The 2018 Innovation Awards
For the sixth consecutive year, the East Bay EDA Innovation Awards ceremony featured trophies created by the Fathom team. The annual event brings the professional community together to recognize and commemorate companies who make cutting-edge contributions in their respective industries. Leading this year’s concept was Industrial Designer Ava DeCapri at Fathom. In this blog post, she talks about what inspired the 2018 design, how it was made and why it represents the innovative work of each nominated organization.

What was the inspiration behind this year’s trophies?
I was inspired by gyroid structures for this years trophy design—an amazing geometry discovered in 1970 by NASA Scientist Alan Schoen that is perplexing to look at and even more vexing to understand. For example, the mathematical equation of a gyroid is complex but there is a trigonometric equation that provides an approximation to the gyroid surface (check out Meet the Gyroid by Adam G. Weyhaupt to learn more).
Other aspects about gyroid structures stood out to me. For example, the gyroid has low density but high tensile strength, as well as interesting optical properties when found in nature (e.g. butterflies wings) which has inspired the scientific work on biomimetic materials. The gyroid has gained some attention recently when MIT researchers 3D printed graphene into a gyroid form (a material that is one cell thick). The gyroid form can be found in nature in the structure of cells phasing between liquid and solid and in some cell membrane structures.
Why did you take this approach?
Fathom just released an open source software for creating complex conformal lattice structures, the Crystallon Project by Aaron Porterfield, that implements the use of the gyroid as one of the base unit cells. The gyroid form is truly in line with the Easy Bay EDAs focus on innovation because it is a structure that is now possible to manufacture because of additive technologies. The complex surface structure of a gyroid would have been impossible to realize without the combined use of modern 3D CAD software and additive manufacturing. The form itself is at the forefront of biomimetic material design and it is inspiring the scientific community to innovate in ways not previously possible.
The final design was 3D printed in nylon using Fathom’s selective laser sintering (SLS) equipment then dyed. The gradual use of darker to lighter shades of blue gives the illusion of sky to impress upon the feeling of limitlessness to innovation.
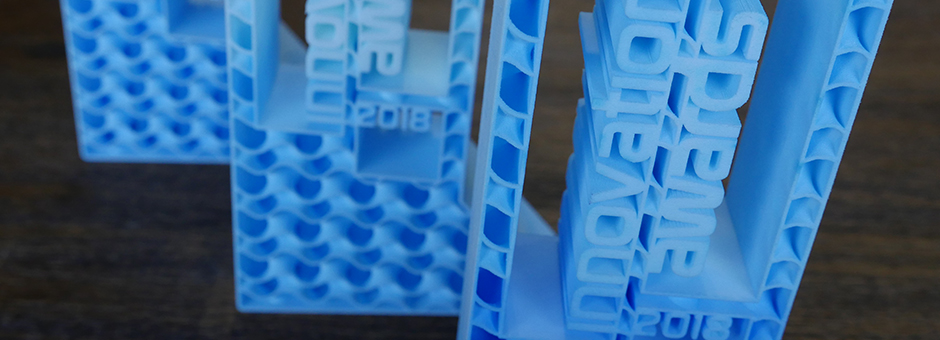
What is the practical application of this approach in today’s product development and production processes?
Although the trophy design was mostly driven by aesthetics, the lattice structure within can be utilized for very technical applications where light-weighting and structural integrity are key. Fathom’s design and engineering team often works with companies in product development who want to incorporate additive technologies into their processes. We are also always looking to work with companies who want to leverage additive technologies as part of their sustainability initiatives to minimize negative environmental impacts.
Those who want to learn more about how to design for additive manufacturing can attend a course led by Fathom’s applications engineering team—many of my teammates are featured speakers. Each session is focused on the practical use of these technologies, materials and process to better help people identify when and how to use it effectively. The curriculum includes an in depth look at topology optimization and lattice structures which features our open source Crystallon Project software.
To learn more about how to design for additive manufacturing, check out the upcoming training sessions. For more information about Fathom’s engineers and designers who can be contracted to support your in-house design teams product development, click through to read about their expertise. Past trophy designs are still available on the blog—check out last year!