New FDM Material ASA (Acrylonitrile Styrene Acrylate)
Every day, Fathom leverages an in-house team of design, engineering and manufacturing experts to innovatively compress industry standard lead-times by using advanced manufacturing technologies so our customers products go to market faster and more efficiently. Bethany Casarez, an Applications Engineer at Fathom, has access to the most advanced additive manufacturing technologies on the market. Casarez spends much of her time sharing this expert knowledge with companies all across the country, as well as with the world through the Fathom blog. In this material review, she examines one of the latest material options from Stratasys: ASA, a thermoplastic available in 10 colors for FDM-based 3D printers.
How does ASA compare to other materials commonly utilized for end-use products and prototypes put through rigorous physical tests?
Casarez: ASA (Acrylonitrile Styrene Acrylate) is very similar in mechanical performance to ABS (Acrylonitrile Butadiene Styrene), which is the most widely used plastic in the injection molding industry and one of the most common 3D printing materials. ASA is actually better suited to prolonged use than ABS because it has superior resistance to ultraviolet light degradation. This is true in both 3D printing and injection molding.
In essence, ASA will maintain its color, surface quality and mechanical performance under prolonged UV exposure longer than ABS. ASA also has very similar chemical and heat resistance to ABS and has been widely adopted in the automotive industry for both injection molding and 3D printing applications. Specific to 3D printing materials for FDM (Fused Deposition Modeling), ASA has better aesthetic and mechanical properties than ABS, including a better Z-strength ratio (meaning it has better inter-layer adhesion).
Post-processing methods are often used to give 3D printed models the look and feel of final products for form and fit testing — what types of finishing techniques work best with ASA?
Casarez: Most finishing techniques that work for ABS will also work for ASA. This includes vapor polishing, vapor smoothing with acetone, mechanical vibration polishing, hand sanding, filling, priming, painting, hydrographic printing and metal coating through vacuum metallization or electroplating. Since ABS and ASA are both variations of a Styrene-Acrylonitrile copolymer, they behave very similarly for most finishing processes.
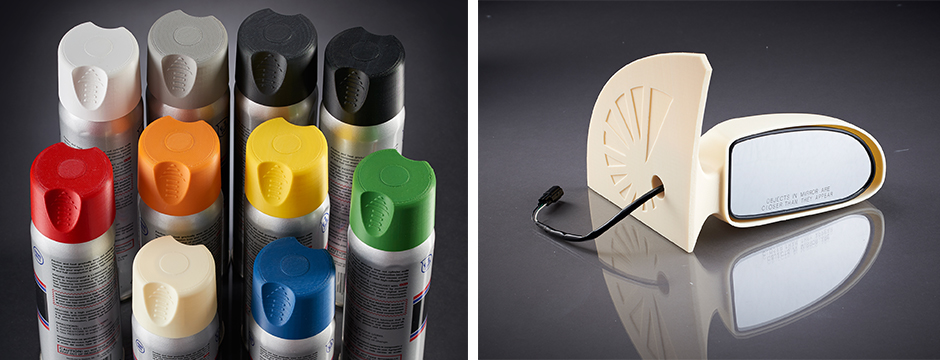
ABS is comparable to ASA in strength and heat resistance and is a popular choice for many FDM builds — in what situations would you recommend ASA over ABS?
Casarez: ASA is slightly superior to ABS in both mechanical performance and aesthetic quality. It is better suited to outdoor applications and it is generally better suited for end-use models since it will not degrade as quickly under UV exposure. If your model will be exposed to sunlight for a significant period of time, ASA is definitely a better choice. ASA is also currently available in more color options than ABS-M30 on the Fortus 3D printing platform (view matrix of 3D printing systems by Fathom).
System Availability
Fortus 360mc
Fortus 380mc
Fortus 400mc
Fortus 450mc
Fortus 900mc
Layer Thickness
0.013 inch (0.330 mm)
0.010 inch (0.254 mm)
0.007 inch (0.178 mm)
0.005 inch (0.127 mm)
Support Structure
Soluble
ASA also has the best bridging properties of any FDM material (view page 3 of the material chart for mechanical properties). This means that you can print parts with a sparser interior fill than with ABS or other FDM plastics, which enables greater material savings for applications where cost and/or weight are critical.
Many companies and individuals may choose to replace ASA as their go-to 3D printing material. For applications in which UV exposure is not an issue, some people may continue to choose ABS due to system availability or because they are more familiar with it—ABS is still a great general prototyping material, especially for an office environment.
One of the benefits of FDM technology is the ability to use 3D printed models as end-use parts, not just for prototyping — given ASA’s UV resistance, what are some practical applications for this material?
Casarez: ASA is great for products that require long-lasting strength and aesthetics. We recently used ASA to build a prosthetic hand for a child in collaboration with the e-NABLE community (see below—the part was dyed to achieve the desired color). We chose ASA for a combination of its UV resistance, aesthetics and strength. Automotive companies use ASA to prototype exterior vehicle components and it can be used for many outdoor applications such as bike accessories, garden tools, sports equipment and camera mounts. ASA is currently available in 10 colors (red, orange, yellow, green, blue, light gray, dark gray, black, white and ivory), which will remain vibrant over time, making it great for outdoor signage and decorations, too.

Stratasys frequently releases new additive manufacturing systems and materials with increasingly refined capabilities — what does the implementation of the new ASA material say about the future of additive manufacturing?
Casarez: In the additive manufacturing space, you often hear of game changing technologies coming to market. While these announcements can be exciting to hear about, many of them only really promise the potential of new applications and some disappoint. I actually think some of the most impactful changes occurring in the additive manufacturing industry are the incremental improvements that are being made to established technologies and systems. Its exciting to be at Fathom because our team has that hands-on experience with advanced technologies and materials. That practical perspective, combined with an in-house research and engineering team focused on the material needs of our industry-leading customers, gives us great insight on the future of additive manufacturing and how we will get there.
The release of ASA from Stratasys represents years of research and development to improve some of the biggest shortcomings of the FDM technology—surface finish, inter-layer adhesion and mechanical durability over time. These improvements, while not revolutionary to the industry, will continue to push the boundaries of new applications that are possible with additive manufacturing. I think, in the coming years, we will continue to see improvements in materials that enable new applications. I also think we will continue to see improvements in build time and throughput that will make production of end-use parts through additive manufacturing more and more cost competitive.
Start a conversation with Fathom—
-
Looking to purchase a professional 3D printer (FDM & PolyJet)? Get a quote!
-
Need a quote for services (3D printing, CNC machining, urethane casting and injection molding)? Send us a 3D CAD file!