Featured Part / / Mounting Bracket
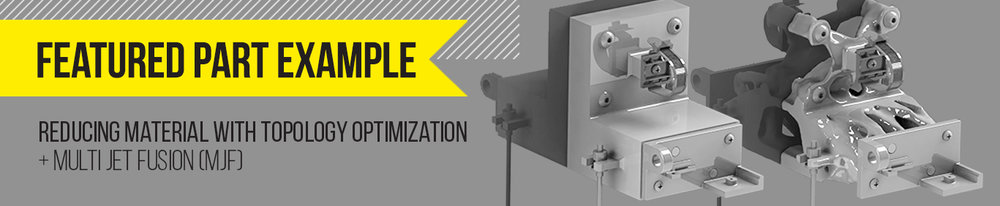
Utilizing Topology Optimization to Reduce Material Per Part by 72%
In this featured post, Mechanical Engineer Alexei Samimi and Application Engineering Manager Tony Slavik highlight the practical application of taking a design for additive manufacturing (DFAM) approach to production parts.
Method Used // Topology Optimization
Original Part Volume // 96,473 mm3 (5.89 in3)
Final Part Volume // 27,181 mm3 (1.66 in3)
Software Used // Solidworks 2018 & ANSYS 18.2
Additive Technology Used // Multi Jet Fusion (MJF)
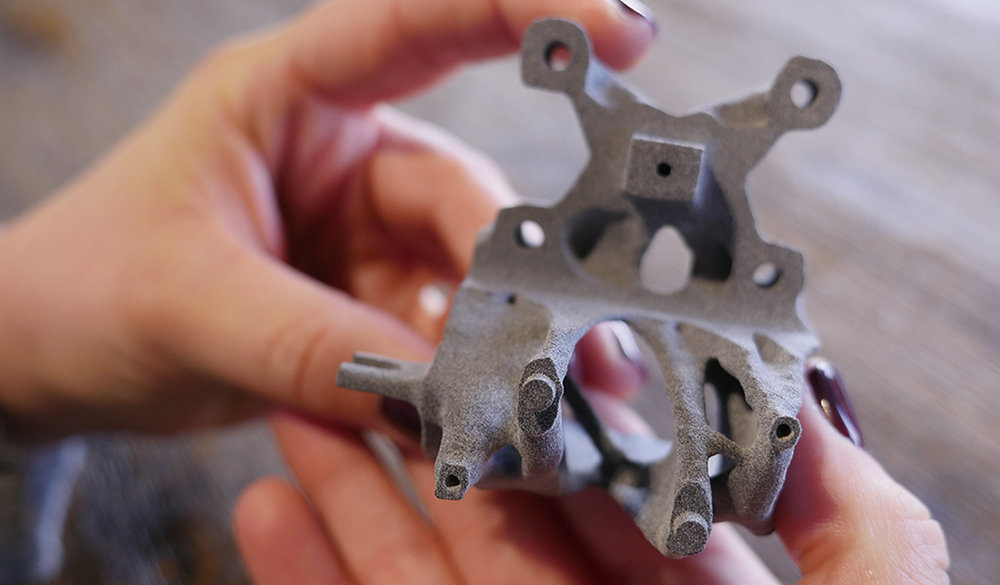
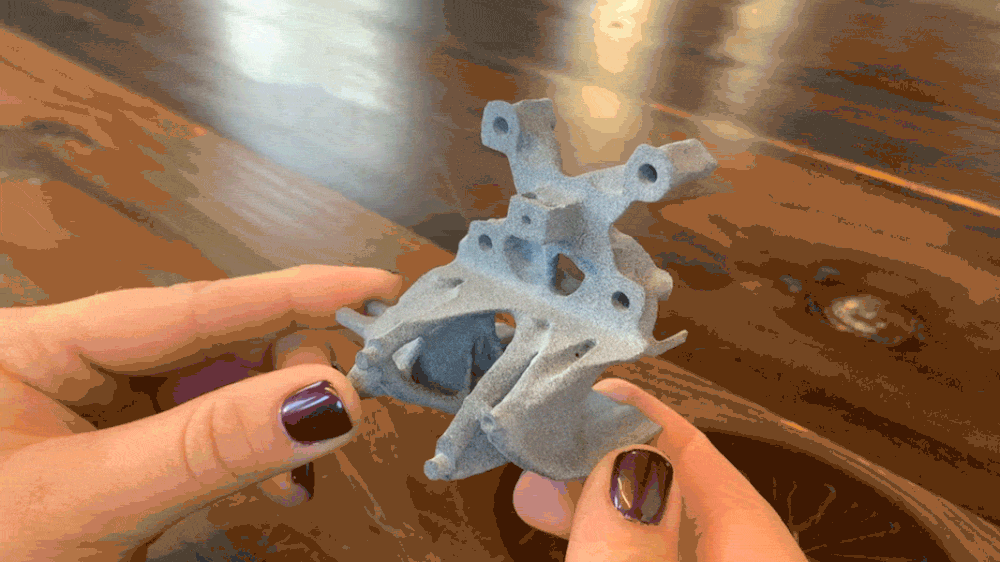
The Part // Sub-assembly within a service station at a manufacturing facility. The actuator assembly (pink) attaches to its front face and a wiring harness (dark green) routes a bundle of wires over the actuator. The wired probe hanging from its side (light green) is used for calibration and diagnostics.
The Project // The goal in this example was to leverage topology optimization to minimize the weight of the bracket without compromising structural integrity. To fabricate this part, additive manufacturing is an ideal method of production because of the geometry, as well as the low-volume of parts required for this type of application (100 units). Multi Jet Fusion (MJF) is an ideal technology because its nearly isotropic material properties are suitable for topologically optimized parts and nylon 12 would also satisfy the strength and impact specifications.
It is also important to highlight how MJF is proving to be one of the more efficient additive manufacturing processes to choose from for short-production runs—designers and engineers are choosing this technology because the process allows for nesting in the z direction. Today, higher quantities of parts can be realized by way of additive manufacturing than previously possible. And, not just a few hundred parts but thousands of parts, even tens of thousands of parts using engineering-grade materials. Even after the break-even point when comparing quantity and cost savings between additive manufacturing versus injection molding, the part functionality achieved can still outweigh the cost of efficiency with a traditional process.
Did you know that Fathom offers a Design for Additive Manufacturing (DFAM) training program that highlights topology optimization? Click thru to learn more about this custom curriculum focused on the practical application of today’s technologies for modern product development.
Learn more about Fathom’s Multi Jet Fusion (MJF) services—upload files and get a quote today!