Family Molding
Do you need to create multiple variations of a part? Do you need to build a group of parts that will be used together – that need to be the exact color and finish? If so, you can produce them in a special type of multi-cavity mold called a family mold.
Family mold injection molding can save you a significant amount of money and time by reducing tooling costs and setup time. It can also help you achieve consistent part quality across all the components you’re molding at the same time.
What is Family Molding?
Family tools are similar to multi-cavity tools:
Multi-cavity Tools // Produce multiple copies of an identical part using a single tool.
Family Tools // Family molding produces a set of related parts that are designed to fit together. All the parts are usually similar in size and quantity. They are molded in the same color from the same material. These multi-cavity molds are often used to build parts for consumer products, where all visible parts need to have an identical color.
Because they enable the production of multiple parts from a single tool, family molds offer significant cost advantages compared to multiple single-cavity molds.
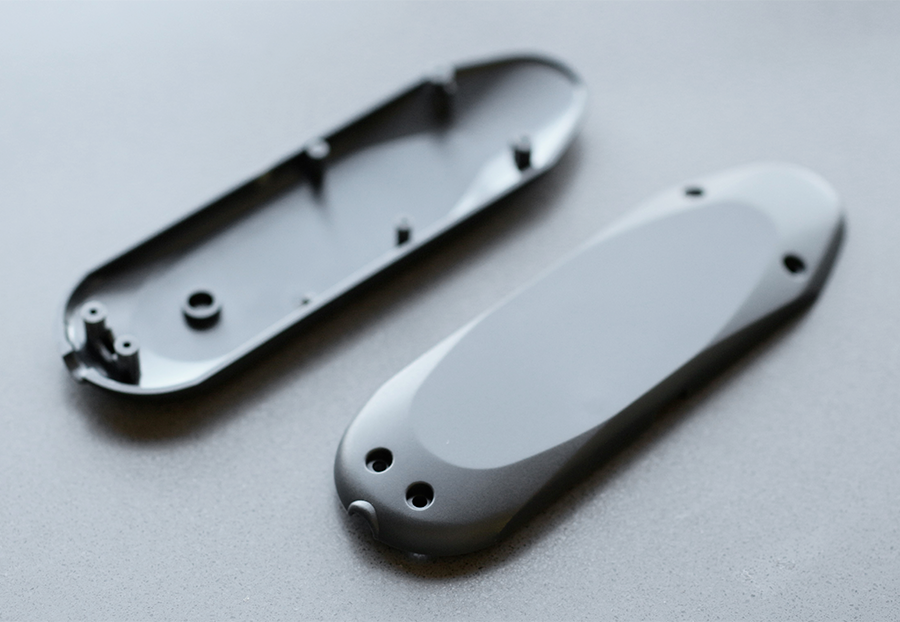
How Can Family Molding Benefit Your Project?
Reduced Tooling Costs // Instead of investing in separate molds for each component, family molding enables you to produce multiple different parts with a single tool, significantly reducing your tooling investment.
Time Savings // Family molds produce multiple parts in a single cycle. That saves time, because it eliminates the need for tool changes. That enables you to focus more time on accelerating your product development timeline.
Lower Production Costs // Family molding reduces labor, material handling and machine setup time by consolidating multiple parts into a single production run. Family molds also require less time on press, which also saves money.
Better Control Over Production Variables // Compared to using separate tools to produce each part, a multi-cavity injection molding tool means fewer opportunities for variances in production settings. With all parts manufactured under identical processing conditions, family molding enables you to maintain consistent quality across components and simplify your QA process.
Simplified Inventory Management // Family molding enables you to produce parts in ratios that match your assembly requirements. That can help you eliminate excess inventory and the associated storage costs.
When Should You Consider Family Molding?
Family mold injection molding is ideal for projects that involve:
- Components with similar material requirements
- Parts with comparable wall thicknesses and cooling characteristics
- Products that require multiple related components in known ratios
- Products with tight budget constraints but multiple-part needs
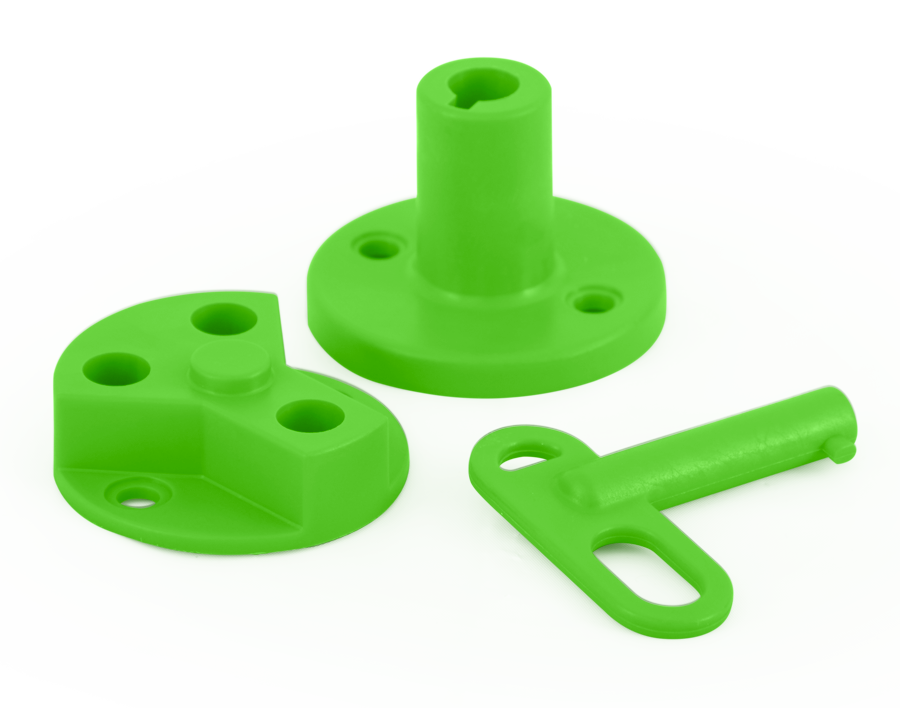
Applications
- Automotive
- Consumer electronics
- Appliances
- Medical devices
- Packaging closures
Industries
- Automotive and transportation
- Medical
- Consumer
- Industrial
- Aerospace
- Defense
- Consumer products
Design Considerations for Family Molding
When considering family molds, you need to evaluate:
Part Size Compatibility // Components should be relatively similar in size to ensure balanced filling and uniform cooling during the injection molding process.
Material Compatibility // All parts must be produced from identical or highly compatible materials.
Quantity Ratios // The number of cavities for each part should align with your assembly requirements to minimize excess inventory.
Processing Conditions // Parts should require similar molding parameters (temperature, pressure and cooling time) to ensure uniform quality of all components in this type of multi-cavity mold.
Production Optimization for Family Molding // Fathom’s experienced engineering team can help you address critical production parameters including:
- Optimizing cavity layouts for efficient material flow
- A runner system designed to compensate for varying part volumes
- Gate placement to ensure balanced filling across different-sized part cavities
- Wall thickness consistency for predictable cooling and minimal warping
- Ejection requirements for all parts in the mold
Failure to properly balance these factors can result in part cosmetic and quality issues. Fathom’s experienced team will guide you through the design process to ensure that your family molding project is a success.
Why Choose Fathom for Family Molding?
Fathom understands that successful family mold implementation requires expertise in both engineering and production management.
Our team brings decades of experience in helping customers optimize their manufacturing processes through intelligent mold design and material selection.
Multi-cavity injection molding tools are complex and require a family molding expert for best results. The mold, runners and gates must be carefully designed and optimized for consistent filling, cooling and ejection of each part.
An excellent place to start with family molding is an assembly that has pairs of parts – such as right and left sides, an upper and lower half or a front and back. Because they are similar in size, you can design a well-balanced tool that performs well and can help you reach your production targets faster.
Let’s get started on your next family molding project!
Additional Resources