Panel on Prototyping Wearables
At the upcoming Wearables & IOT TechCon in San Jose, Fathom Advanced Technology Manager Michael Duncan will be a panel speaker during a Monday session, Tips for Rapid Prototyping Your Wearable. He will focus largely on his lengthy experience in helping companies from Silicon Valley titans to startups through challenging phases of product development. As a quick preview of the types of stories his presentation will include, we chatted with Michael about one of his past projects, a wearable lens device he helped develop with Intel.
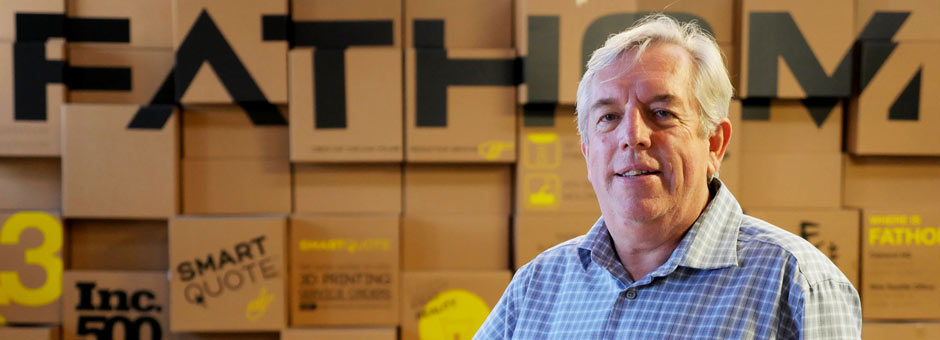
Q&A WITH MICHAEL DUNCAN Rapidly Prototyping Wearables
Can you tell us about a wearables project you worked on that required some alternative thinking to achieve a desired result?
Duncan—I worked on a project with Intel that was largely a wearable project. Intel was creating a product that integrated a lens, but their designers had much more experience in designing electronic products than they did with lens design.
We helped to get the resin manufacturers for the lens materials and a tool design that allowed us to have flexibility in lens development. We were able to shoot that plastic and try some different things and we literally turned the lens into the back of the device.
The lenses that are typically used on a device like that are really small cylindrical plastic lenses that are premade and they are either mounted on the device or mounted on a substrate so that they had a focal length or a center to the receiver part of the device. That is pretty tough to accommodate in a wearable because everything is moving around and there is no way to guarantee that you’re absolutely parallel to the device. So, what we did was take the back of the enclosure design and integrated the lens directly into it. To maintain the proper parallax, where the two surfaces have to be parallel, we used a small metal insert for the middle of the DMLS tool. The tool was adjustable in order to create different thicknesses, which would create a parallel process.
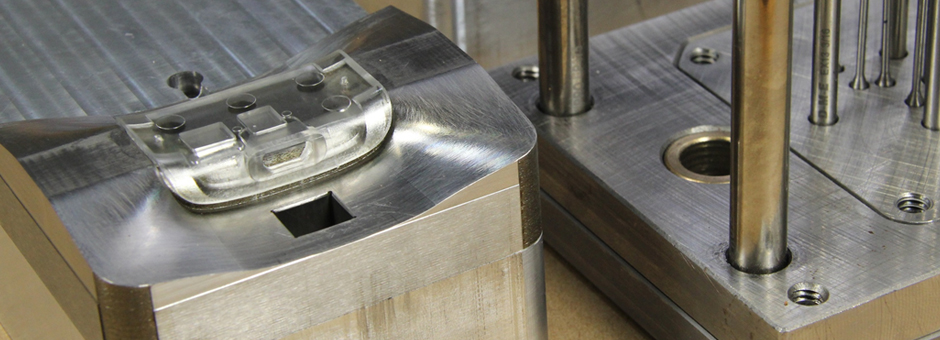
We designed the tool, pulled in the back enclosure and molded those two pieces together to solve the problem—and, it more than just solved the problem, Intel initially ran 25,000 parts for the marketing of that product.
It really blew them away because they didn’t have to grapple with the lens design and incorporation anymore—the lens was part of the back enclosure and our process allowed us to maintain the parallax.
The quirkiness of this project was that Intel was initially looking for help on how to prep their enclosure for manufacturing, but the real challenge at hand turned out to be how would the lens be mounted.”
How did you know that integrating the lens into the enclosure’s design would work out so well?
Duncan—I worked for Inspector Physics when I first came to Oregon around late 1994. And Laser Light, another place I worked, was all about lenses and mirrors. I learned a lot about how to produce and optimize lenses and a lot about the plastic used for lens-like materials in an injection molding situation. Being a project designer, I understood components, especially for a wearable. To me, it was a natural solution to put the two together.
With previous companies that I’ve worked for, wearables were just coming into light, so to speak. With Garmin, I helped with the first Nike watches, so we learned about prototyping complete watch systems to get the precise industrial design communicated.
What are you looking forward to most in the wearables industry? How does 3D printing best fit into the product development of wearables?
Duncan—The whole industry has come a long way with durability, ruggedness and material applications. I think where Fathom is really well placed is that we can take a concept, iterate designs, merge functionalities and help create a design that’s optimized for manufacturing. Rapid prototyping has really altered the product development timeline.
One of our customers used to have an eight- to ten-week design-to-prototype cycle and they are being asked by their clients for half of that. Now we help them to do many of the same things in less than four weeks. It’s very exciting to help clients like that create products so rapidly and it’s exactly what we are geared to do.
To start a conversation about a project or discuss a quote for 3D printing, CNC machining, urethane casting, rapid tooling, injection molding or R&D contract services, send us a request for quote. Fathom is also an authorized partner of Stratasys. Get a quote for a professional 3D printer today!