A customer came to Fathom with a complex part that required complex tooling for a racetrack-style scoreboard panel. Fathom recommended STEP technology, a groundbreaking 3DP technology that is able to print injection mold-like parts in days instead of weeks, with similar functional properties and surface finish of injection molded ABS.
43%
Cost Savings
63%
Time Savings
Challenge //
Daktronics, a world leader in designing and manufacturing electronic scoreboards, programmable display systems and large-screen video displays, faced a challenge in designing a new LED panel for a project. Due to the racetrack-style scoreboard panels in the corner sections, multiple individual molds with a high degree of tool automation would be needed to meet the requirements of the customer. Instead, Fathom was able to use STEP technology to create these parts.
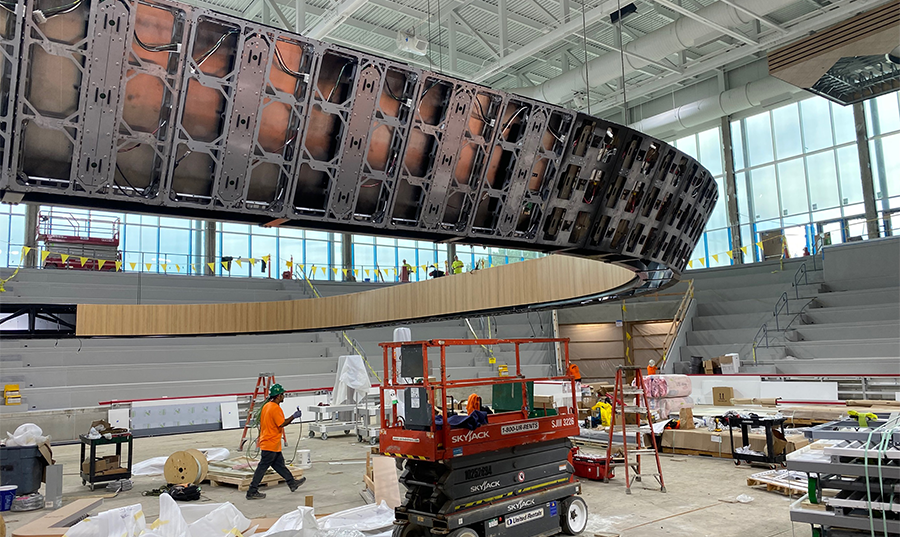
Solution //
With the deployment of STEP technology, quick and smooth DFAM (Design for Additive Manufacturing) for clip designs saved time and money (due to no costly Design of Experiments (DOEs) with tooling designs).
Speed vs Injection Molding
Using injection molding, the process would have included complex tooling, a 8-16+ week overseas or 12-19 weeks+ domestic timeframe and required tooling with two lifters per clip feature which would be prone to breakage due to the size, then part validation (1-2 weeks). If parts weren’t up to spec, the cycle would repeat.
Agility
One of the big advantages of Evolve is it allows quick iterations WITHOUT the tedious tooling/validation exercise typical to injection molding and yet can produce injection molding (or better) quality parts.
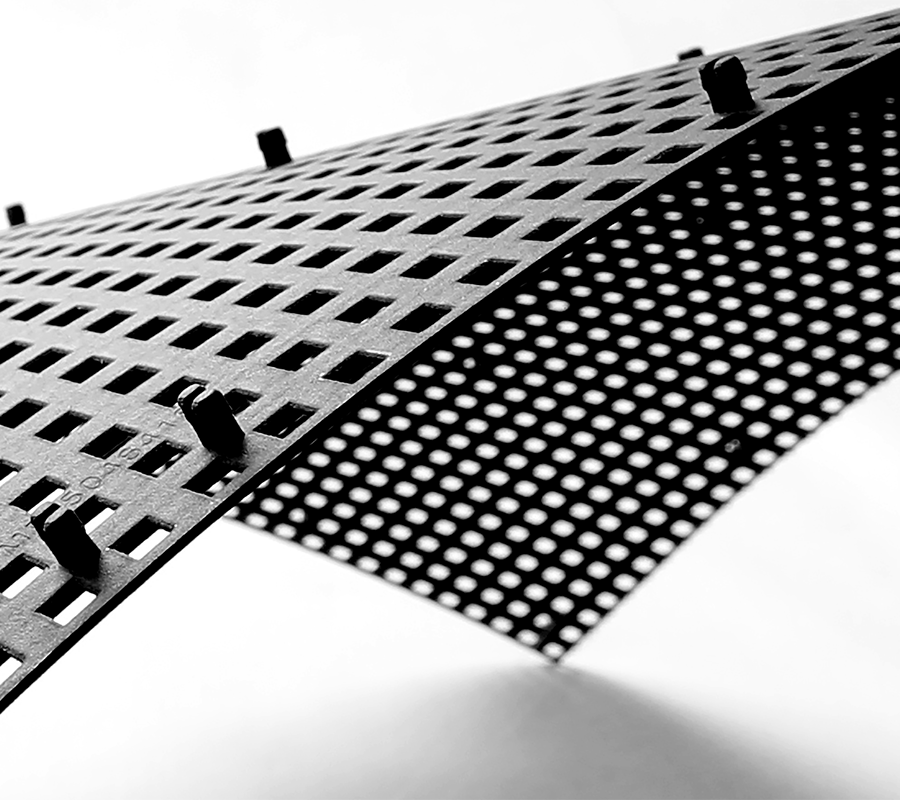
Results //
Fathom’s entrenched customer relationships, deep industry expertise, and outcome-focused approach enables the advancement of additive STEP technology for the production of plastic parts. This is a significant and disruptive innovation for the additive manufacturing industry as it gains ground against traditional manufacturing methods. STEP technology enables the production of thermoplastic parts within hours or days without compromising on quality, throughput, scalability or cost, a significant time advantage over the typical multi- month lead time for traditional injection molding tools and parts. STEP technology is also an environmentally responsible manufacturing process that reduces carbon footprint by eliminating the need for tooling as well as by reducing warehousing and transportation logistics.
For Daktronics, using STEP resulted in time and cost savings – and an attractive new method of product development for their company as they continue to look at ways to engage Fathom and STEP for their future projects.
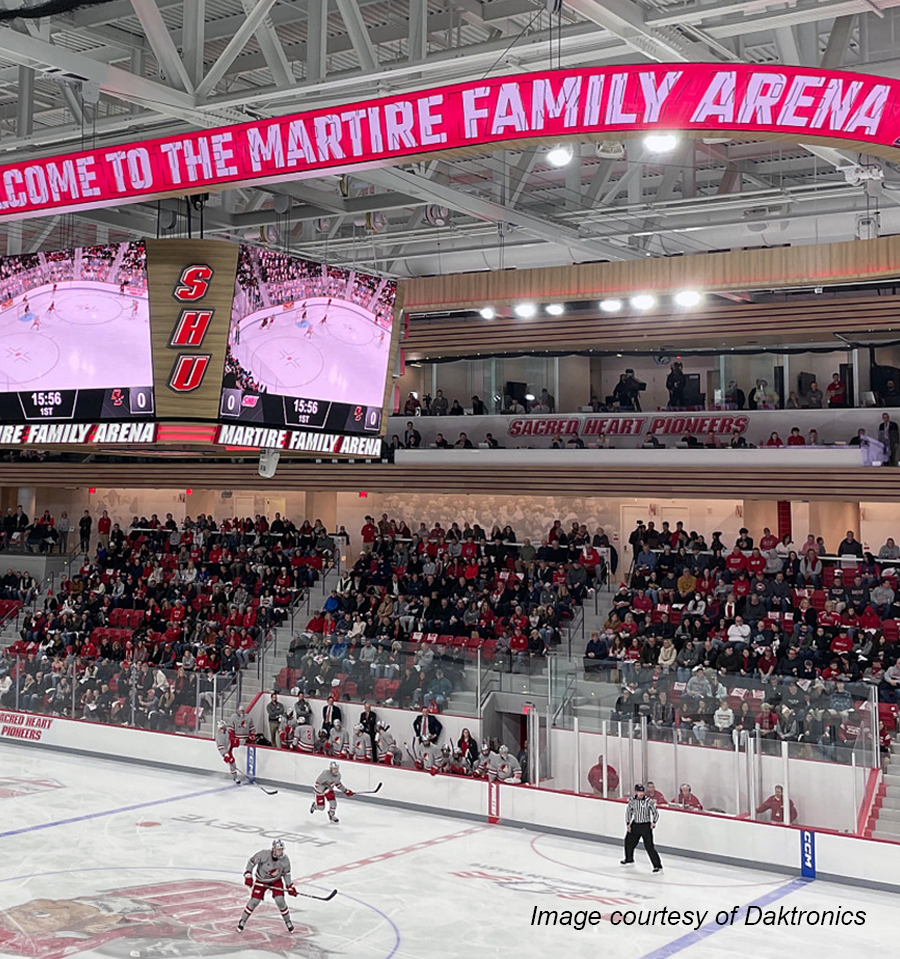
Talk to an Expert
Working with Fathom means easy access to Additive and Advanced manufacturing experts. Contact us today, and let’s transform the future of manufacturing together!