How to Select an EDM Machine Shop
EDM machining requires a combination of precision equipment and experienced operators. Here’s why you should select Fathom for your EDM machine shop.
What To Look For
In A Wire EDM Machine Shop
Are you looking for an EDM machine shop that can help you produce precision metal parts? Here are some criteria to keep in mind:
Capabilities & Equipment
What EDM machining equipment and technology does the shop have in place to support your needs? In addition to wire EDM cutting, do they also support sinker and small-hole EDM?
Materials
What types of materials can the EDM machine shop process? Only electrically conductive metals can be cut using wire EDM. Some materials commonly processed using EDM machining include:
- Aluminum
- Brass
- Stainless steel
- Steel
- Titanium
- Nickel
- Bronze
- Copper
Applications & Experience
How much experience does the EDM machine shop have in producing parts in the industries and applications that matter the most to you? Can they provide you with examples of relevant work they’ve done? Do they have well-defined case studies for projects like yours? Can they provide you with relevant references – customers who have successfully worked with them on similar EDM machining projects?
Personnel
Who are their most experienced EDM machine operators? Can you meet them? What’s your first impression of their knowledge and skills?
Processes & Quality Control
What processes does the shop have in place to ensure that new projects entering their system are handled efficiently? How do they communicate progress reports to customers? How frequently and at what level of detail? Do they use any digital tools to streamline collaboration and keep projects moving smoothly? What measures do they have in place to avoid production errors? What certifications do they have?
Capacity
What is the shop’s sweet spot from a production standpoint? Can they accommodate prototype projects? Are they best suited for low-volume, mid-volume or high-volume production EDM machining? Does the shop appear to have enough capacity, equipment and experienced personnel to take on your project?
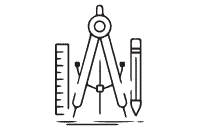
Design Assistance
Is the EDM machine shop able to help you optimize your part design, material selection and production processes to help save you money and deliver high-quality parts consistently? Which CAD/CAM software does the shop support? Does this match up with the software and file types you work with?
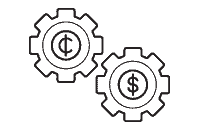
Financial Stability
Is the shop profitable? Or is it in the midst of financial challenges? If the shop is struggling, that could limit its ability to purchase material for your project.
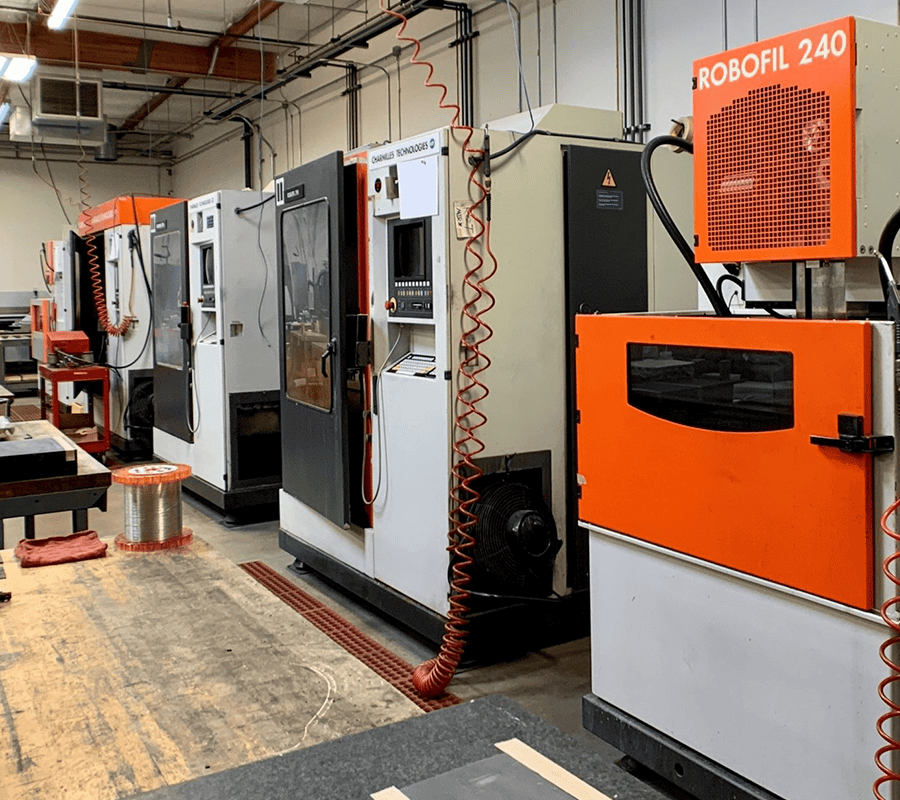
Fathom’s Locations
for Wire EDM Surface Finishing
Fathom’s nationwide network has several locations across the U.S. that offer wire EDM services:
Arizona //
Micropulse West
444 W. 21st St. Ste. 101
Tempe, AZ 85282
Illinois //
Summit Plastics & Tooling
1207 Adams Drive
McHenry, IL 60051
Precision Process Corporation
1401 Brummel Avenue
Elk Grove, IL 60007
Texas //
Centex Machining
1513 Sam Bass Rd.
Round Rock, TX 78660
New York //
Incodema
1920 Slaterville Rd.
Ithaca, NY 14850
Fathom’s Wire EDM
Specifications and Tolerances
Material Thickness | Tolerance | Kerf | Part Volume | Set Up Cost | Lead Time ** | Notes |
---|---|---|---|---|---|---|
up to 15 inches thick | 0.0002" | 0.009" to 0.016 | 1-200 Is Best | Low | 10-15 days | Conductive Metals, Carbon |
Fathom’s Wire EDM
Materials List
- Copper
- Carbide
- Tungsten
- Bronze
- Carbon steel
- Inconel
- Stainless steel
- Hastelloy
- Kovar
- Titanium
- Carbon graphite
- High alloy steel
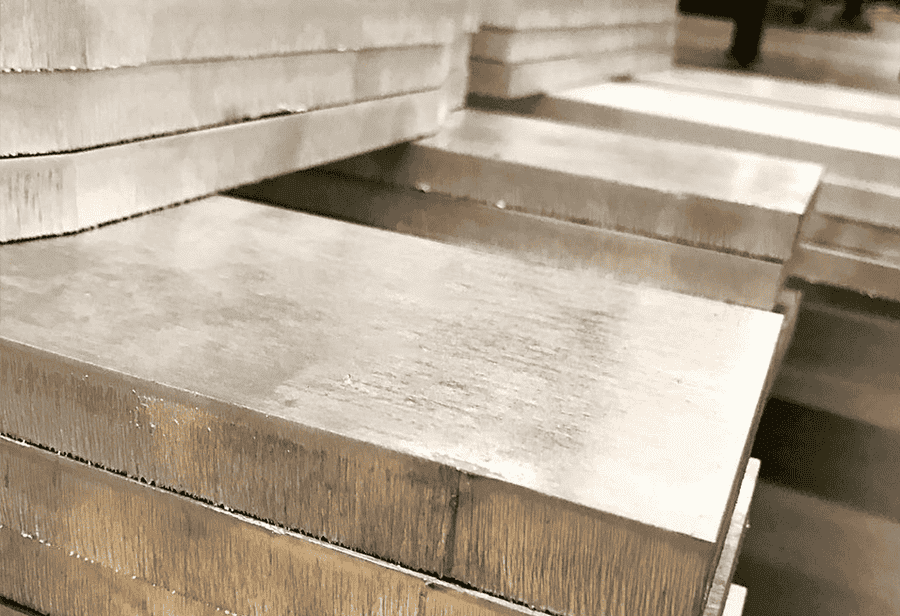
Wire EDM Surface Finishing
Processes
Some finishing may be required on wire EDM parts even though the process can produce a smooth, mirror-like finish. Common finishing processes for wire EDM parts include:
Deburring // Wire and sinker EDM produces features that are burr-free, eliminating the need for costly and time-consuming manual deburring operations.
Painting // Powder coating, liquid coating or e-coating may all be used during the painting process. During powder coating, the powder is electrostatically charged, leaving a scratch-resistant and even coat on the metal part. Liquid coating uses wet paint to coat a surface. E-coating is the process of dipping a metal part into a bath of paint where the part and paint are electrified, causing the paint to adhere to the part.
Transfers // The transfer process uses a heated press to apply a design to a part. Transferring can also be used to add a design that will later be engraved on the part. Transfers are often used to add labels or decorative designs to a part.
Assembly // During assembly, a set of smaller parts are joined together using fasteners or bonding procedures that may or may not be permanent. Assembly is used to make a larger piece from smaller units.
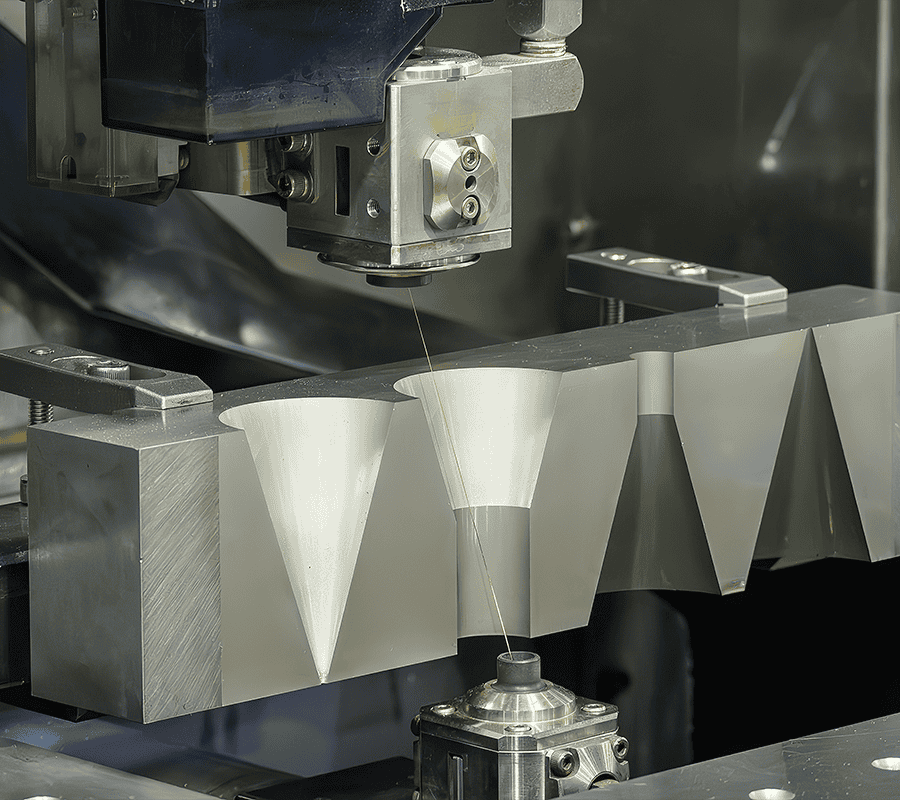
Why Choose Fathom for EDM Machining?
Accelerate Your Project with Wire EDM Cutting by Fathom
The Fathom team has extensive experience cutting parts with wire EDM and getting the highest quality results.
Our Tempe location is one of the premier shops for wire EDM machine shops in the U.S. and has been producing high-quality parts using this technology for over 20 years.
We do tight-tolerance wire EDM cutting for customers in a variety of industries, including automotive, medical, aerospace, satellite, solar and firearms.
Contact us about your sheet metal fabrication and prototyping needs, large or small.