Prototype Early, Fail Faster
DESIGNING AND 3D PRINTING RATCHETING STRAPS—35+ Iterative Components for BOOMcast in 5 Days
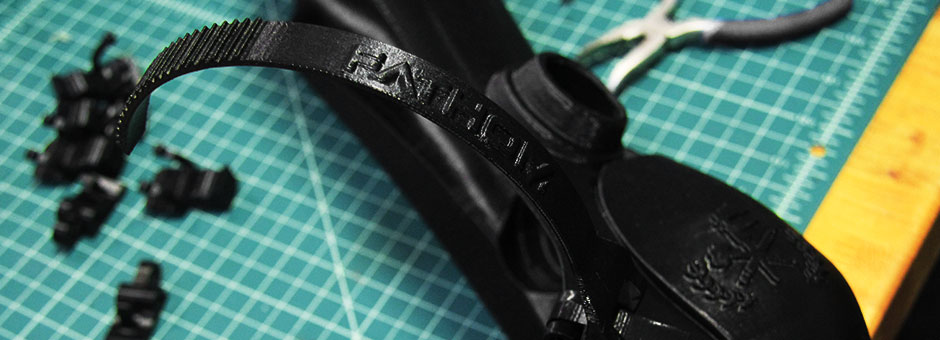
BOOMcast is a modern re-imagining of the medical leg cast—a lightweight 3D printed structure with LEDs, Intel Edison, Bluetooth speakers and integrated sensors that monitor contact pressure.
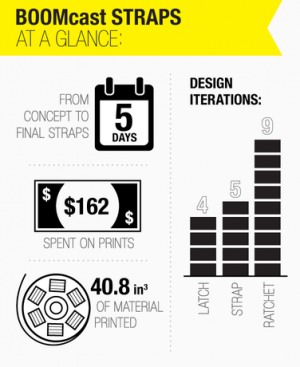
A key feature that makes BOOMcast viable is a set of 3D printed ratcheting straps. To remain adjustable yet weight bearing, BOOMcast needed durable, flexible straps that maintain tension over time. Fathom Applications Engineer Bethany Casarez, utilizing the rapid iterative cycles available through 3D printing, was able to create more than 30 unique iterations of strap components for functional testing before producing the final straps.
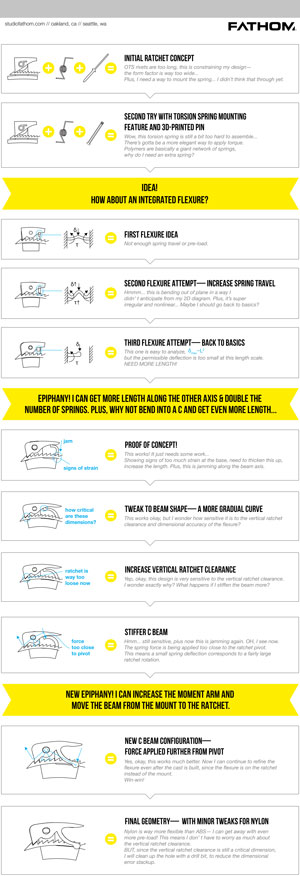
The development of the BOOMcast ratcheting straps displays the timelines available through effectively leveraging additive manufacturing technologies. The process demonstrates the speed, creativity and efficiency you can achieve by integrating design, engineering and production all under the same roof. With a wide range of durable materials and the ability to conduct rapid functional tests, Casarez and the BOOMcast design team were able to develop and refine each aspect of the cast within an extremely tight deadline.
Front-Loaded Design
Taking a front-loaded approach to design means building and testing as soon as possible in the design process. While it can seem counterintuitive to many designers and engineers, one of the most important strategies in agile design is to avoid spending too much time in CAD up front.
BOOMcast’s ratcheting straps were conceived, designed and produced by Casarez in five days. Compared to a traditional process for designing a mechanical assembly, the strap converged to a functional design extremely quickly. In a more traditional development process, the engineer spends a long initial phase developing foundational assumptions—researching existing mechanisms or models and running simulations. Developing an integrated compliant mechanism such as the one in the strap’s ratchet design requires research, careful analysis (such as pseudo-rigid body analysis) and a nonlinear finite element simulation.
Since outsourced prototypes can take weeks or months to turn around, resulting in fewer iteration cycles, it can be months into the development process before simple physical testing uncovers modeling errors or flaws in some of the designer’s underlying beliefs. Moreover, by limiting the design space to a well understood set of models or mechanisms, functional designs begin looking similar, with more unique approaches deemed too risky or unfeasible.
In the design of the BOOMcast ratcheting straps, easy access to production-quality 3D printers enabled a front-loaded design approach. Instead of spending time at the outset developing a model to predict mechanical behavior of the compliant features, design concepts were tested early and often. Rather than waiting days or weeks to receive machined or molded prototypes, Casarez was able to 3D print, test and re-design in a matter of hours, sometimes even minutes.
The strap design was abstracted into six functional components early on to enable parallel development. As the design evolved, the purpose of test prints became more focused. Whereas early prints informed Casarez about the form factor and basic mechanism, later prints focused on refining a specific feature or determining a critical dimension.
In addition, because the team focused on the design’s functionality rather than the suitability for machining or molding, the design was able to evolve away from standard features and venture into more integrated functional design features.
The earliest versions of the BOOMcast ratcheting strap design are similar to traditionally manufactured rollerblade straps, which utilize rivets, a torsion spring and injection molded components. With rapid iterations and testing, the strap quickly evolved to better suit the design requirements of BOOMcast and the additive manufacturing process. Each of the components of the strap design went through three to eight full design iterations.
The components were all designed in parallel with other BOOMcast features and were created in such a way that the most critical components—the release button, strap and latch—could continue to be refined and improved even after the primary cast structure was printed.
3D Printed Prototype Fabrication
For much of the design process, two uPrint SE Plusdesktop 3D printers were used to rapidly prototype different aspects of the ratcheting strap design. The ease of access and high dimensional accuracy of the uPrints enabled many quick iterative tests without tying up limited resources. Using the two uPrints, Casarez quickly honed in on the form factor of each component and identified critical-to-function features and dimensions through functional testing. Casarez was able to print, test and re-design components in a matter of hours and sometimes minutes, by running many small builds and testing while working on CAD for other components in parallel. Quick prints and tests were carried out during the day to learn as much as possible about the design during work hours. Longer builds were scheduled overnight so they would be ready the next morning.
Once each component was mostly refined the straps were printed in Nylon, a highly durable FDM thermoplastic, on a Fortus 450. The components were tested in the end-use material and the critical-to-function dimensions for the compliant mechanisms were slightly adjusted. With one final re-print of the latch and release button, the BOOMcast functional ratcheting strap was complete.
The Final 3D Printed Ratchet Strap
One of the most unique aspects of the ratcheting strap is the extremely flexible body, which contours to the cast when tightened. The flexibility and durability of the strap is due to the high elongation at break of FDM Nylon 12 (30% compared to 3-9% for most other rigid FDM plastics). These qualities, combined with the excellent fatigue resistance of the material, make it suitable for durable compliant mechanisms.
Instead of utilizing a torsion spring, the ratcheting straps for BOOMcast utilize an integrated compliant mechanism to spring-load the ratchet, enabling it to maintain tension without loosening over time—a critical necessity for a functional weight-bearing cast. All pivoting components are connected through strong, easy-to-assemble snap-in pins inspired by those used in open source prosthetic designs from Enable Community Foundation, a global 3D printed prosthetic community of volunteers.
The final 3D printed strap design uses 3.5 in3 of material, costs $12.50 and 3D prints in 3 hours. The strap’s design is modular and open source, so engineers and designers anywhere can download it, modify it and integrate it into future designs for other casts, prosthetics, braces or custom athletic gear (view on Instructables).
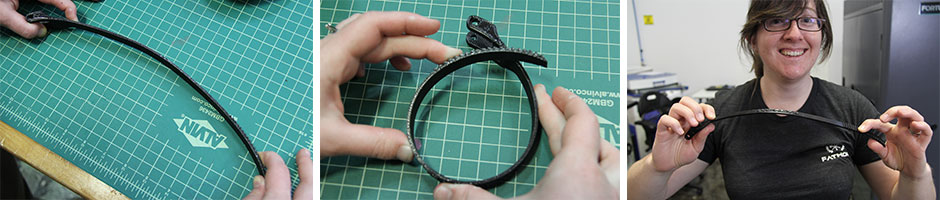
Accelerating Product Development
By effectively leveraging additive manufacturing technologies and techniques, Fathom and Casarez were able to create many innovative design features on an extremely short timeline.
BOOMcast is just one of many projects that exhibit how Fathom is changing the way products are designed and manufactured. To see other ways Fathom is utilizing 3D printing and advanced manufacturing technologies to accelerate product development and push the boundaries of product viability, check out our many blog posts or start a conversation with an account manager today.
Have a Fortus 3D printer? Download the open source design files and print BOOMcast for yourself.