3D Printing Michelangelo
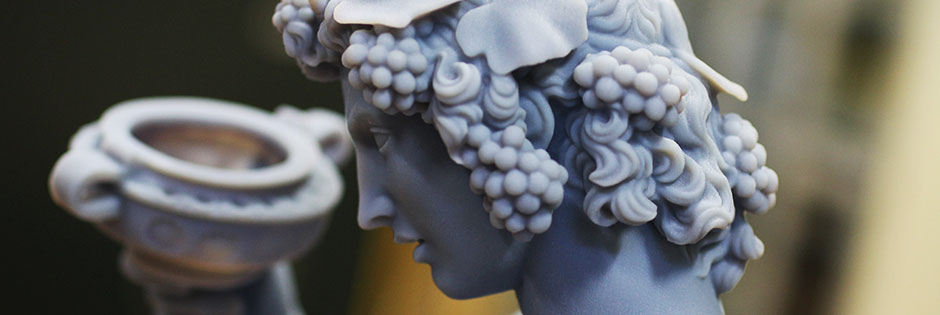

ANCIENT ARTISTRY OF METAL CASTING
— Transformed by Advanced 3D Printing & 3D Scanning
The Thinker. David. Bacchus. Pietà. Michelangelo’s iconic work is widely recognizable, even to those without an extensive art history background. For experts, however, very few replicas have ever fully captured the gravitas of the original sculptures.
Through a revelatory partnership between Fathom, Scansite, and Artworks Foundry for Renaissance Masters, a limited edition of flawless reproductions are being created more than 6,000 miles from the home of the originals.
Enter the advanced 3D scanning, industry-leading 3D printing and expert bronze casting. This collaboration of highly sophisticated equipment and technological expertise from several San Francisco Bay Area companies have transformed the ancient art of metal casting.
“Now we have the facility to be able to reproduce something that is very faithful to the original,” said Piero Mussi, founder of Artworks Foundry, “and that’s something that’s never been done in the past.”
For centuries, sculptors have used the same basic metal casting techniques for one simple reason: the process works. When developing original pieces of art, the age-old conventions are unparalleled, but the challenge comes with reproducing classics that were constructed by the masters.
Mussi learned the ancient art of ‘lost wax casting’ by working with the best foundry masters in Italy. After working almost 40 years in an essentially unaffected trade, Mussi sees 3D scanning and 3D printing as the most notable development in centuries.
“We get a reproduction that is really good,” said Mussi. “No artist can do it. Only the technology can do it.”
Famous for its metal casting, Artworks Foundry has stood by traditional methods since its inception in 1975. Mussi is embracing the opportunities presented by 3D printing and welcomes the partnership with Fathom and Scansite to transform a former impossibility into a current reality.
“What is so unique about this project is the utilization of 3D printing and 3D scanning in an industry which has remained unchanged for over a thousand years,” said Rich Stump, Principal at Fathom.
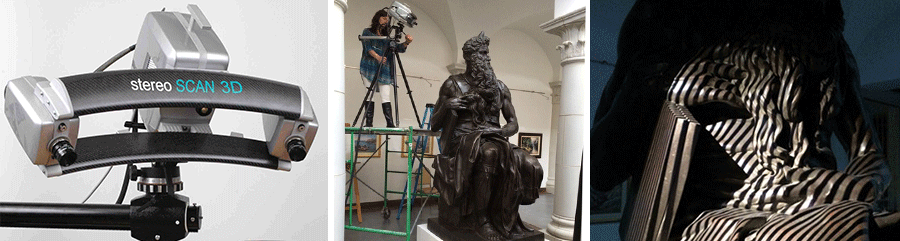
BLENDING INDUSTRY-LEADING TECHNOLOGIES WITH LEGACY METHODS
Renaissance Masters are art liaisons with an official declaration and authorization to reproduce 28 works of Michelangelo. Through the exclusive partnership, permissions granted Scansite on behalf of Renaissance Masters with access to scan 1/1 bronze castings that were made from original molds crafted by the Marinelli Pontifical Foundry in Italy (the successor of a bell-making establishment that dates back to 1040). In the 1930s and 1940s, the foundry made molds of the original statues that resided in Vatican City and other parts of Italy.
After a statue is 3D scanned by Scansite, point cloud data is converted into an STL file format. Fathom, home to experts in additive manufacturing, receives the digital model for review to determine the optimal 3D printing technology, material and orientation. The 3D printed model built on an Objet500 Connex in VeroBlue (PolyJet Technology) is then passed to Artworks Foundry and used in the bronze casting process. Through the “Lost Wax” method, the foundry team can reproduce any artwork in bronze that honors the integrity of the original molds.
For more than 500 years, Michelangelo’s marble sculpture Pietà has been housed in St. Peter’s Basilica. Across the Atlantic Ocean and the entirety of the United States, identical bronze castings now exist in Berkeley, California thanks to the blended use of advanced manufacturing technologies. The accuracy of the replicas is unprecedented.
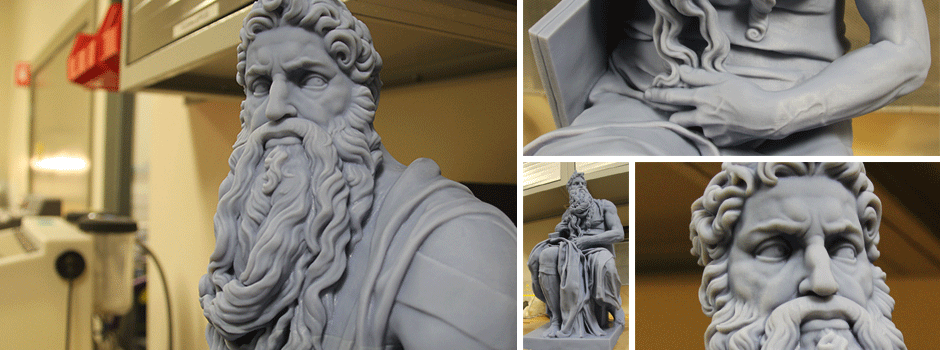
To learn more about the lost wax bronze casting process: artworksfoundry.wordpress.com/lost-wax-process/
To learn more about the 3D scanning process: scansite.com/services/3D-scanning
PRESS MEDIA KIT
For more information on this story, contact Fathom Media Relations.