Conventional tooling and injection molding in a classroom or lab environment presents many challenges—access to highly specialized equipment, time, doctorate-level training, close supervision and more. Using a combination of 3D printing and off-the-shelf parts, Fathom’s Director of Research Carlo Quiñonez envisioned an innovative method of producing silicone rubber parts to improve the speed, ease and cost-effectiveness of the process. To see how he reimagined this procedure using the design freedom of 3D printing technologies and materials, check out the first episode of Fathom’s original web series What Can You Fathom?
INTRODUCING REACTION INJECTION MOLDING (RIM) MOLDING By Fathom’s Director of Research
Reaction injection molding (RIM) is similar to traditional injection molding (IM); the key difference is what is being injected. In conventional IM, a polymer is melted, enabling it to flow into the mold. As the polymer cools, it solidifies in the desired shape. In RIM, the polymer exists as a liquid at room temperature, then solidifies after a chemical reaction occurs inside the mold.
The tool system produced in the video is used to make the consumable portion of an automated apparatus for testing the toxicity of potential drugs. The mold halves were printed using PolyJet material to take advantage of the technology’s high resolution for critical details. Other parts were printed in FDM as mechanical properties were important, but resolution wasn’t essential.
In addition to the two mold halves, the system includes components to help eject parts from the molds, as well as a fixture so the parts can be cast reliably. The fixture orients the mold to facilitate proper ventilation and ensures a complete fill.
This system allows lab assistants of any experience level, including college undergraduates, to make clear, bubble-free silicone rubber parts with a 90% success rate. Work-study students—often the ones assigned to this type of work—can achieve this by following simple written instructions without supervision. Conventional methods often result in a success rate closer to 50%, even with users who have a PhD-level skillset in the field.
What’s more, the only specialized equipment required is a 3D printer. This significantly improves the reproducibility, allowing anyone to easily replicate the designs.
This tool system was developed to make a silicone rubber parts with a very specific form-factor, but the general concept of molding silicone rubber parts using 3D printed molds and parts is broadly applicable. Additive manufacturing has the biggest impact when users can reimagine and optimize entire processes for the technology, rather than trying to figure out how to simply insert 3D printing to an existing process.
In the case of reaction injection molding, design iterations proceed much more quickly since new molds can be 3D printed overnight, whereas the conventional approach can take weeks. Since developing parts for automated laboratory testing requires a lot of trial and error, speeding up the iteration process makes a significant difference.
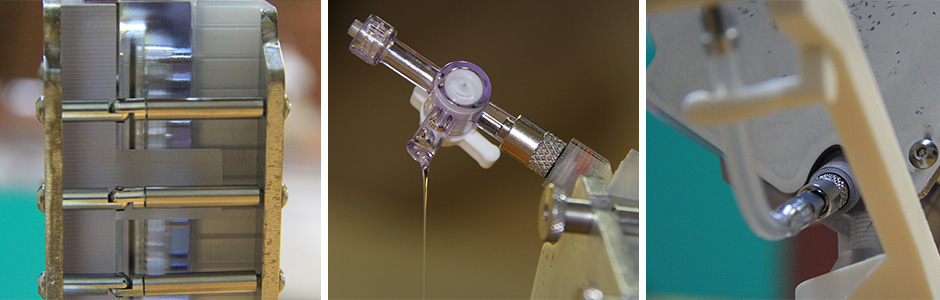
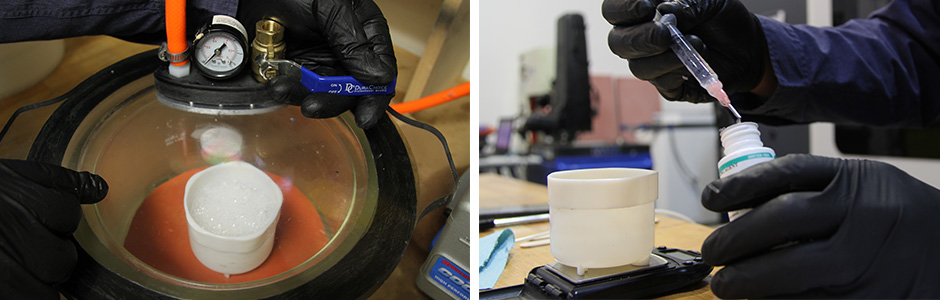
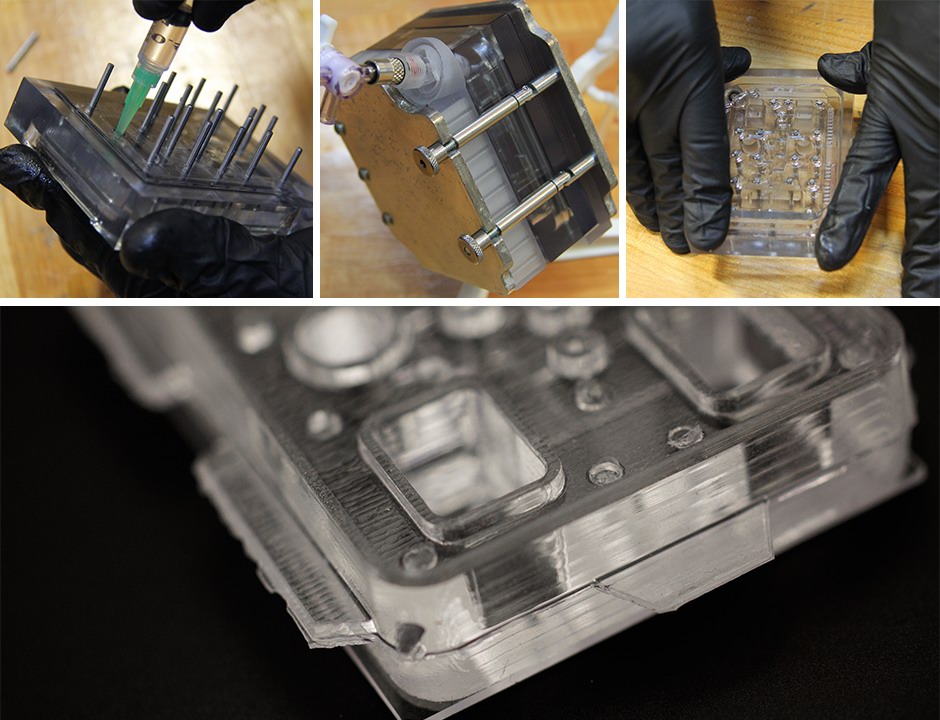
Have a question on how additive manufacturing can improve your traditional manufacturing project? Start a conversation here.