazak |
Quick Turn Universal Smart 350 |
Lathe 4″ bar diameter, 10″ x 25.5″ |
KUKA |
KRC22 6-Axis Robotic Cell |
w/ Turntable |
Mori-Seiki |
NLX 2500SY 2015 & 2017 |
CNC Lathe |
Makino |
2019 D 200Z |
Carbon Mill |
Makino |
2018 D 200Z |
Hard Milling |
CNC Milling Finishing
Bead Blasting // Bead blasting adds a satin or matte finish to a CNC part. The matte finish is accomplished by using a pressurized air gun to shoot glass beads at a part.
Powder Coating // Following powder coating, the part has a thin protective layer that adds strength and wear-resistance. During the powder coating process, the part is first primed using a chromating or phosphating coat. Next, the part receives a dry powder coating from an electrostatic spray gun. Lastly, the part is cured in an oven.
Anodizing // Once a CNC part has been anodized, it has an oxide layer that increases its density, thickness, and durability. Anodization also makes a part electrically non-conductive. During the anodizing process, the part is placed into an acid electrolyte bath which serves as an anode. A cathode is added to the part, and an electrical current is passed through the acid. Oxygen ions from the electrolyte and atoms from the alloy are combined along the surface of the part.
As-Milled // As-milled or as-machined products do not require a secondary process. They will still have visible blemishes and may have a rough surface.
Surface Grinding // Surface grinding produces a smooth finish. Surface grinding removes material by using a high-speed abrasive wheel as a cutting tool. The surface grinding process is used when a specific size or precision finish is required.
Polishing // Polishing improves the dimensions and accuracy of a part while producing a mirror gloss finish. Polishing tools and abrasive materials are used to achieve a smooth surface.
Passivate // After a CNC machined part has completed the passivation process, its corrosion resistance is improved. Passivation may include spray application, circulation in a chemical solution, gel application, or tank immersion.
Chemfilm // Chemfilm finishing is a chemical conversion coat that adds corrosion resistance to aluminum substrates, acting as a base for organic coatings. The part is dipped, brushed, or sprayed with the chemfilm layer.
Vacuum Metallization // The vacuum metallization process adds a mirror-like or decorative uniform finish while also improving thermal, air, light, or water barrier properties. In the vacuum metallization process, the part is placed inside a closed chamber where a metal vapor adheres and coats the part.
Silkscreen // Screen printing is used to transfer a design or logo to a part. When a part is silk-screened, a mesh is used to apply ink onto the surface, but only to permeable areas that are not covered by a blocking stencil.
Plating // Plating results in corrosion and abrasion resistance, conductivity, and reflectivity to parts. While electroplating, the part is submerged into an electrolyte bath with the material that will be used for the metal coating. An electrical charge causes the material to transfer to the part, resulting in a uniform metal coating.
Tumbled // Tumbling or ultrasonic polishing removes any sharp points or edges from a machined part. During the tumbling process, the part is placed inside a barrel along with media, water, and detergent. The barrel tumbles at different speeds depending on the desired finish.
Painting // Painting a part adds color, varnish, or ink. The painting process may include powder coating, liquid coating, or e-coating. Powder coating uses an electrostatically charged powder which produces a scratch-resistant and uniform coat on the metal part. When a part is liquid coated, wet paint is applied. The e-coating process involves dipping the part into a bath of paint where both the part and paint are electrified, causing the paint to adhere to the part.
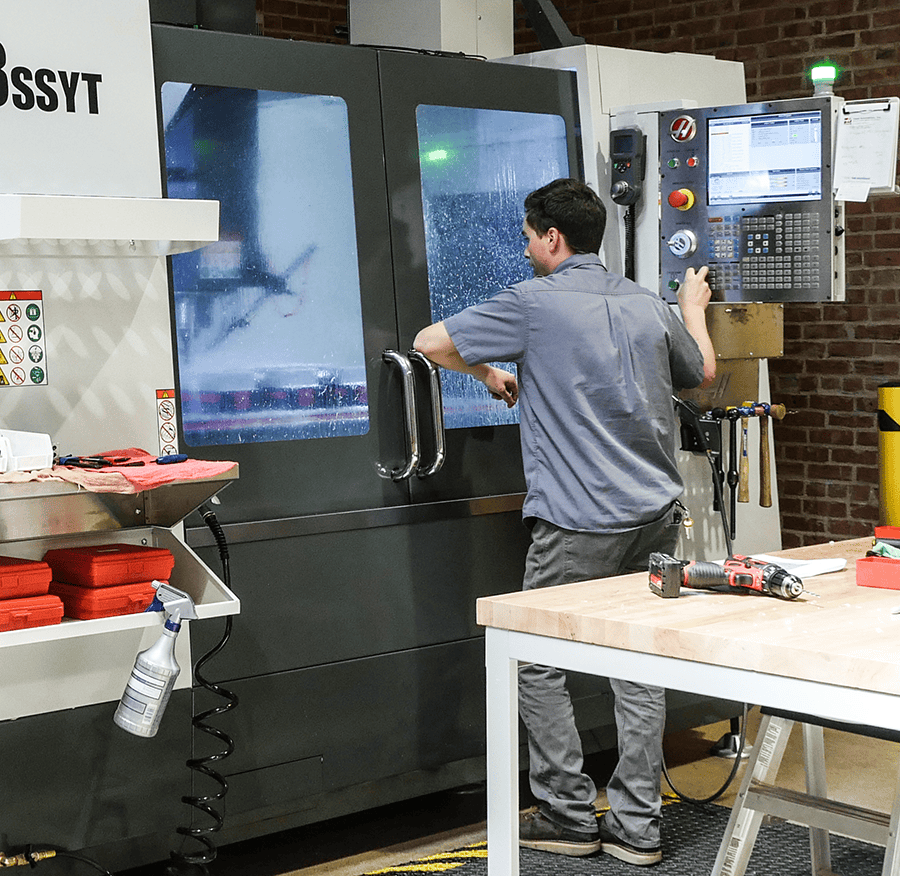
Fathom’s Locations for CNC Services
Fathom’s nationwide network has several locations across the U.S. that offer CNC milling services:
Wisconsin //
Fathom Headquarters
1050 Walnut Ridge Drive
Hartland, WI 53029
Arizona //
444 W. 21st St. Ste. 101
Tempe, AZ 85282
Illinois //
1401 Brummel Avenue
Elk Grove, IL 60007
Minnesota //
13758 Johnson Street NE
Ham Lake, MN 55304
Texas //
1513 Sam Bass Rd.
Round Rock, TX 78660
Choose Fathom for CNC Milling Services
We have the expertise to help you meet your precision CNC milling requirements.
Complex geometries? Tight tolerances? Tough, hard to machine materials? Short-run/high-mix projects? Bring it on. We’re problem-solvers who bring decades of experience to every machining challenge. We have the capacity and expertise to take on your most challenging projects.
When you’re not sure where to turn for precision CNC milling, talk to us. We’ll help you make the design changes, material selections and process and finishing decisions that will ensure we can deliver the parts that meet your requirements.