Not Your Ordinary Slinky
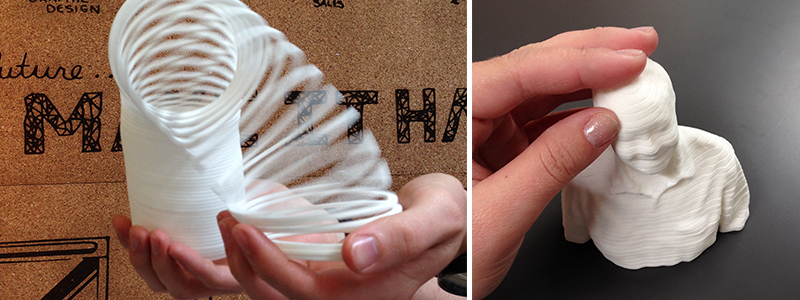
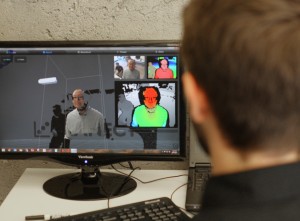
One of our most popular posts on social media this month was of a slinky, but not the ordinary kind made using traditional manufacturing methods. Instead, this slinky was created using a popular type of additive manufacturing called Selective Laser Sintering or SLS, one of Fathom’s many in-house production center services. First, the team built a plain slinky, a great sample piece that demonstrated the unique capabilities of SLS and the material durability (check out the video posted on Instagram). Not long after it circled around the office, the design team came up with the idea of turning a CAD file of a 3D scanned employee into a custom, one-of-a-kind slinky. Thats what really caught the attention of our online followers, a few of which asked some great questions! To learn more about this project, we met with Veronica De La Rosa, an industrial designer on the Fathom design team.
Tell us about this build, from concept to completion. Veronica: The idea for this sample part came to us one day when we were asked to design a piece that would best show off the capabilities of the SLS machine and the strength and flexibility of the nylon material we offer (PA2200). SLS is a type of additive manufacturing which makes use of a high power optic laser. Designs come to life as the laser fuses small powder particles together layer by layer. Fathom’s customers opt for this technology when creating complex geometric parts that must meet high durability requirements.
Our Mechanical Engineer, Cole Hartman, engineered the first design by splitting a cylinder with an extruded helix. At that same time, our support team was 3D scanning Fathom employees and printing the busts on one of our PolyJet-based 3D printers. We thought, why not turn one of those scans into a slinky! Instead of splitting a cylinder with an extruded helix, we used a scan of Fathom’s Advanced Engineering Project Manager, Alric Lam.
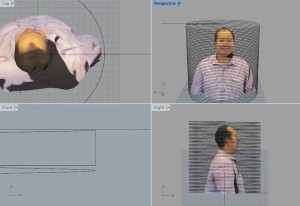
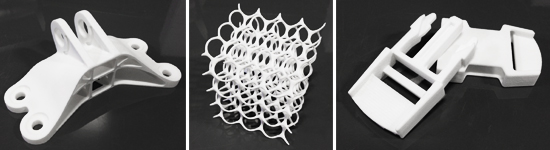
SLS makes it possible to achieve durable, versatile, functional parts, as well as, complex geometric shapes. Originally designed for building prototypes, it has now evolved in a preferred method for creating end-use parts in small to large volumes.
Dennis Harroun on Facebook wrote, Id love to know how it was modeled. Ive been seeing this lately. I use Maya and Im drawing a blank as to any methods to achieve such shapes. Veronica: You can pretty much “slinkify” any object by taking any solid form and giving it a thickness. Then, you Boolean it with a helix that also has thickness and depth. This should result in a continuous slice of the model.
Carrie Sloane on Facebook wrote, Does it function as a slinky, still? It seems like it would lose some of that because its not circular anymore. Veronica: The human bust doesnt act like the traditional slinky design mainly because it is not a tube and the diameter of the head is quite smaller than the base of the chest, but its still fun to play with (check out the video posted on Instagram). You can find functional slinky designs in different form factors. If you do a quick search online, there are heart and star shaped versions for download. It would be interesting to test how irregular of a form you can “slinkify” without losing the slinky mechanics.
We hope that youll try to create a slinky of your own! Send us a photo of your design, or, have us print it for you and we will feature it on our blog. Using our online ordering tool, you can upload your CAD model on smartquote.studiofathom.com and select the SLS option. Have a question? Contact one of our additive manufacturing specialists using this form.