PEKK Material Option for FDM / / PEKK FAQ
Just last year, the Fathom production team began offering carbon-filled Nylon 12 to meet an increasing demand for high-performing additive material options—and recently, we’ve added another! Our additive manufacturing service customers can also choose PEKK from our wide range of FDM materials. In this featured blog post, Applications Engineer Kaitlyn Bailey answers the most frequently asked questions about this engineering-grade thermoplastic for fused deposition modeling (FDM).
What stands out about this new material option for FDM?
The superior chemical resistance of this material is what really stands out to me—it is resistant to tricky substances like hydraulic oils, solvents, cleaning fluids and fuels. PEKK also has extremely low outgassing, which is needed for space and cleanroom type applications.
When should a designer or engineer consider using PEKK?
PEKK should be kept in mind for parts that require chemical and temperature resistance, high strength and stiffness and ultra-low outgassing. Taking a digital fabrication approach with this durable material allows users to take advantage of FDM in ways not possible with traditional manufacturing methods. For example, build high-strength parts that are more complex and lighter in weight at lower volumes and faster speeds—its really powerful to additively fabricate parts in PEKK because it allows for part consolidation, which ultimately reduces assembly time and overall cost.
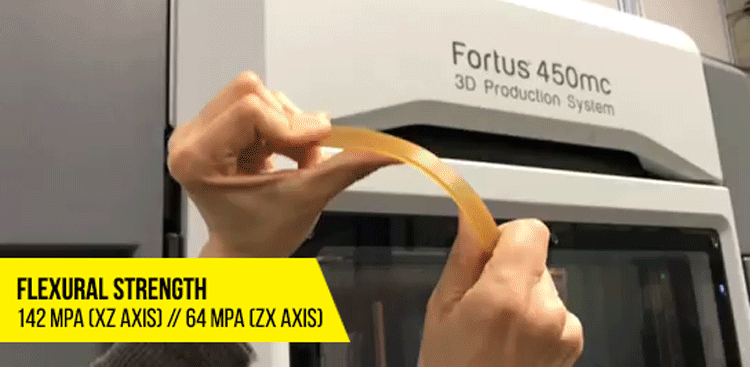
How is the surface quality of this material versus other FDM materials suited for similar application types?
Currently PEKK only runs in 0.010” layer height. This thermoplastic option comes in a natural color and uses breakaway support. Surface finish may be rougher than FDM materials known for aesthetics such as ASA, but should still be appropriate for the industrial and manufacturing applications it was developed for (e.g. harsh environments).
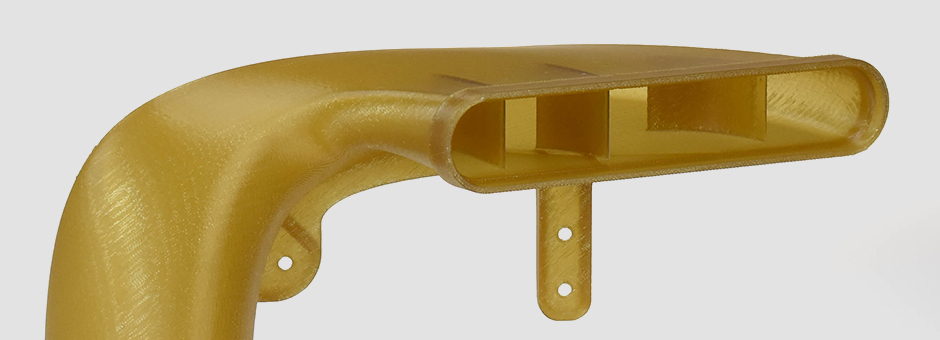
What industries do you see using this material the most?
PEKK is best suited for industries with applications exposed to harsh environments such as automotive, industrial manufacturing, oil/gas (e.g. parts exposed to hydrocarbons), semiconductor, robotics, motor sports (e.g. under the hood) and aerospace. For example, PEKK is especially ideal for aircraft components exposed to jet fuel, oil and hydraulic fluid. Other uses include ducting, housing, clips, brackets and manufacturing aides such as jigs, fixtures, and end-of-arm tooling.
What should be expected regarding cost and lead-time for PEKK?
Considering all of the FDM material options available from Fathom, the price point of PEKK will be most similar to our ULTEM options because of its use in specialized and advanced applications. Customers should expect a lead-time of six business days (if you need to expedite an order, talk with your account manager or customer service representative directly).
Submit 3D CAD Files—Request for Service Quote